Understanding Festo Solenoid Valves: A Comprehensive Guide
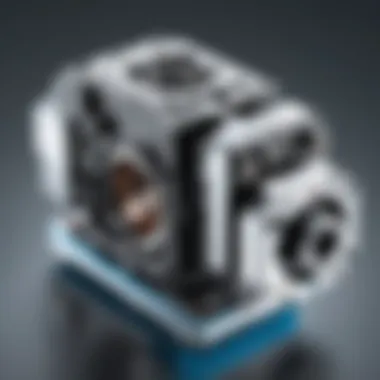
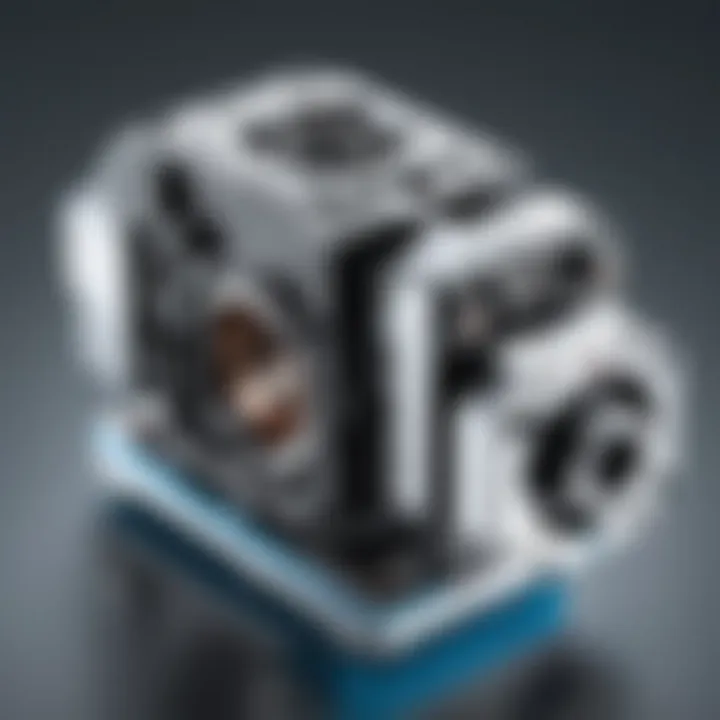
Intro
Festo solenoid valves play a crucial role in automation technology. Understanding their complex design and functionality is essential for anyone involved in industrial automation or related fields. This section will provide an overview of what these valves are and why they matter.
Typically, solenoid valves are electromechanical devices used to control the flow of fluids. Festo, a renowned provider in automation, offers a range of solenoid valves with unique features tailored for various applications. These valves are fundamental in systems requiring precise control, such as pneumatic circuits or hydraulic applications.
By exploring Festo solenoid valves, one can gain insights into their specifications, performance metrics, and practical applications. Such knowledge aids engineers, technicians, and even hobbyists in selecting appropriate components for their needs. Understanding these elements is the key to optimizing performance in automation systems.
Now, let’s delve into the technical specifications of Festo solenoid valves, which illuminate their capabilities and applications.
Technical Specifications
Detailed Product Specs
Festo solenoid valves are designed with various specifications that highlight their suitability for specific applications. Key aspects include:
- Operating Pressure: Ranges from 0.5 to 10 bar, accommodating different operational environments.
- Fluid Type: Suitable for air, vacuum, and neutral gases. Some models can handle liquids, expanding their versatility.
- Mounting Type: Options include base-mounted, panel-mounted, and inline configurations, allowing installation flexibility.
Performance Metrics
Understanding the performance metrics of Festo solenoid valves is vital.
- Response Time: Typically, response times vary around 20 milliseconds, ensuring quick actuation.
- Flow Rate: Flow rates vary between models, often in the range of 100 to 500 liters per minute. This affects their efficiency in various systems.
- Durability: Many solenoid valves are rated for extensive cycles, often exceeding 10 million operations under normal conditions.
Compatibility Information
Festo solenoid valves are designed to integrate seamlessly with other components.
- Control Systems: They are compatible with a range of control systems including PLCs (Programmable Logic Controllers) and remote control interfaces.
- Power Supply: Operating voltages typically include 24V DC and 230V AC, allowing for diverse applications.
- Pneumatic and Hydraulic Interfaces: Standard connection sizes also contribute to easy integration within existing systems.
Festo solenoid valves offer a unique blend of functionality and versatility, making them a preferred choice in numerous applications.
Next, we will navigate through product comparisons, assessing how Festo solenoid valves stack against their competitors in terms of features and user satisfaction.
Preamble to Festo Solenoid Valves
Understanding Festo solenoid valves is crucial for professionals in automation and control systems. The significance of these components lies in their ability to manage the flow of fluids with precision and efficiency. Festo solenoid valves are widely used in various applications, from industrial automation to process control. Their functionality directly impacts the performance of larger systems, making it essential to grasp their mechanisms and capabilities.
Definition and Purpose
Festo solenoid valves are electromechanical devices that regulate the flow of liquids or gases within a system. At their core, they operate based on electromagnetic principles to open or close pathways for fluids. This allows for both controlling and directing the flow according to the demands of the specific application.
The purpose of these valves extends beyond mere on/off functions. They play a vital role in achieving automation, improving system responsiveness, and ensuring safety in operations. Whether utilized in pneumatic systems or integrated within sophisticated control circuits, the efficiency of a Festo solenoid valve can significantly enhance overall system performance.
Historical Background
The development of solenoid valves coincided with advances in electrical engineering and automation. Evolving from simple mechanical switches, these valves emerged in the mid-20th century as industries sought greater precision and reliability in control systems. Festo, a key player in this field, has consistently contributed innovative designs and functionalities to enhance the use of solenoid valves.
Over the decades, Festo has refined its solenoid valve technology, integrating features that address both the increasing complexity of applications and the demand for energy efficiency. As automation technology expanded, so too did the necessity for reliable and precise solenoid valves, solidifying Festo's role as a leading manufacturer in this domain.
Components of Festo Solenoid Valves
Understanding the components of Festo solenoid valves is crucial as these parts work together to ensure optimal operation. Each element plays a specific role in the valve's functionality, impacting reliability and efficiency. Analyzing these components provides insight into the valve’s overall performance. Below, we will explore the individual parts that make up these essential devices.
Solenoid Coil
The solenoid coil serves as the core element of a Festo solenoid valve. When electrical current passes through the coil, it generates a magnetic field. This magnetic field is what actuates the valve, leading to its opening or closing. The efficiency of the solenoid coil is vital for performance. A properly functioning coil ensures fast response times, which is imperative in many automation applications.
Several factors influence the efficiency of the solenoid coil. The wire gauge used in the coil, the number of turns, and the material of the core contribute significantly to performance. A coil constructed with high-quality materials can achieve better heat dissipation and reliable operation over long periods. Specific models may offer various voltage ratings, allowing users to select coils that best match their systems.
Valve Body
The valve body houses the internal components of the solenoid valve, providing structure and durability. Generally made from robust materials like brass or stainless steel, the body is designed to withstand varying pressure levels and environmental conditions. Its design affects flow characteristics, as well as ease of installation.
Festo offers multiple designs for valve bodies, including inline and manifold styles. Inline valves are simpler to integrate into existing piping systems, while manifold valves allow for compact assembly of multiple valves. It's important to choose a valve body that not only fits seamlessly with the existing setup but also meets the required pressure ratings.
Seal and Diaphragm
The seal and diaphragm are critical components that aid in preventing leaks and ensuring that the valve functions as intended. The diaphragm, often made from elastomeric materials, helps separate the different pressures within the valve. It moves in response to the magnetic force generated by the solenoid coil, ultimately enabling the valve’s operation.
Selecting the right materials for seals and diaphragms is crucial. They must be compatible with the media being controlled, as well as capable of withstanding temperature and pressure variations. Regular inspection of these components is necessary, as wear and tear can lead to functional failures. Proper maintenance can prolong their life and enhance the overall reliability of the solenoid valve.
Key Points:
- The solenoid coil generates the magnetic field that actuates the valve.
- The valve body is essential for structural integrity and performance.
- Seals and diaphragms prevent leaks and ensure functionality.
In summary, an understanding of the components in Festo solenoid valves is fundamental for effective usage and maintenance. Each part plays a specific role that directly impacts overall valve performance.
How Festo Solenoid Valves Operate
Understanding how Festo solenoid valves operate is crucial for grasping their role in automation. These valves are central to controlling the flow of fluids in various systems. Their operation relies heavily on electromagnetic principles, which ensures precise and efficient performance. The benefits of mastering the mechanics of these valves extends to enhanced system reliability and better integration into existing frameworks.
Electromagnetic Actuation
Electromagnetic actuation is the primary mechanism behind Festo solenoid valves. This process involves the use of a solenoid, which is essentially a coil of wire that generates a magnetic field when electrical current passes through it. This field actively drives the movement of a plunger or armature, which in turn opens or closes the valve.
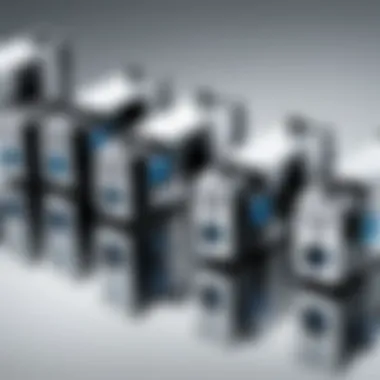
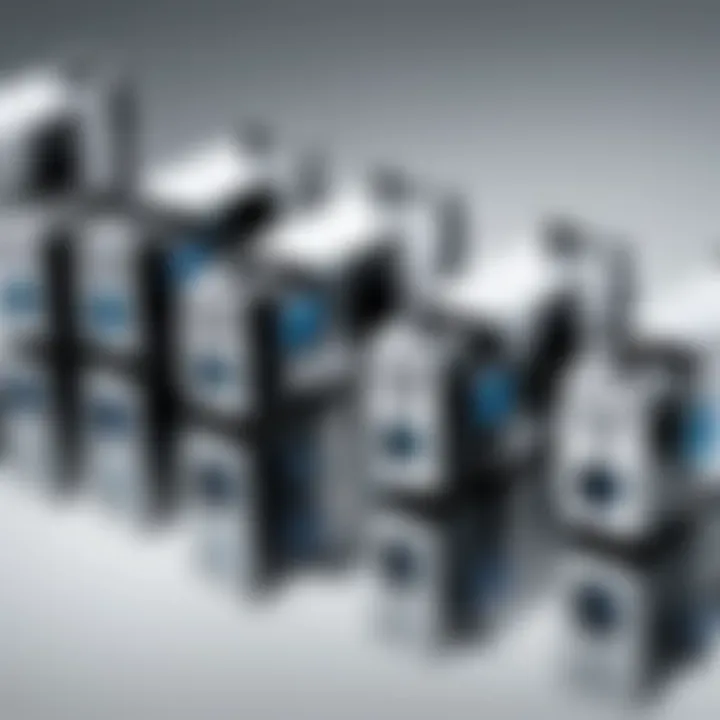
- How it Works: When the solenoid is energized, the magnetic field attracts the plunger. This movement pushes against a spring mechanism, either opening or closing the valve based on its configuration. The entire process is quick, allowing for rapid response in controlling fluid flow.
- Importance: This method of actuation is vital for ensuring precise control in automated systems. The ability to switch states in milliseconds makes these valves ideal for applications requiring real-time decision-making.
"The speed and reliability of electromagnetic actuation make Festo solenoid valves a preferred choice for many professionals in industrial automation."
Flow Control Mechanism
The flow control mechanism is another essential aspect of how Festo solenoid valves function. Through this mechanism, the valves manage how much fluid flows through the system and regulate pressure levels. Effective flow control is critical in ensuring that processes operate within designated parameters.
- Types of Control: The flow control can be either on/off or proportional. On/off valves quickly shut or allow the passage of fluid, whereas proportional valves adjust flow rates, providing more granularity in control.
- Valves Configurations: Depending on the application, valves can be designed in two-way configurations to control flow in one direction or three-way configurations to switch between multiple flow paths. This versatility enhances overall system flexibility.
Integrating an efficient flow control mechanism reduces energy waste, enhances safety, and extends the lifespan of equipment. Understanding these principles will help professionals select and maintain Festo solenoid valves effectively, maximizing their utilities in complex systems.
Types of Festo Solenoid Valves
Understanding the various types of Festo solenoid valves is crucial for optimizing their application in automated systems. These valves are designed to control the flow of fluids effectively, and selecting the appropriate type can significantly enhance the overall performance of a system. Factors such as process requirements, space constraints, and operational philosophies must all be considered when making a choice. The following are the main types of Festo solenoid valves that practitioners should familiarize themselves with:
Normally Closed Valves
Normally Closed solenoid valves function under the principle that the valve is in a closed position until energized. This means that when there is no electric current supplied to the solenoid, the mechanism remains closed, preventing fluid flow. They are essential in applications where stopping the flow of fluid is critical when the control signal is not active.
Key Benefits:
- Safety: Keeps fluid securely contained when power is off, crucial in processes where leakage poses risks.
- Control: Provides a straightforward means of controlling the flow based on a simple electrical signal.
- Flexibility: Suitable for various mediums, including air, water, and other fluids.
These valves are often utilized in applications such as pneumatic control systems, where a sudden loss of fluid could lead to system failure.
Normally Open Valves
On the contrary, Normally Open solenoid valves allow fluid to pass through when no power is supplied. When electrically actuated, these valves close off the flow. They are often selected for applications where continuous fluid flow is needed until an external signal interrupts it.
Key Benefits:
- Efficiency: Saves energy as they consume power only during operation.
- Immediate Response: Quick closure upon receiving a signal, which adds to operational safety in certain scenarios.
- Simplicity: Easy to incorporate into existing systems without extensive modifications.
These valves find applications in systems like cooling and heating, where the need for continuous flow is paramount.
Two-Way and Three-Way Valves
Two-Way solenoid valves facilitate fluid flow in one direction. They can be normally open or normally closed, but their primary function is to allow or block the flow. In contrast, Three-Way solenoid valves, as the name suggests, have three ports and can be configured to direct flow between two outputs. This added functionality allows greater control in systems requiring fluid redistribution.
Key Benefits:
- Versatility: Three-Way valves can be used for switching operations, enhancing the flexibility of fluid systems.
- Simplified Design: Combining control functionalities in fewer components leads to a more streamlined system architecture.
- Space-Efficiency: Reduced components can result in a more compact setup, which is advantageous in constrained spaces.
Both Two-Way and Three-Way valves are integral to applications in manufacturing, automotive systems, and even HVAC setups.
In summary, choosing the right type of solenoid valve is pivotal for the operational efficiency of any automation system. The specific attributes and functionalities of Normally Closed, Normally Open, Two-Way, and Three-Way valves should drive the selection process to meet project requirements effectively.
Applications of Festo Solenoid Valves
The applications of Festo solenoid valves play a crucial role in understanding their value in automation. These valves are not just components; they function as integral parts that drive efficiency and effectiveness in various sectors. Industries rely on these devices to streamline processes, control fluid dynamics, and ensure seamless operation across numerous systems.
Industrial Automation
Festo solenoid valves are essential in industrial automation applications. They help control the movement of pneumatic cylinders and actuators. These devices allow for precise control of machinery, contributing to overall productivity. The timing and flow accuracy provided by solenoid valves enable synchronous operations. A delayed or mismanaged flow can cause significant bottlenecks, leading to inefficiencies.
In high-speed production environments, solenoid valves ensure rapid response times. Their ability to rapidly switch the flow on and off increases operational speeds. This capability is vital in assembly lines where timely and coordinated movements directly affect output.
Pneumatic Systems
Pneumatic systems heavily rely on Festo solenoid valves, as they are crucial for controlling air flow within various applications. Solenoid valves manage the flow of compressed air that powers tools and equipment. The precise control these valves offer leads to better performance and safety. This is especially true in systems where pressure levels need tight regulation to prevent failures.
In addition to control, solenoid valves in pneumatic systems help maintain energy efficiency. By quickly adjusting the flow, they minimize energy waste, leading to lower operating costs. Moreover, their compact nature allows for easy integration into existing setups, maximizing space utilization. This adaptability makes them valuable in both new installations and retrofitting projects.
Process Control Systems
In process control systems, Festo solenoid valves play a pivotal role in maintaining various parameters such as pressure, flow rate, and temperature. These systems require precise control to ensure high-quality production in industries like food and beverage, pharmaceuticals, and chemicals. The valves provide real-time adjustments, enabling quick responses to any changes in the system.
Furthermore, the modular nature of Festo solenoid valves allows for easy expansion and customization of control systems. Businesses can incorporate advanced functionalities as their needs evolve, without requiring complete overhauls of their equipment. This flexibility enhances operational longevity and supports innovation in production techniques.
Festo solenoid valves not only improve efficiency but also enhance safety and operational flexibility.
In summary, the applications of Festo solenoid valves are diverse and impactful. From industrial automation to pneumatic systems and process control, these valves provide numerous benefits. Their capacity for precise control, energy efficiency, and adaptability makes them indispensable in many sectors.
Advantages of Using Festo Solenoid Valves
The use of Festo solenoid valves brings various significant advantages to the table. Understanding these benfits is crucial for professionals and enthusiasts alike, as it aids in the selection process and enhances system performance. Festo solenoid valves stand out in the realm of automated systems for their efficiency, adaptability, and engineering quality.
Reliability and Performance
Festo solenoid valves are designed for reliability under varying operational conditions. They perform consistently, reducing the odds of failure during critical operations. The precision engineering inherent in their design means these valves can endure high pressure and temperature fluctuations. This reliability equates to less downtime, which is essential in environments where productivity is key.
Moreover, the performance of Festo solenoid valves extends to quick response times. This ability to actuate and regulate flow almost instantaneously allows for fine-tuned control in numerous applications. Fluctuations in pressure and flow can be managed adeptly, promoting efficiency in entire systems.
Ease of Integration
Integrating Festo solenoid valves into existing systems is generally straightforward. Their design allows for compatibility with various control systems without the need for extensive modifications. This characteristic is especially vital in industrial automation, where time and resources are often limited.
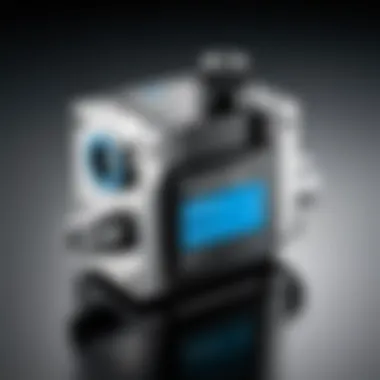
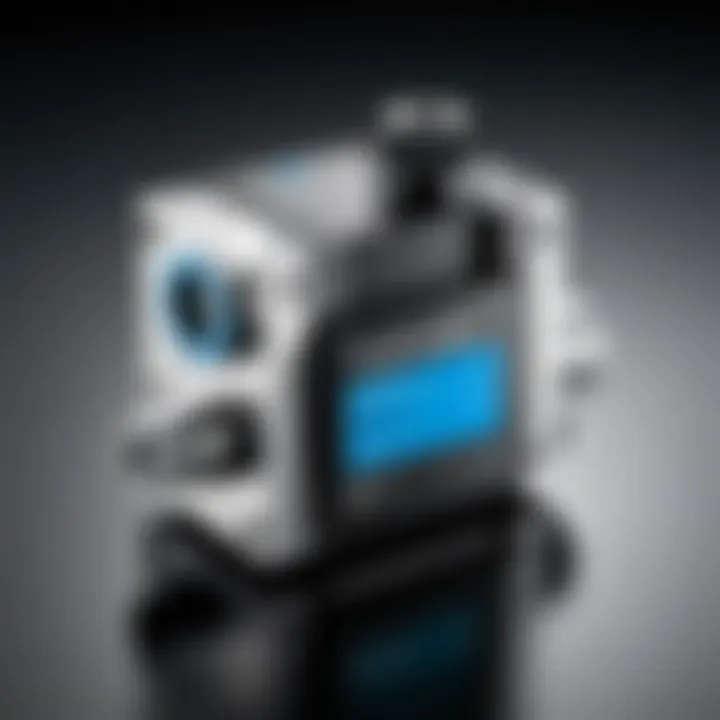
Moreover, Festo provides comprehensive documentation and support, easing the installation process. Users can easily find information on specifications and wiring, leading to smoother setups. This ease of integration also applies to a wide range of configurations and connections, ensuring that Festo solenoid valves can meet various specific project requirements.
Compact Design
Festo solenoid valves come with a compact design, which offers significant advantages in terms of space management. In today’s automation landscape, where systems are often designed to occupy minimal space, this factor cannot be overlooked.
Their reduced footprint allows easier placement within confined areas. This is particularly relevant in environments where every inch of space counts. Additionally, their compactness contributes to lighter overall system weight, which can further simplify installation and reduce the strain on supporting structures.
The combination of reliability, ease of integration, and compact design makes Festo solenoid valves a preferred choice for both new applications and upgrades of existing systems.
Challenges in Festo Solenoid Valve Usage
Festo solenoid valves are crucial in many applications, but they face certain challenges that must be understood. Addressing these challenges is essential for optimal performance and longevity of the valves. This section will explore two primary challenges: environmental sensitivity and power supply dependence.
Environmental Sensitivity
Environmental sensitivity is a significant concern when it comes to the usage of Festo solenoid valves. These valves can be affected by dust, moisture, and temperature variations.
- Dust and Debris: Dust can accumulate on the valve components, leading to improper sealing and malfunctions. This can cause a drop in performance levels and increase wear and tear.
- Moisture and Humidity: Excessive moisture can result in corrosion or even short-circuiting within the solenoid itself. As such, it is essential to install valves in protected environments or to use protective casings when working in moist conditions.
- Temperature Fluctuations: Operating outside the recommended temperature range may impair functionality. Festo valves are designed for specific temperature limits. If these limits are exceeded, the material properties can degrade.
“Understanding the environmental factors that influence solenoid valve performance is crucial for maintaining their reliability and efficiency.”
Power Supply Dependence
Power supply dependence is another challenge faced by Festo solenoid valves. These valves rely on electrical input to open and close efficiently.
- Voltage Variations: Fluctuations in power supply voltage can lead to unstable operations. This may cause the solenoid to misfire or operate sporadically, making it difficult to maintain consistent performance in automation systems.
- Current Ratings: Each solenoid valve has specific current requirements. Using a supply that does not match these ratings can cause overheating or permanent damage.
- Power Outages: In case of power loss, valves may revert to their default state. Knowing how the valve behaves in such situations is vital for applications where uninterrupted operation is critical.
Each of these challenges can be addressed through careful planning and the implementation of appropriate measures, like dust covers and voltage regulators. By acknowledging these elements early on, users can enhance the reliability and performance of their Festo solenoid valves.
Maintenance of Festo Solenoid Valves
Regular maintenance of Festo solenoid valves is crucial to ensure their functionality and reliability. These components are often critical in automation and control systems, where any failure can lead to inefficiencies or system downtimes. Proper maintenance includes consistent inspection, cleaning, and addressing any issues that may arise during operation. Understanding the importance of maintenance enables technicians and engineers to prolong the life of the equipment and maintain optimal performance.
Regular Inspection
Regular inspection is an essential aspect of maintaining Festo solenoid valves. This process involves checking the physical condition of the valve, ensuring that all components are intact and functioning as intended. During inspections, one should look for wear or damage that could affect the valve's performance.
Key elements to inspect include:
- Solenoid Coil: Check for signs of overheating or corrosion.
- Valve Body: Look for surface damage and ensure seal integrity.
- Connections: Ensure electrical connections are tight and free from corrosion.
Performing inspections at regular intervals can catch potential issues before they escalate, thus reducing machine downtime and preventing costly repairs.
Cleaning Protocols
Cleaning Festo solenoid valves is another important maintenance task. Accumulation of dirt, dust, and other contaminants can affect the valve's responsiveness and reliability. A proper cleaning protocol helps maintain the performance and longevity of the valve.
Recommended cleaning steps include:
- Power Off: Always shut off power supply to the valve before cleaning.
- Disassemble: Carefully take apart the valve components as per manufacturer guidelines.
- Gentle Cleaning: Use a soft cloth or brush to remove dirt. Avoid using abrasive materials.
- Lubrication: Apply appropriate lubricants to moving parts if recommended by the manufacturer.
Following these cleaning protocols can significantly enhance the operational efficiency of solenoid valves, ensuring they respond correctly in various applications.
Common Issues and Solutions
Over time, Festo solenoid valves may encounter a variety of issues. Identifying these problems quickly and understanding their solutions can minimize downtime and extend the valve's lifespan.
Common issues and possible solutions include:
- Valve Not Responding: Check for electrical supply issues or a faulty solenoid coil.
- Leaking Valve: Inspect seals and diaphragms for wear or damage, replace if necessary.
- Erratic Operation: Ensure that the valve is clean and free from obstructions. Additionally, confirm that pressure and voltage levels are within specified ranges.
Regular attention to these common problems can keep Festo solenoid valves operating effectively, making it easier to maintain automated processes.
Overall, by implementing a structured maintenance approach, users can ensure consistent operation and reliability of Festo solenoid valves, ultimately leading to better performance in automation systems.
Festo Solenoid Valve Specifications
Festo solenoid valve specifications are critical for the efficient operation of automated systems. A clear understanding of these specifications helps users select the correct valve for their applications. Each specification correlates with performance and reliability. Important elements include pressure ratings, voltage and current ratings, and flow coefficients.
Pressure Ratings
Pressure ratings indicate the maximum pressure at which a valve can function safely. Choosing a valve with the proper pressure rating ensures the system will operate effectively without risk of failure. Users must consider the pressure of the fluid or gas that will pass through the valve. Typical applications involve variable pressure conditions.
- Common pressure ratings for Festo solenoid valves include:
- Up to 10 bar for standard applications
- Specialized valves may handle pressures exceeding 16 bar
When selecting a valve, always check this rating against the requirements of your specific application.
Voltage and Current Ratings
Voltage and current ratings are significant in determining how the solenoid activates. These ratings specify the electric input needed for optimal function. If a valve does not receive proper voltage or current, it may not operate correctly, leading to system inefficiencies.
- Typical ratings for Festo valves can be:
- 24V DC (direct current)
- 230V AC (alternating current)
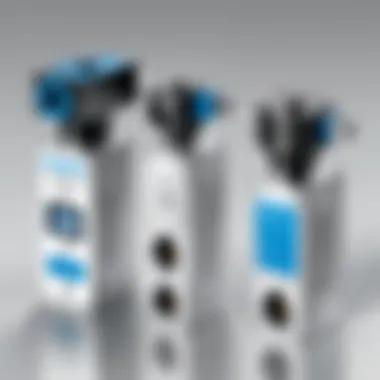
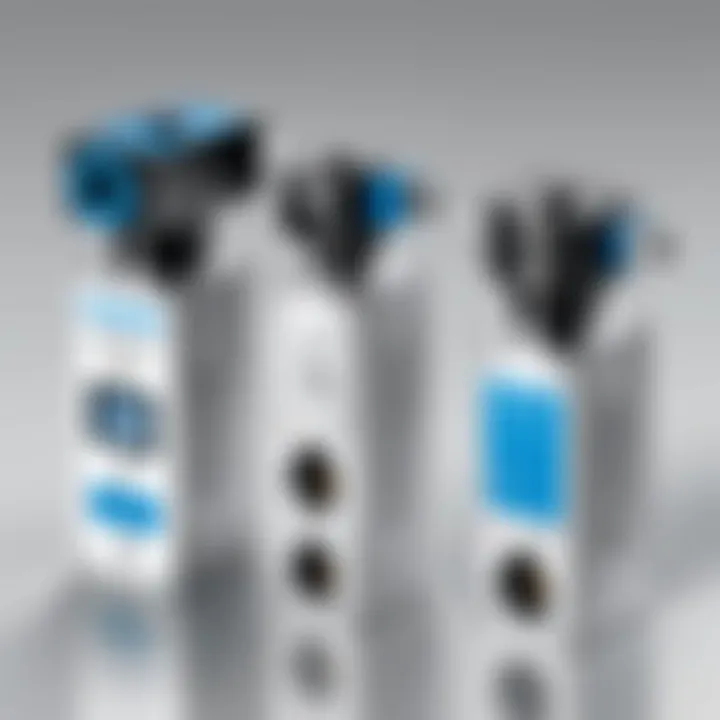
Understanding the required power input allows for seamless integration into existing systems. Always ensure that the electrical supply matches the valve specifications.
Flow Coefficients
Flow coefficients are essential in determining the flow rate through a valve. The higher the flow coefficient, the greater the flow capacity of the valve. This metric is beneficial in applications that require specific flow rates for operation.
Flow coefficients can vary based on:
- Valve size
- Design type
When reviewing flow coefficients, consider the total flow demands of the system. Matching the flow capacity to application requirements can prevent issues with underperformance or energy inefficiency.
Understanding Festo solenoid valve specifications not only enhances response times but also contributes to system reliability, safety, and efficiency.
Selecting the Right Festo Solenoid Valve
Selecting the appropriate Festo solenoid valve is critical. This decision can affect both performance and efficiency in automation applications. An improper valve can lead to system malfunctions or inefficient operations.
Matching Specifications to Application
When matching specifications, several factors must be considered. The first step involves understanding the system's requirements. Each application has unique needs, including pressure ratings, flow control, and response times.
- Pressure Ratings: Ensure the valve can handle the system’s pressure. Using a valve rated below the requirements can cause failures.
- Flow Requirements: Assess the required flow rate. A valve with inadequate flow capacity may lead to sluggish operations.
- Response Time: Evaluate how quickly the valve must open or close. Some applications need rapid responses while others can function with slower actuation.
Moreover, the type of fluid should also be assessed. For example, some valves are compatible solely with air or specific gases, while others may work effectively with liquids. Using the wrong valve can lead to leaks or reduced efficiency. Always reference the technical specifications from Festo to ensure compatibility with the intended application.
Considering Environmental Factors
Environmental conditions influence the selection of solenoid valves. Factors such as temperature, humidity, and exposure to contaminants are crucial to consider.
- Temperature Range: Valves should operate effectively within the designated temperature range. Extreme temperatures can affect materials and lead to component failure.
- Humidity Levels: In high-humidity environments, selecting valves with appropriate sealing is essential to prevent corrosion or other issues.
- Contaminant Exposure: If the valve will be exposed to dust or chemicals, ensure it is designed to withstand such conditions. Special coatings or materials may be necessary to prevent degradation.
Important Note: Not considering environmental factors could result in premature wear and system inefficiencies.
Festo Solenoid Valve vs.
Competitors
Festo solenoid valves are prominent in the automation landscape. Understanding how they compare to competitors is vital for making informed choices. Companies like SMC, Parker, and ASCO also produce solenoid valves that may attract users for various reasons. To grasp the competitive advantages and limitations of Festo solenoid valves, it is essential to dissect the features and market positioning, and how these elements align with customer needs.
Comparison of Features
When comparing Festo solenoid valves with those from competitors, several key features stand out. These include:
- Build Quality: Festo is known for its rigorous quality control and durability in harsh environments. Components are often robust and designed for long-term use.
- Performance Metrics: The efficiency of Festo valves in terms of response time and pressure handling often surpasses those of competitors. Users benefit from faster actuation, which enhances system performance.
- Versatility: Many Festo valves can operate in various applications without extensive modifications. This versatility can simplify installation and maintenance processes.
- Energy Efficiency: Festo has made strides in energy-efficient designs. Users may notice reduced utility costs when selecting their products due to lower energy consumption during operation.
Additionally, Festo offers a comprehensive range of products that cover both basic and specialized applications. This diversity in offerings can be an advantage over competitors that may only focus on niche markets.
Market Positioning
Festo has carved out a strong position in the marketplace for solenoid valves. The brand is often associated with high-quality engineering and innovation. This reputation underscores several advantages:
- Brand Recognition: Festo is widely recognized for its commitment to quality, which fosters trust. This recognition can be a deciding factor for professionals choosing between various brands.
- Support and Resources: Customers can access extensive resources, including technical support, documentation, and training materials. This level of support can be a critical differentiator for those tasked with installation and maintenance.
- Market Reach: Festo has a global presence that allows them to serve customers in varied industries. Their ability to cater to multiple segments—from automotive to food and beverage—shows their adaptability in the market.
- Innovation Leadership: Continuous investment in research and development ensures that Festo remains at the forefront of solenoid valve technology. Competitors may struggle to keep pace with their advancements.
Future Trends in Solenoid Valve Technology
The field of solenoid valve technology is evolving. The demand for efficiency and smart solutions drives these changes. Festo solenoid valves are not exempt from this trend. They incorporate modern innovations that improve functionality and user experience.
Innovations in Design
Innovation in design is crucial. Engineers and manufacturers are focusing on making solenoid valves more compact and effective. New materials are used to extend the life of these devices and ensure reliability.
A few key design innovations include:
- Miniaturization: Smaller valves save space in machinery.
- Improved Sealing Technology: Better seals reduce leakage and increase efficiency.
- Enhanced Flow Characteristics: New designs can optimize flow rates, leading to better performance in various applications.
These advancements play a vital role in ensuring solenoid valves meet the increasing demands of industry. They allow for more precise control in automated systems.
Smart Valve Technologies
Smart valve technologies are transforming how solenoid valves operate. Integration of sensors and communication systems is becoming more common. These enhancements allow for data collection and remote monitoring.
Benefits of smart solenoid valves include:
- Real-Time Monitoring: Users can track performance and detect issues before they escalate.
- Automatic Adjustments: Valves can automatically adjust based on changing conditions, improving system efficiency.
- Easy Integration: Smart valves can fit into existing systems without significant modification.
Incorporating these technologies leads to more sophisticated automated systems. Users have greater insight into operational performance and can make data-driven decisions.
The future of solenoid valves is undoubtedly intertwined with smart technology and innovative design. This combination promises to enhance efficiency and operational reliability across industries.
Epilogue
In this article, we explored Festo solenoid valves, pinpointing their critical role in automation technology. Understanding these components leads to improved efficiency and precision in various applications, such as industrial automation and pneumatic systems. The knowledge gained here helps in selecting the correct type of valve, ensuring that it aligns with the specific needs of your project or system.
Summary of Key Points
- Definition and Purpose: Festo solenoid valves are essential for controlling fluid flow in automated systems.
- Operation Mechanism: They operate through electromagnetic actuation, facilitating precise flow control.
- Types and Applications: Different types exist, including normally opened and normally closed designs, suited for various industrial applications.
- Specifications: Understanding pressure ratings, voltage, and current specifications is crucial in valve selection.
- Maintenance Needs: Regular inspection and cleaning are vital for optimal performance and longevity.
Final Thoughts on Selection and Maintenance
Choosing the right Festo solenoid valve involves more than just looking at features. It requires careful consideration of the specific application's needs and environmental factors. Ensuring compatibility with existing systems can prevent future problems. Maintenance cannot be overlooked, as it directly affects reliability and performance. Regular checks, cleaning, and addressing common issues will extend the life of your solenoid valve, ensuring it operates effectively when needed.
By understanding the intricacies of Festo solenoid valves and their specifications, users can make informed decisions that enhance operational efficiency.