Understanding IP68 Waterproof Electrical Connectors

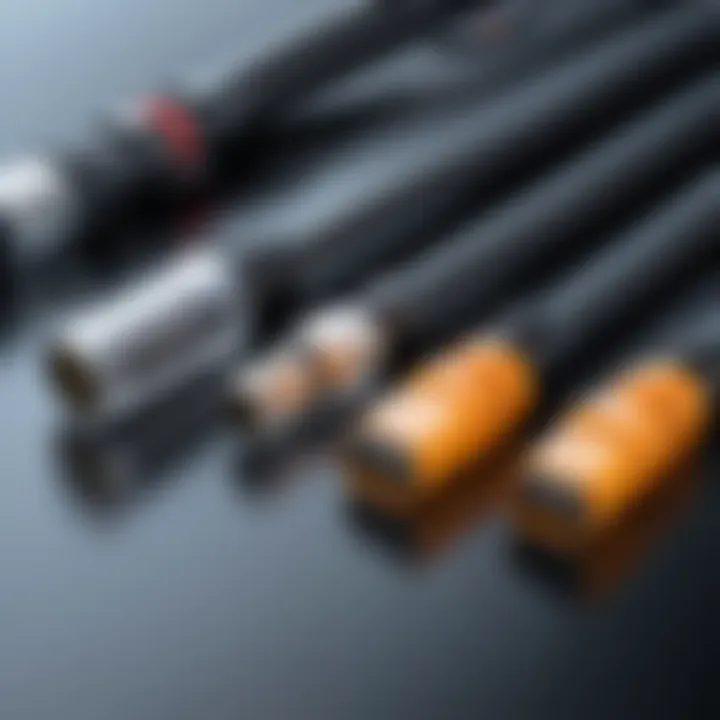
Intro
In today's technological landscape, the demand for reliable connectivity solutions is paramount. This is especially true for electrical cable connectors, which form the backbone of countless systems across various industries. Among them, IP68 waterproof electrical cable connectors stand out due to their robust design and ability to endure harsh environmental conditions.
Understanding the significance of these connectors is essential for a range of users, from tech enthusiasts to industry professionals. The focus of this article will be on the functional aspects, specifications, and applications of IP68 connectors, providing a comprehensive guide for anyone seeking to enhance their knowledge in this area.
Technical Specifications
Detailed Product Specs
IP68 rated connectors are known for their superior performance in environments where exposure to dust and water is inevitable. To achieve this rating, connectors must withstand submersion in water up to a certain depth and duration, typically 1 meter for up to 30 minutes. This level of waterproofing is crucial for devices used in marine settings, outdoor installations, and other challenging environments.
Furthermore, the materials used in manufacturing these connectors play a vital role in their effectiveness. Common materials include polycarbonate and elastomer seals that ensure longevity and durability.
Performance Metrics
Performance metrics for IP68 connectors include:
- Water Ingress Protection: must withstand sustained immersion in water.
- Dust Ingress Protection: effectively prevents dust from entering the connector.
- Temperature Range: typically operational between -40°C to +85°C.
These metrics ensure that IP68 connectors perform optimally in various applications, without compromising reliability.
Compatibility Information
IP68 connectors must be compatible with the systems they integrate into. This involves checking for appropriate pin configurations, voltage ratings, and material compatibility. Users should always verify that the selected connector matches their system's specifications to ensure maximum efficacy.
Practical Applications
Use Cases for Different Users
There are numerous scenarios where IP68 waterproof electrical connectors have become indispensable:
- Marine Applications: Used in boats and ships to connect electrical systems, preventing water damage.
- Outdoor Equipment: Essential for garden tools, lighting, and power tools exposed to the elements.
- Industrial Settings: Often found in manufacturing plants where moisture is prevalent.
Recommended Configurations
When selecting a configuration, consider the following:
- Environment: Where will the connector be used?
- Load Requirements: How much power needs to pass through?
- Number of Connectors: Assess the total number required for the installation.
Multi-Platform Performances
These connectors are versatile and suitable for multiple platforms, including:
- Consumer Electronics: Smartphones, outdoor speakers, and more.
- Automotive Applications: Sealed connectors used in electric vehicles.
- Networking Equipment: Critical for ensuring uninterrupted data transmission in outdoor installations.
Latest Trends
Industry Developments
With advancements in technology, the manufacturing processes for IP68 connectors are evolving. There is an increased focus on sustainability and using recyclable materials without compromising performance.
Emerging Technologies
Technologies such as smart connectors are emerging, offering enhanced features like data transmission capabilities alongside waterproof properties. This trend is reshaping how connections are established in various devices.
Future Predictions
The growth in IoT devices is likely to drive demand for IP68 connectors further. As more devices become connected, the necessity for reliable waterproof connections will only increase.
Buying Guides
Recommended Products
When considering IP68 connectors, it's important to select brands known for quality, such as Amphenol, TE Connectivity, and Molex. These manufacturers offer a wide range of connectors suitable for varying applications.
Purchasing Tips
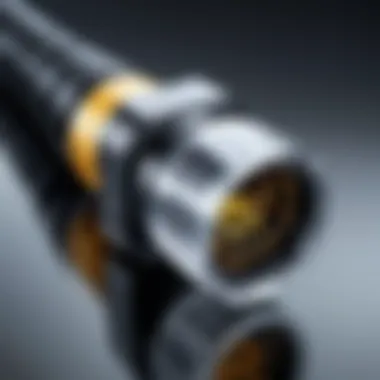
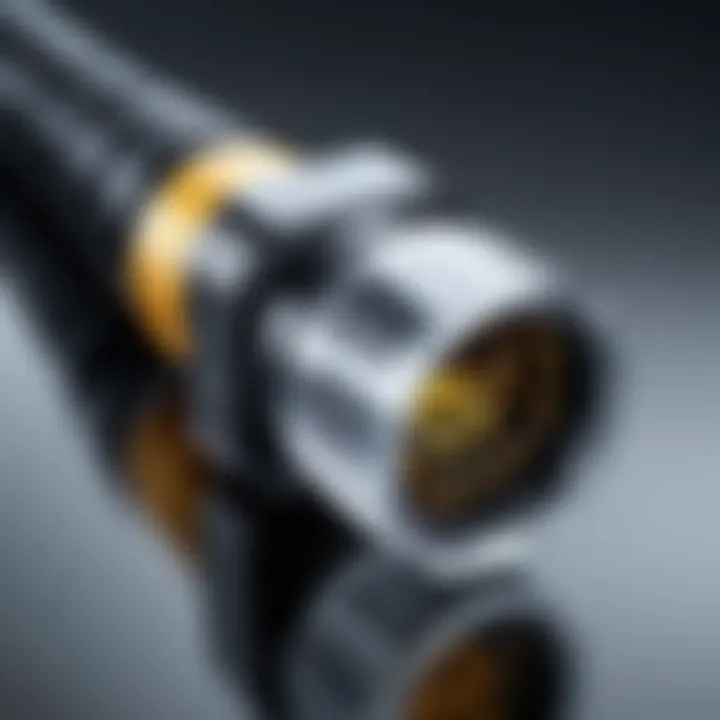
- Read Reviews: Check user experiences and performance reviews.
- Verify Ratings: Ensure the product has an authentic IP68 rating.
- Assess Warranties: Look for products that provide good warranty terms.
Warranty and Support Information
Selecting products from well-regarded manufacturers often provides added peace of mind through robust support and warranty programs. User manuals and customer service channels can aid greatly in installation and troubleshooting.
Understanding IP68 Ratings
Understanding IP68 ratings is crucial in the context of electrical cable connectors. This rating signifies the connectors' ability to withstand dust and water exposure under specific conditions. For industries that rely on electronic connections in harsh environments, such as telecommunications, marine, and construction, knowing the nuances of IP68 can influence equipment longevity and performance.
Definition of IP Ratings
International Protection (IP) ratings are a standard way to gauge how well electrical enclosures are protected against the intrusion of solid objects and liquids. Each rating consists of two digits; the first digit denotes the level of dust protection, while the second addresses water exposure. The IP68 rating indicates that the connector is completely dust-tight and can handle continuous immersion in water at specified depths. This definition serves as a foundation for evaluating connector efficacy in demanding conditions.
Breaking Down the IP68 Standard
Level of dust protection
The first digit in the IP68 rating indicates a high level of dust protection. A rating of 6 signifies that the connector is entirely dust-tight, meaning no particles can enter, thus ensuring reliable performance. This feature is especially relevant for electronics used in environments like construction sites or manufacturing facilities where dust could cause short circuits or mechanical failures.
The robust nature of IP68 connectors makes them a popular choice. With the unique benefit of being completely sealed against dust, they significantly reduce maintenance needs and increase equipment uptime. The advantage of wearing such connectors is the extended service life and overall reliability in harsh settings.
Level of water immersion
The second digit, 8, indicates a high level of water immersion protection, allowing for continuous submersion in water at depths beyond one meter. This means IP68 connectors can operate effectively even when fully submerged, making them ideal for applications in marine environments or outdoor settings where wet conditions are common.
This feature allows for versatility in design and installation where other, lower-rated connectors would fail. While IP68 connectors offer remarkable advantages, they may introduce higher costs due to their advanced manufacturing and quality materials, which can be a consideration for budget-conscious projects.
Understanding IP68 ratings is essential not only for ensuring performance but also for optimizing safety in environments where exposure to dust and water is inevitable.
Construction of IP68 Waterproof Connectors
The construction of IP68 waterproof electrical connectors is pivotal in ensuring their performance in harsh environmental conditions. These connectors must provide superior protection against dust and water while maintaining electrical integrity. Understanding the construction details gives insight into their reliability and utility across diverse industries. The selection of materials and manufacturing processes heavily influences the connectors' overall efficacy.
Materials Used
Metallic components
Metallic components are critical for IP68 connectors. Typically, these components are crafted from high-grade materials like stainless steel or aluminum. The choice of metal enhances durability and resistance to corrosion, which is essential in environments with moisture or salt air. Stainless steel, for instance, offers impressive strength while being resistant to oxidation.
The unique feature of metallic components is their conductive properties, ensuring effective electrical flow while promoting stable connections. This characteristic makes them a popular choice among industries requiring reliable electrical performance. However, the downside is that metallic parts can be susceptible to galvanic corrosion if not isolated properly, especially when in contact with different metals in the presence of an electrolyte.
Insulating materials
Insulating materials serve an essential function in IP68 connectors, primarily preventing electrical short circuits. Commonly used materials include thermoplastic elastomers (TPE) and polyvinyl chloride (PVC). These materials are selected for their robust insulating properties, enabling them to withstand water ingress while providing flexibility and durability.
A key aspect of insulating materials is their exceptional resistance to various environmental factors. For instance, TPE is beneficial because it can remain flexible even in extreme temperatures. However, some insulating materials might not provide the same resilience over time, leading to potential degradation in performance. It's crucial to balance the type of insulating material used with the specific environmental conditions the connector will face.
Manufacturing Processes
Injection molding
Injection molding is a widely used manufacturing process for producing plastic parts in IP68 connectors. This technique allows for the creation of complex shapes with high precision, making it advantageous for producing durable housings that enhance protection from environmental factors. One of the main reasons for its popularity is the efficiency with which it can scale production, ensuring consistency in quality.
The unique feature of injection molding lies in its ability to incorporate various materials and components into a single piece, minimizing assembly requirements. However, one disadvantage can be the initial costs of mold creation, which may be significant but pays off in high-volume production scenarios.
Die-casting
Die-casting is another prevalent manufacturing method, often utilized for the metallic components of IP68 connectors. In this process, molten metal is injected into a mold, creating intricate and robust parts. This approach ensures a high degree of accuracy and surface finish, making it suitable for components requiring tight tolerances.
A defining feature of die-casting is its ability to produce parts that are both strong and lightweight, essential for connectors exposed to various environmental scenarios. However, like injection molding, die-casting can be expensive in terms of initial tooling costs but generally results in a cost-effective solution for mass production.
Importance of IP68 Connectors in Various Industries
IP68 waterproof electrical cable connectors play a critical role across different sectors. Their efficiency is rooted in the ability to withstand specific environmental challenges. This section delves into their importance within telecommunications, marine and offshore installations, as well as construction and outdoor equipment.
Telecommunications Applications
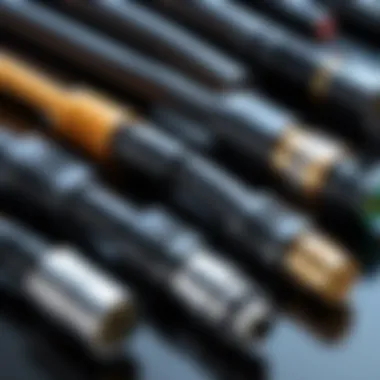
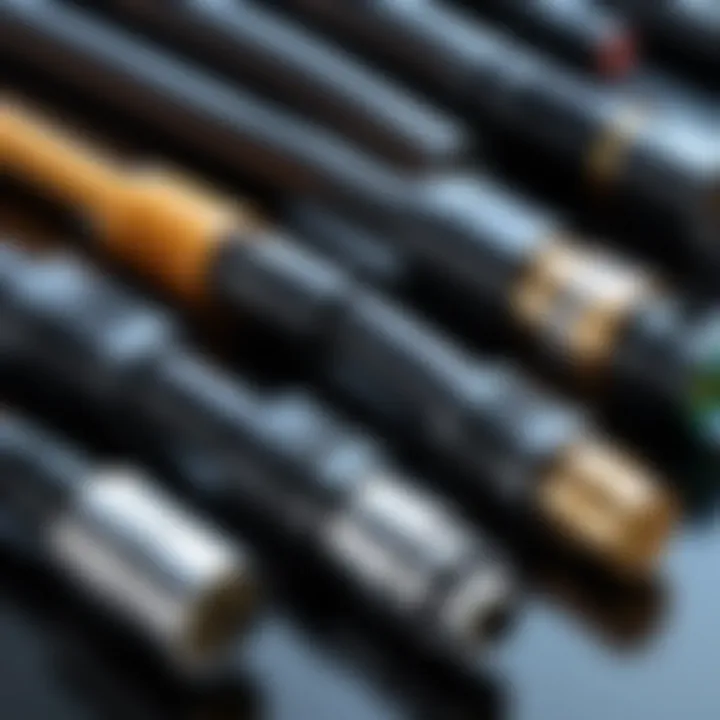
In the telecommunications industry, the reliability of connections is paramount. IP68 connectors ensure that sensitive equipment remains undamaged under adverse conditions. This is vital for maintaining service continuity.
Modern telecommunications infrastructure requires connectors that can endure rigorous conditions, including exposure to moisture and dust. The IP68 rating guarantees that these connectors are sealed against dust infiltration and can withstand submersion in water.
"Using IP68 connectors minimizes the risk of malfunction, ensuring uninterrupted data transmission and communication."
These connectors are also instrumental in outdoor installations, where environmental factors pose a significant risk. Whether used in cell towers or critical networking equipment, IP68 connectors help maintain optimal performance while reducing the likelihood of breakdowns.
Marine and Offshore Installations
Marine environments present unique challenges. Components must resist corrosion from saltwater and excessive moisture. IP68 connectors meet these demands effectively, ensuring safety and functionality for marine equipment.
In offshore platforms, connectors play a crucial role in various applications, including power distribution and data communication. The establishment of reliable and durable connections is essential. IP68 connectors provide the robust protection necessary against harsh elements.
Moreover, the importance extends to safety. Failures in connectors can lead to operational downtime and safety hazards. Thus, investing in quality connectors mitigates risks and enhances operational efficiency in these sectors.
Construction and Outdoor Equipment
In construction, the use of equipment is often in challenging conditions. IP68 connectors are vital for ensuring that machinery and tools maintain functionality despite dust, dirt, and water exposure. Construction sites can be unpredictable, where exposure to elements is the norm rather than the exception.
For outdoor equipment such as generators and site offices, high-performance connectors can significantly enhance longevity. These connectors not only protect against water ingress but also ensure that electronic systems can operate without disruption.
Attention must also be paid to installation practices to maximize the benefits of IP68 connectors. Properly fitted connectors can withstand the rigors of field use, ensuring that construction projects run smoothly.
In summary, IP68 connectors are instrumental in various industries for their protective capabilities. They safeguard against environmental threats, ensuring that critical systems operate effectively. This not only improves operational integrity but also promotes a safer working environment across telecommunications, marine, and construction sectors.
Installation Guidelines for IP68 Connectors
Setting reliable and waterproof connections is crucial for many applications. This section focuses on the importance of proper installation guidelines for IP68 connectors. Following best practices ensures maximum efficacy and longevity of these components. The guidelines provided here help avoid issues that may arise due to improper handling or assembly of connectors.
Preparation of Cables
Preparing cables for IP68 connectors is a fundamental step in the installation process. Proper preparation enhances the integrity of the waterproof seal. First, it is essential to ascertain the right cable type based on the specific application. Cables should be cut to the correct length, ensuring that excessive length is not an issue. The insulation must be stripped back adequately but not excessively. This ensures that the connectors make firm contact with the conductors when assembled.
When dealing with outdoor and marine applications, it is advisable to apply strain relief to prevent mechanical stress on the connections. Additionally, use heat shrink tubing or other sealing methods to further protect the cable ends before connecting them. This attention to detail during preparation can dramatically increase the performance and reliability of the connection.
Proper Assembly Techniques
Assembling IP68 connectors requires careful attention to the manufacturer's specifications. It is critical to follow the guidelines for connecting procedures to ensure waterproof properties remain intact. Begin by aligning the cable within the connector properly. Misalignment can lead to gaps that allow water or dust ingress.
When inserting the conductors into the connector, ensure they are fully seated to establish a good electrical connection. Some connectors may require crimping tools for secure attachment. Ensure the connectors are rotated according to instructions to lock them in place securely. After assembly, a testing phase should follow. This can involve checking for continuity or using specific meters to ensure electrical integrity. Performing these assembly techniques minimizes the risk of connection failures later.
Common Pitfalls to Avoid
When installing IP68 connectors, certain mistakes can compromise functionality. One major pitfall is neglecting the condition of the cables prior to installation. Damaged insulation or exposed conductors can easily lead to failures. Always inspect cables for any sign of wear or damage.
Another common error is over-tightening or under-tightening connections. Each connector has a specified torque rating, and not adhering to this can lead to connector failure. Use torque wrenches where applicable.
Furthermore, neglecting to follow environmental conditions during installation is detrimental. For example, assembling connectors in wet conditions can introduce moisture, rendering the seals ineffective. Always choose a dry environment and consider temperature factors, as extreme temperatures can affect material properties.
Proper installations save time and costs down the line. Adequate preparation and assembly greatly enhance the longevity of IP68 connectors.
Maintenance and Inspection of Connectors
The performance and lifespan of IP68 waterproof electrical cable connectors hinge significantly on routine maintenance and thorough inspections. Given their role in protecting sensitive electrical circuits from moisture and dust, neglecting these practices can result in decreased functionality and eventual failure. Regular attention to these connectors not only ensures their reliable operation but also prevents costly repairs or replacements in the long run. This section will delve into the importance of maintenance and inspection protocols, detailed cleaning procedures, and recognition of potential signs of wear and failure that can compromise the effectiveness of these critical components.
Regular Inspection Protocols
Regular inspection of IP68 connectors is fundamental. These inspections should be conducted as part of a systematic maintenance schedule. Importantly, the frequency of inspections can depend on the connector's application environment. For example, connectors used in high-stress conditions or extreme environments may require more frequent checks than those in controlled settings.
When inspecting IP68 connectors, technicians should focus on several key aspects:
- Visual Integrity: Check for visible signs of wear, damage, or corrosion on both the connectors and the cables.
- Sealing Integrity: Ensuring that seals are intact is vital for maintaining the IP68 rating.
- Electrical Connectivity: Measuring resistance or connectivity across the connectors can help identify potential failures.
Establishing a clear checklist can help guide the inspection process, ensuring all critical components are thoroughly reviewed.
Cleaning Procedures
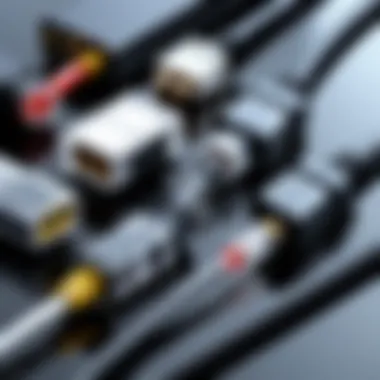
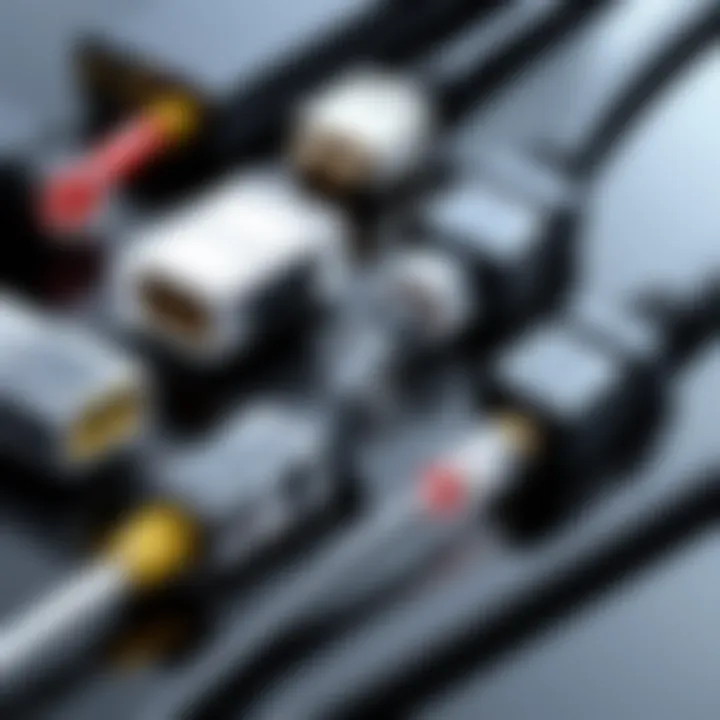
Cleaning IP68 connectors is as crucial as regular inspections. Over time, debris, dust, or residues can obstruct the connector’s functionality. Proper cleaning prevents such contaminants from compromising the sealing features of the connectors.
Here are recommended steps for effective cleaning:
- Disconnect Power: Ensure that all power is disconnected before beginning the cleaning process.
- Use Appropriate Cleaners: Use solvents or cleaning agents that do not degrade the materials of the connectors. A mild detergent mixed with water can suffice for general cleaning.
- Gentle Scrubbing: Employ a soft brush to remove any stubborn dirt or buildup without causing scratches or damage to the surface.
- Thorough Rinsing: Rinse all surfaces with clean water to eliminate any residue from cleaning agents.
- Dry Completely: Ensure that connectors are thoroughly dry before reconnecting power to prevent moisture-related issues.
Signs of Wear and Failure
Recognizing early signs of wear and failure can prevent significant disruptions in function. Operators should be attuned to specific indicators that suggest a connector may need immediate attention:
- Discoloration: This may indicate heat damage or chemical exposure, warranting further investigation.
- Cracks or Fractures: Visible cracks can severely compromise the waterproof function of the connectore; such connectors should be replaced immediately.
- Increased Resistance: Abnormal resistance levels can point to internal failures, necessitating further scrutiny.
- Intermittent Connection: The fluctuating connection may suggest internal corrosion or damage.
Regular inspections and proper maintenance practices are essential to maximizing the efficacy of IP68 waterproof cable connectors.
Implementing a robust inspection and maintenance plan is imperative in ensuring the continued performance and durability of IP68 connectors in critical applications.
Challenges in Using IP68 Connectors
While IP68 waterproof connectors are well-known for their reliability and performance, they do come with certain challenges that must be addressed by engineers and users alike. Understanding these challenges is crucial for anyone involved in selecting, installing, and maintaining these connectors in various applications. The sections below explore two significant challenges—cost considerations and compatibility issues with existing systems.
Cost Considerations
One of the primary challenges associated with IP68 connectors is their cost. These connectors are often more expensive than standard connectors due to their specialized construction and materials. High-grade materials such as stainless steel and certain durable plastics are necessary to achieve the IP68 rating. These materials ensure that the connectors can withstand not only immersion in water but also protect against dust and other particulates.
The manufacturing processes involved, such as die-casting and precision molding, also contribute to the higher costs. Setting up the equipment required for producing IP68 connectors involves significant investment.
Despite these costs, the long-term benefits can outweigh the initial investment. Using IP68 connectors reduces the risk of failures, maintenance costs, and replacement expenses in environments where moisture and dust are present.
When evaluating the cost, it’s essential to consider the total cost of ownership. This encompasses both the direct costs of purchasing the connectors and the indirect costs related to failures and downtimes caused by poor-quality connectors. Choosing a well-manufactured IP68 connector can prevent more expensive problems in the future.
Compatibility Issues with Existing Systems
Another notable challenge is ensuring compatibility with existing systems. Many industries have legacy systems that may not have been designed to incorporate IP68 connectors. This can require additional modifications which can increase the installation time and complexity.
Changes in connector types may demand redesign of cable assemblies or even complete overhauls of systems. This not only creates a financial burden but may also lead to downtime for equipment and installations. Manufacturers and engineers must also consider environmental factors such as temperature and chemical exposure when integrating new connectors into established systems. Mismatching specifications can lead risks, diminishing the benefits that IP68 connectors are meant to provide.
For users, understanding the specifications of older systems and how new connectors fit into that framework is critical. It may be necessary to consult with engineers or technical experts to ensure seamless integration.
Future Trends in Waterproof Connector Technology
In the context of waterproof connectors, particularly IP68-rated models, future trends are pivotal. These trends not only reflect the advancements in technology but also the growing expectations for performance in diverse environments. Understanding these trends can help stakeholders adapt to new developments that might redefine standards and practices.
Emerging Materials and Innovations
Innovation in materials is one of the most significant aspects of future trends in waterproof connectors. The industry is increasingly focusing on novel materials that enhance durability without compromising flexibility. For instance, the use of thermoplastic elastomers (TPE) has gained traction. TPE offers excellent resistance against environmental factors such as UV rays and extreme temperatures.
Furthermore, advancements in nanotechnology are paving the way for coatings that significantly improve corrosion resistance. These coatings can withstand harsh substances while maintaining the integrity of the connectors. This evolution promotes longer service life and reduces maintenance costs for users, making such connectors more appealing in competitive markets.
Another important area is the integration of smart technology within connectors. Smart connectors equipped with sensors can provide real-time data regarding their operational status. For example, they can notify users about moisture levels, which directly impacts performance. Such innovation can preemptively address issues before they escalate, enhancing overall reliability.
Increased Adoption in Consumer Electronics
The consumer electronics sector is experiencing a marked shift towards IP68 waterproof connectors. As devices become more compact and multifaceted, the need for reliable waterproof connectivity is paramount. From smartphones to wearable technology, ensuring that electronics can endure exposure to water and dust is increasingly important for manufacturers.
Companies are recognizing the value that IP68-rated connectors bring to their products. This not only enhances the durability of devices but also elevates the consumer experience by reducing risks related to environmental exposure. For instance, devices like smartwatches and fitness trackers often face conditions where moisture could pose a problem. The IP68 standard ensures that these devices can function effectively without the fear of damage.
Consumer demand is driving manufacturers to adopt these connectors as a standard rather than an option. Recognizing this trend can propel companies to innovate further and cater to market demands, keeping them ahead of competitors who may not prioritize this protection standard.
End on IP68 Waterproof Connectors
In this discussion about IP68 waterproof connectors, we arrive at a significant understanding of their role in modern applications. The world is increasingly dependent on robust electrical systems that perform reliably under adverse environmental conditions. IP68 connectors emerge as critical components where durability and safety are paramount. These connectors withstand harsh elements such as dust and water, ensuring continuous operation in various industries.
The importance of IP68 connectors cannot be understated. They provide peace of mind, knowing that electrical connections remain secure and unaffected by external hazards. The construction materials, manufacturing process, and inherent ratings combined serve to highlight their efficacy. In telecommunication, marine, and outdoor equipment, the reliability of these connectors safeguards both infrastructure and public safety.
Furthermore, the maintenance and installation guidelines outlined earlier demonstrate that proper care can extend the lifespan of these connectors. Investing in quality IP68 connectors is not merely an option; it is a necessity for applications requiring high reliability.
Summary of Key Takeaways
- The IP68 rating signifies a high level of protection against dust and water immersion, making these connectors suitable for extreme environments.
- Various industries benefit from IP68 waterproof connectors, particularly telecommunications, marine, and outdoor construction sectors.
- Effective installation and regular maintenance are crucial to ensure the longevity of these connectors.
- Emerging trends suggest a move towards more innovative materials and design improvements, further solidifying the place of IP68 connectors in modern technology.
In summary, IP68 waterproof connectors play a pivotal role in enhancing the reliability and safety of electrical systems across diverse fields. Their unique characteristics make them indispensable in today’s connected world.
The evolution of this technology will continue to address the challenges faced by today’s industry professionals. Their indispensable functionality ensures a stable future where IP68 connectors remain a standard choice for ensuring safety and performance.