Understanding Blue Heat Shrink Wrap: Uses and Benefits
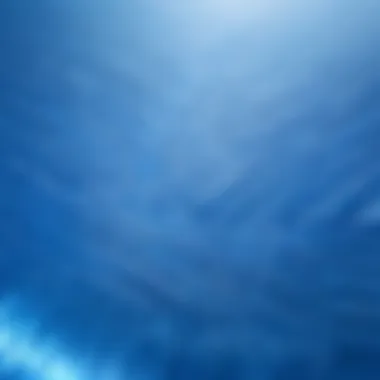
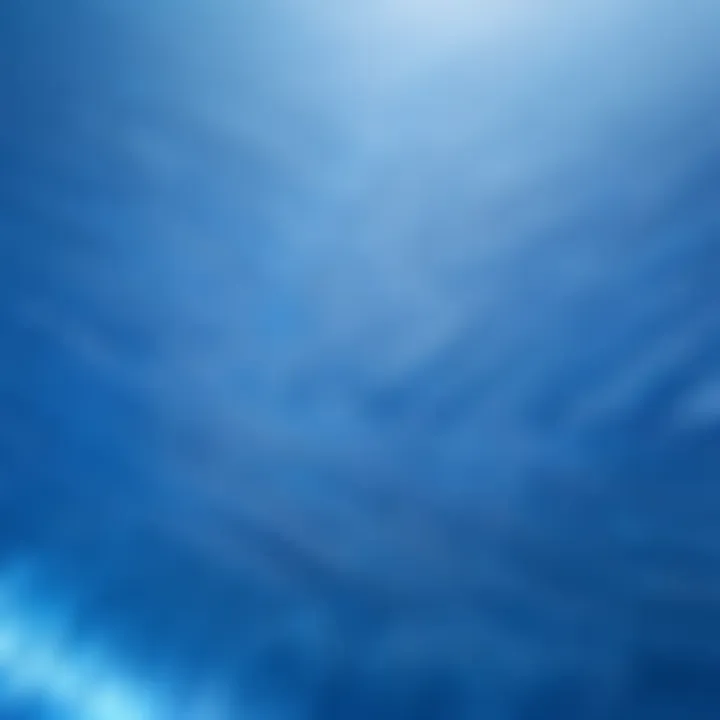
Intro
Blue heat shrink wrap, though often overlooked, plays a critical role in various applications within electronics and hardware. This material is used to insulate, protect, and bundle components, ensuring longevity and operational efficiency. Understanding its properties, applications, and benefits is essential for both professionals and enthusiasts. This article aims to shine a light on the intricacies of blue heat shrink wrap, focusing on its technical specifications, practical uses, buying guides, and current trends in the industry.
Technical Specifications
Detailed Product Specs
Blue heat shrink wrap is available in various sizes, thicknesses, and materials. Commonly made from polyolefin, it boasts excellent flexibility and resiliency. The shrink ratio typically ranges from 2:1 to 3:1, meaning that it can shrink to half or a third of its original size when heated. This characteristic is vital for ensuring a snug fit over irregular shapes or components.
Performance Metrics
Performance metrics are crucial for evaluating the effectiveness of blue heat shrink wrap. Important factors include its operating temperatures, which usually range from -55°C to +125°C. Moreover, it exhibits strong resistance to chemicals, abrasion, and moisture, making it suitable for various environments.
Compatibility Information
Compatibility with electrical components is one of the highlights of blue heat shrink wrap. It can be used effectively with wires, terminals, and a range of connectors. It is also important to select the correct size and type for specific tasks to ensure optimal performance. Always consult manufacturer specifications for recommendations on compatibility.
Practical Applications
Use Cases for Different Users
The versatility of blue heat shrink wrap makes it ideal for a variety of users. For hobbyists and DIY enthusiasts, it is often employed for securing connections in custom electrical projects. Professionals in electronics assemble also utilize it to protect soldered joints and enhance the durability of circuitry.
Recommended Configurations
Recommended configurations for using blue heat shrink wrap include selecting the right diameter based on the component size and noting the shrink ratio for effective coverage. Additionally, a heat gun is preferred for uniform shrinking; not using lighter flame is advisable, as it may cause uneven heating and damage to the material.
Multi-Platform Performances
This type of heat shrink wrap is not limited to one platform. It is used across different sectors including automotive, telecommunications, and even in various consumer electronics. This adaptability is a substantial advantage, providing a protective barrier in various contexts, ensuring performance integrity.
Latest Trends
Industry Developments
As the demand for efficient and safe electronic components continues to rise, manufacturers are innovating blue heat shrink wrap materials. Developments towards eco-friendly materials are also gaining traction, as consumers become more mindful of environmental impact.
Emerging Technologies
Emerging technologies related to heat shrink wrap include advancements in smart materials. New thermochromic and piezoresistive wraps are being tested, which could provide enhanced functionalities, such as changes in color based on temperature or stress, adding another layer of information regarding the state of the components.
Future Predictions
Looking ahead, the future of blue heat shrink wrap appears promising. The integration with smart technology is expected to become a norm, with enhanced features catering to a tech-savvy audience. These advancements should result in higher efficiency and better usability in an ever-evolving tech landscape.
Buying Guides
Recommended Products
When considering purchasing blue heat shrink wrap, several reputable brands like 3M and HellermannTyton are worth examining. They offer a range of options suitable for different applications and budgets.
Purchasing Tips
It is beneficial to buy in bulk, especially for professionals, to reduce costs. Always check the manufacturer specifications to ensure the suitability for the intended application, and consider obtaining samples if unsure.
Warranty and Support Information
Most reputable brands provide warranties for their products, ensuring confidence in quality. Support from manufacturers often includes access to technical assistance and detailed product information, which can be invaluable.
Understanding the properties and applications of blue heat shrink wrap will ensure users make informed decisions, optimizing both performance and longevity in their projects.
Intro to Blue Heat Shrink Wrap
Blue heat shrink wrap serves a significant role in various applications, especially in electronics and hardware. Its importance lies in its ability to provide protection and enhance the durability of components. This section aims to explain why understanding blue heat shrink wrap is essential for both enthusiasts and professionals.
Heat shrink wrap is a versatile material that shrinks in response to heat. Blue, specifically, is utilized not only for its aesthetic appeal but also as a functional element in specific scenarios. The color serves as a visual identifier, helping in color-coding systems, which can be particularly useful when managing wires or components in complex electronic setups.
When selecting blue heat shrink wrap, several benefits emerge:
- Environmental Protection: The material offers barriers against dust, moisture, and other environmental factors that can lead to component degradation.
- Durability: Blue heat shrink wrap is known for its robustness, ensuring that covered components remain protected in various settings.
- Identification: The blue color adds a layer of organization in settings where multiple types of heat shrink wraps are employed, enhancing visibility and traceability.
The introduction of this article sets the stage for a detailed exploration of blue heat shrink wrap. It will assess its composition, applications, benefits, and installation techniques. By the end, readers will have a comprehensive understanding, aiding them in making informed decisions regarding the use of this vital material in their projects.
Understanding the nuances of blue heat shrink wrap can lead to improved performance and longevity of electronic components.
As we proceed, we will delve deeper into the characteristics of blue heat shrink wrap, ensuring that both beginners and seasoned professionals gain valuable insights.
What is Blue Heat Shrink Wrap?
Blue heat shrink wrap is a specialized material that plays a crucial role in various fields, especially in electronics and hardware. Understanding what blue heat shrink wrap is can help users appreciate its benefits and applications more fully. It is easy to overlook the specific characteristics that enhance its functionality, but a deeper dive reveals its significance in offering protection and versatility.
Definition and Purpose
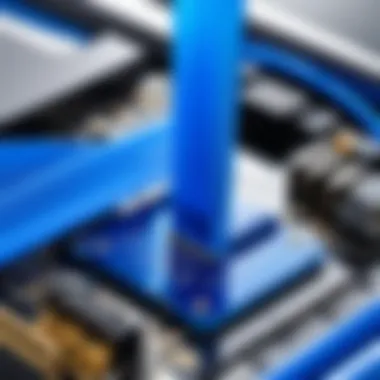
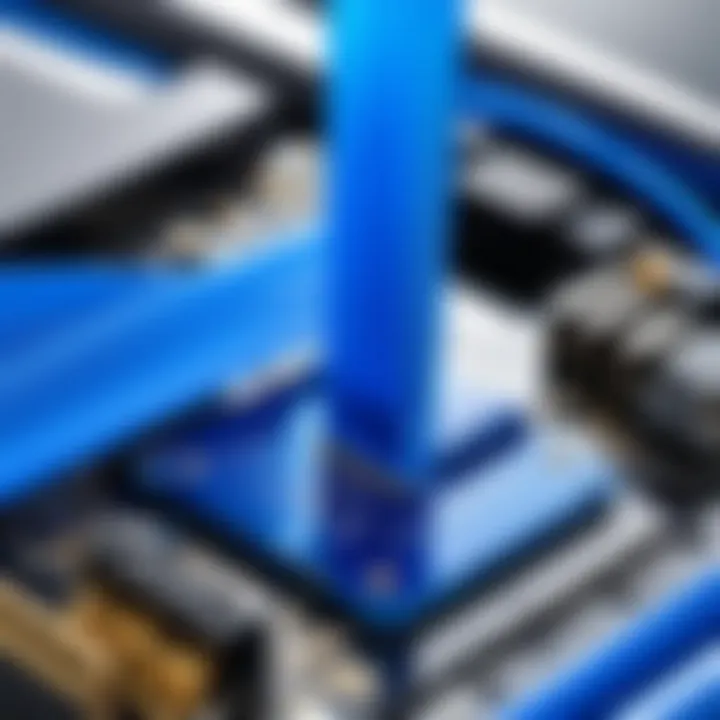
Blue heat shrink wrap is a polymer material that contracts when heat is applied. It encases components to provide insulation, protection, and strain relief. This wrap is particularly essential in electrical applications where it safeguards wiring and connections from factors such as moisture, dust, and mechanical abrasion. Its bright blue color can also aid in quick identification, especially in tangled or complex setups. The primary purpose of this material is to enhance safety and functionality by preventing short circuits and ensuring a reliable connection.
Composition of Materials
The material from which blue heat shrink wrap is made is commonly polyolefin, PVC, or rubber, each with unique properties.
- Polyolefin: This type is noted for its excellent flexibility and resistance to extreme temperatures. It shrinks uniformly and adheres well, making it a preferred choice for many electronics.
- PVC: PVC heat shrink provides good protection against environmental factors like chemicals and moisture. It’s often used in automotive applications due to its durability.
- Rubber: Rubber heat shrink offers superior elasticity, making it suitable for applications involving flexible connections, such as in robotics or intricate electronic devices.
In summary, the composition of blue heat shrink wrap directly influences its properties. This is key when selecting the right type for specific applications, ensuring optimal performance and safety.
Types of Heat Shrink Wrap
Understanding the different types of heat shrink wrap is essential for users who wish to prioritize specific applications in their projects. Each type offers distinct advantages derived from its material composition, making it more suitable for certain tasks. This section will delve into the three prominent types: Polyolefin, PVC, and Rubber heat shrink. Knowing the features and benefits of these materials can guide you in making an informed choice based on your project's requirements.
Polyolefin Heat Shrink
Polyolefin heat shrink wrap is favored for a multitude of applications due to its superior qualities. It is known for its flexibility, high temperature resistance, and ability to conform to irregular shapes. \n
- Key Benefits:
- Excellent electrical insulation properties
- Wide operating temperature range
- Easy to use in various settings
Polyolefin is often the preferred choice for electronic components and wiring as it can provide protection from moisture and mechanical stress. The material's intrinsic qualities allow it to shrink consistently around the object, reducing the risk of exposing sensitive parts to external elements. Its transparency can also be an aesthetic advantage, allowing labels or the underlying object to be visible.
PVC Heat Shrink
PVC heat shrink offers a balance of affordability and functional performance. It is available in several thicknesses and shrink ratios, making it versatile for different tasks.
- Benefits of PVC Heat Shrink:
- Economical and widely accessible
- Good chemical resistance
- Enhanced flame-retardant characteristics
Though not as heat-resistant as polyolefin, PVC can still withstand considerable temperatures and is suitable for applications that do not demand extreme levels of durability. It is commonly used for insulating cables and protecting components in automotive and industrial environments. However, it is crucial to note that PVC may not perform well when exposed to certain solvents, limiting its applications in highly corrosive environments.
Rubber Heat Shrink
Rubber heat shrink wraps are designed for specialized applications, particularly in environments where flexibility and impact resistance are critical. Although less common than the previous two types, they serve essential roles in specific sectors.
- Advantages of Rubber Heat Shrink:
- Excellent elasticity and flexibility
- High resistance to abrasion and impact
- Good sealing properties for moisture protection
Due to these characteristics, rubber heat shrink is often employed in automotive and industrial applications, particularly for bundling and sealing sensitive components or connections. Its flexibility makes it easier to install in tight spaces, ensuring a secure fit that can adapt to various shapes.
When selecting heat shrink wrap, consider not only material cost but also the specific performance characteristics needed for your application.
Applications of Blue Heat Shrink Wrap
The applications of blue heat shrink wrap are diverse and fundamental in several industries. It serves not just as a protective layer but also as a means to signify inclusivity in various tasks. Understanding its applications aids users in making informed decisions about its utilization in their respective fields.
Electronics and Wiring
Blue heat shrink wrap plays an essential role in the electronics sector. Its primary usage is to insulate and protect wiring connections. In this sector, wires can be exposed to humidity, dust, and oil, among other contaminants. Blue heat shrink wrap acts as a barrier, reducing the risk of electrical shorts and ensuring longevity in devices. The color blue is often used to differentiate between components or assess the status of repairs visually.
Moreover, its application extends to cable management. Bundling multiple wires with blue heat shrink wrap can enhance organization, reduce clutter, and simplify maintenance. It offers a neat appearance and ensures that wires are bound with minimal room for movement, which can help prevent wear. These attributes highlight the functionality and necessity of blue heat shrink wrap in electronic setups.
Medical Devices
In the medical field, compliance with stringent safety standards is paramount. Blue heat shrink wrap finds applications in protecting sensitive wires in medical devices. This coating ensures that they can endure sterilization processes without degrading. The color-coding of blue wrap helps in easy identification, which is crucial in medical environments where quick responses can save lives.
Furthermore, using heat shrink wrap on medical devices minimizes the risk of contamination. Components wrapped in this material are less prone to collect dust or contaminants, leading to safer operations. Its flexibility ensures that it can conform to various shapes of medical instruments, providing both protection and functionality.
Automotive Use
In the automotive industry, blue heat shrink wrap finds its footing in multiple applications. Connecting wires that power electrical systems in vehicles often require protection against heat and moisture. The heat shrink wrap creates a robust insulation layer, ensuring the integrity of electrical connections. This is vital for the safety and performance of the vehicle.
This material can also be used for marking purposes. In complex wiring harnesses, differentiating circuits can mitigate confusion during repairs. Blue heat shrink wrap provides a reliable visual cue that assists technicians in understanding the electrical architecture of the car more efficiently. Because it does not hinder performance while facilitating easy identification, blue heat shrink wraps are favorable in the automotive sector.
Blue heat shrink wrap is not just a layer of protection; it is a strategic component that enhances functionality and safety in various industries.
The importance of understanding the applications of blue heat shrink wrap cannot be overstated. It serves critical roles across electronics, healthcare, and automotive sectors. This knowledge can influence decisions regarding its use effectively.
Advantages of Using Blue Heat Shrink Wrap
Blue heat shrink wrap offers several significant benefits that are vital for its use across multiple industries. Understanding these advantages fosters better choices for various applications, ensuring both performance and longevity. The properties of heat shrink wrap make it a favorable option for both professionals and everyday users alike. The following sections delve deeper into the specific benefits of using blue heat shrink wrap.
Protection Against Environmental Factors
One of the primary advantages of blue heat shrink wrap is its ability to protect components from environmental factors. This wrap acts as a barrier against moisture, dust, and other contaminants that can harm sensitive materials or electronics. For instance, in electronics, exposure to humidity can cause corrosion or short-circuiting. By using blue heat shrink wrap, users can effectively shield wires and components, thus enhancing overall reliability.
Moreover, UV protection is another critical element. Prolonged exposure to sunlight can degrade materials. Blue heat shrink wrap is formulated to resist UV rays, making it suitable for outdoor applications. Its color plays a dual role here. Not only does it help in identifying components quickly, but it also helps in reducing the heat absorption of the underlying surfaces.
Enhanced Durability
Durability is another key benefit associated with blue heat shrink wrap. This material is designed to withstand mechanical stress, making it resistant to tearing and cracking. When applied properly, the shrink wrap conforms tightly around the component, offering superior adhesion that resists peeling or lifting. This is particularly important in dynamic or fluctuating environments like automobiles or industrial settings.
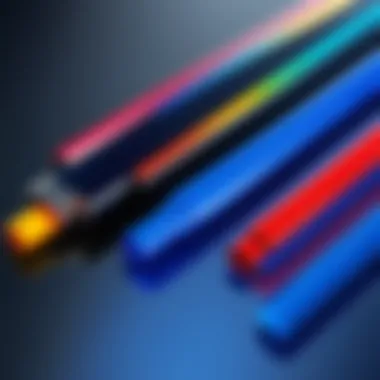
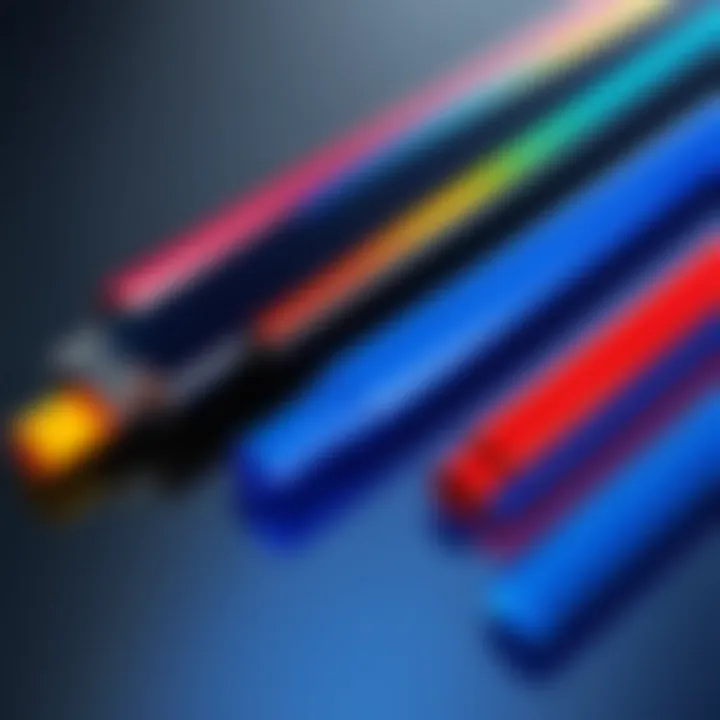
In many cases, the lifespan of protected components is significantly extended due to the added layer of durability. The wrap effectively absorbs impacts and vibrations that could otherwise reach sensitive areas. Using blue heat shrink wrap can translate to cost savings in the long term by reducing the frequency of repairs or replacements.
Color-Coding and Identification
The use of blue heat shrink wrap also offers practical advantages in terms of color-coding and identification. In environments where multiple wires or components are used, distinguishing between them can sometimes be a challenge. The blue color provides an easy way to categorize and identify connections or components quickly. This can be especially helpful in complex electronic systems, where organization is critical to efficient operation.
Furthermore, color-coding can enhance maintenance practices. Technicians can quickly locate specific wires without confusion, reducing the risk of errors during repairs or upgrades. The visual management of cables and components thus leads to more efficient workflows and minimizes the potential for mistakes.
In summary, the advantages of using blue heat shrink wrap extend beyond just protection; they enhance durability and organization, allowing users to maintain control over complex systems. By understanding these benefits, users can make informed choices that align with their needs.
Installation Techniques for Heat Shrink Wrap
Proper installation is crucial when working with blue heat shrink wrap. The techniques employed during installation can greatly influence the effectiveness of the product. This section highlights key techniques for preparing, applying, and inspecting heat shrink wrap to ensure optimal performance.
Preparing the Component
Before applying blue heat shrink wrap, the components involved must be prepared. This includes cleaning the surface of the wire or component. Any residual dirt, grease, or contamination can hinder the adhesion of the wrap. Use a suitable cleaner, such as isopropyl alcohol, on a lint-free cloth to cleanse the area thoroughly. Once cleaned, the component should be dry before applying the wrap.
Additionally, it is essential to measure the length of the heat shrink wrap carefully. Too short a piece may not provide adequate coverage, while too long could lead to unevenness when shrinking. It's wise to cut the wrap with precision, taking into account the diameter of the component and any additional coverage needed for overlaps.
Applying Heat Evenly
Applying heat is the next critical step. It is vital that heat is distributed evenly across the surface of the wrap. Uneven heating can cause the material to shrink erratically, resulting in gaps or over-tightening, which may damage the component underneath.
Using a heat gun is recommended for this process. Hold the heat gun at a distance of about 6 to 8 inches from the wrap. Move the heat gun in a circular motion, ensuring that all areas of the wrap receive equal heat. This method helps in achieving a smooth and uniform shrink.
It is important to note that applying too much heat can lead to damaging the wrap. Monitoring the temperature and adjusting distance accordingly can yield the best results. Keep the heat gun moving to avoid overheating any single area.
Cooling and Inspection
After the heat application, allow the blue heat shrink wrap to cool naturally. Cooling helps in solidifying the material and ensuring a secure fit around the component. Avoid handling the wrap while it is still hot to prevent accidents or burns.
Once cooled, perform a thorough inspection of the installed wrap. Check for any imperfections, such as bubbles, gaps, or uneven surfaces. Imperfections can compromise the protective qualities of the heat shrink wrap. If any issues are observed, it may be necessary to remove and reapply the wrap to ensure complete protection.
Key Takeaway: Proper preparation, even heat application, cooling, and inspection are vital for ensuring effectiveness and durability of blue heat shrink wrap installations.
By understanding these installation techniques, users can maximize the benefits of blue heat shrink wrap, thereby enhancing protection for their electronic components and wiring.
Safety Considerations
Understanding the safety considerations when using blue heat shrink wrap is crucial for ensuring both the effectiveness of the product and the safety of the user. Proper use can prevent accidents and ensure high-quality insulation. This section will explore two key aspects of safety: avoiding overheating and handling precautions.
Avoiding Overheating
Overheating during the shrink process can result in significant issues. If excessive heat is applied, it can lead to deformation, melting, or even combustion of the material. This is especially relevant for sensitive components in electronics.
To prevent overheating, consider the following practices:
- Use Appropriate Tools: Employ heat guns that allow for temperature control. Keep the heat source at a safe distance from the material to avoid concentrating heat in one spot.
- Monitor Temperature: Utilize infrared thermometers to track surface temperatures. This helps to ensure that the material does not exceed safe operating conditions.
- Test Before Full Use: Before applying heat shrink wrap on important components, conduct tests on scrap material to assess the heating requirements properly.
Important Note: Improper heating can lead to fires or damage to delicate electrical components, emphasizing the necessity of precision in application.
Handling Precautions
Safe handling of blue heat shrink wrap is essential for minimizing risks during installation. This process often involves sharp tools and equipment that can cause harm if not used correctly. Here are some key guidelines for safe handling:
- Protective Gear: Always wear safety goggles and gloves to protect against cuts and thermal injuries. These simple precautions significantly reduce injury risk.
- Work Environment: Ensure that installation is conducted in a clean and organized space. Clear clutter to reduce the chance of accidents or interruptions during application.
- Storage Conditions: Store heat shrink wrap in a cool, dry place, away from direct sunlight. Prolonged exposure to heat or UV rays can degrade the material, making it less effective when used later.
Taking these safety measures seriously can lead to enhanced effectiveness of blue heat shrink wrap while ensuring user protection. Being vigilant about overheating and following handling precautions can mitigate risks in both professional and personal projects.
Market Trends and Innovations
The world of blue heat shrink wrap is continuously evolving. Keeping an eye on market trends and innovations is crucial for professionals and enthusiasts alike. It allows for informed decision-making that can increase the efficiency and effectiveness of applications. Understanding the aspects of emerging technologies and sustainability in material production provides a roadmap for the future of heat shrink wrap usage. For optimally effective applications, awareness of these trends is essential.
Emerging Technologies in Heat Shrink Wrap
Technology plays a significant role in the development of blue heat shrink wrap. Several advancements have emerged to improve performance and application scenarios.
- Smart Materials: These materials can respond to environmental stimuli. For instance, some heat shrink wraps can change color when exposed to high temperatures, indicating potential issues. This capability enhances safety and monitoring.
- Nano-coatings: Innovations in nano-coatings are making heat shrink wraps more resistant to scratches and abrasions. This extends the lifespan of the wrap, making it preferable for various demanding applications.
- Advanced Bonding Techniques: New bonding methods have improved the adhesion of heat shrink materials to different substrates. This ensures a tighter and more reliable seal, critical for applications such as electronics where moisture protection is essential.
Ultimately, these technologies are not just about performance. They also cater to specific needs within different industries. For example, the electronics sector may benefit significantly from improved thermal management properties.
“The advancement in heat shrink technologies showcases a shift towards smarter and more adaptable solutions, catering to a broader range of applications.”
Sustainability in Material Production
Sustainability is another focal point in the production of blue heat shrink wrap. As environmental concerns grow, manufacturers are increasingly responsible for their materials.
- Biodegradable Options: Some companies now offer biodegradable heat shrink wraps. This product line facilitates eco-friendly disposal, significantly reduces the environmental footprint.
- Recycling Schemes: Many manufacturers implement recycling programs. Users can return used heat shrink wraps, allowing materials to be repurposed rather than discarded.
- Reduced Carbon Footprint: New production methods aim to minimize energy consumption during manufacturing. By focusing on lower energy inputs, manufacturers can produce heat shrink wrap in a more environmentally conscious manner.
These initiatives reflect an industry shift toward responsible production practices. Importantly, they cater to a growing consumer base that prioritizes sustainability.
In summary, understanding the current market trends in blue heat shrink wrap enhances knowledge of its applications. Informed decisions can only be made by staying updated on emerging technologies and the commitment to sustainability.
Comparative Analysis with Other Protectants
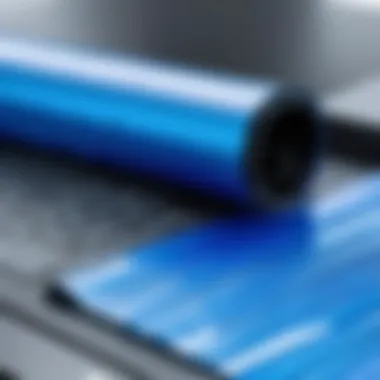
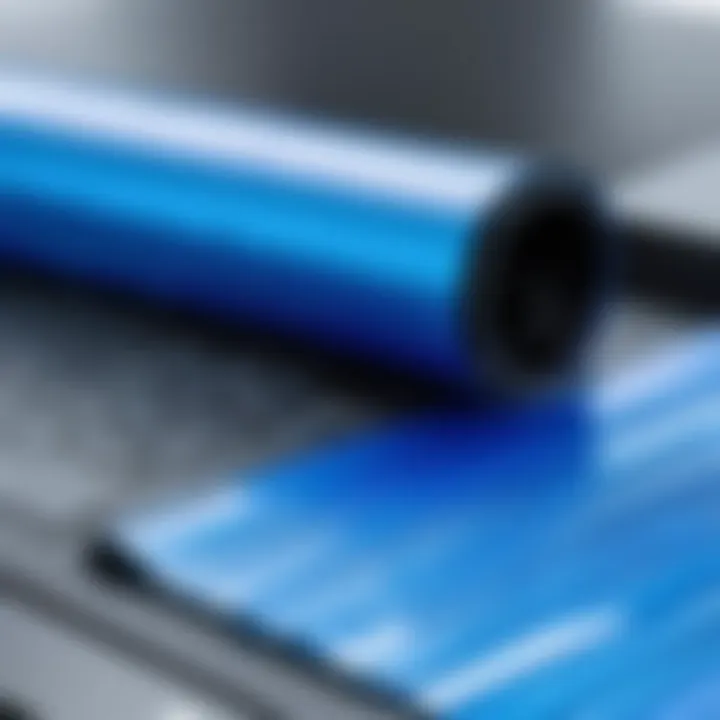
When it comes to protecting delicate components in electronics and hardware, the choice of material is crucial. Various options exist, each with distinct features and benefits. This section provides a comparative analysis of blue heat shrink wrap with other common protectants like electrical tape and liquid insulation. Assessing these differences helps in making an informed decision suited to specific applications.
Heat Shrink vs.
Electrical Tape
Electrical tape is a popular choice for insulation and protection, often used by both professionals and DIY enthusiasts. It is made from flexible vinyl and can be easily applied by hand. However, blue heat shrink wrap offers several advantages that can make it more suitable in certain circumstances.
- Durability: Heat shrink wrap is known for its stronger resistance to abrasion and environmental factors. While electrical tape can wear out over time, heat shrink maintains its integrity.
- Temperature Resistance: Heat shrink wrap generally withstands higher temperatures compared to electrical tape. This makes it more reliable in applications where heat exposure is a concern.
- Sealing Properties: Once shrunk, heat shrink wrap provides a tight fit around components, offering superior protection against moisture and dust. Electrical tape can lose adhesion and may not form a secure seal.
- Aesthetic Appeal: Blue heat shrink wrap is available in various colors, aiding in organization and identification. Electrical tape, while also available in colors, does not offer the same level of uniformity in appearance.
In summary, while electrical tape is suitable for quick fixes, blue heat shrink wrap is often the better choice for long-term protection and durability.
Heat Shrink vs.
Liquid Insulation
Liquid insulation is another alternative used to protect electrical components. It involves applying a liquid polymer that hardens and forms a protective layer. Although it has certain advantages, there are key considerations that make blue heat shrink wrap a preferred choice in many situations.
- Ease of Application: Heat shrink is easier to use. It simply requires sliding over a component and applying heat, while liquid insulation requires careful mixing and curing time.
- Mess Factor: Liquid insulation can be messy and requires protective measures to avoid unwanted spills. Heat shrink wrap is cleaner and more straightforward in application.
- Clarity and Transparency: For tasks where visibility of components is essential, heat shrink can be found in clear forms or colors like blue, allowing easy identification of the insulated area. Liquid insulation, once applied, obscures the components completely.
- Reworkability: Heating and removing blue heat shrink wrap is more straightforward than peeling off cured liquid insulation. This is a significant factor for scenarios where components might need to be replaced or adjusted.
Overall, while liquid insulation serves its purpose, blue heat shrink wrap tends to offer a more user-friendly and practical solution for most electrical applications.
In choosing the right protectant, always consider specific application requirements, material properties, and the environment where the product will be used.
Choosing the Right Heat Shrink Wrap
Selecting the proper heat shrink wrap is critical to ensuring that your projects meet both safety and performance standards. Understanding the nuances involved in this selection process allows users, especially those in electronics and hardware, to optimize their applications. The consideration of various factors can lead to better functionality, longevity, and cost-effectiveness in the use of heat shrink wrap.
Factors to Consider
Before diving into the specifics of choosing heat shrink wrap, it is important to understand key factors that can impact your selection:
- Material Properties: Different types of heat shrink materials, such as polyolefin or PVC, have distinct characteristics, impacting their suitability for specific applications.
- Temperature Resistance: Ensure that the heat shrink material can withstand the operational and environmental conditions it will encounter.
- Flexibility and Strength: Assess whether the selected wrap maintains flexibility while providing adequate protection against physical and environmental conditions.
- Adhesive Properties: Some heat shrink wraps offer adhesive backing that can enhance bonding with the substrate, which may be necessary for reliability in some applications.
Making informed choices based on these factors can greatly improve the performances of electronic components or systems that utilize heat shrink wrap.
Size and Compatibility
Choosing the right size of heat shrink wrap ensures that it fits snugly around the components it is protecting. Factors here include:
- Diameter Measurements: It is essential to measure the diameter of the wire or component to ensure proper coverage after shrinking.
- Shrink Ratio: Different wraps come with varying shrink ratios, from 2:1 to even 6:1. Knowing the right shrink ratio helps in selecting a product that minimizes excess material while maximizing protection.
- Compatibility with Components: Not all heat shrink wraps can interact well with every material and component. Examining the chemical reactivity of the heat shrink wrap with your materials ensures that the longevity and effectiveness of protection are maintained.
Understanding these factors not only elevates the quality of your project but also promotes sustainability by preventing excessive waste due to improper sizing and material selection.
“Selecting the right heat shrink wrap is as much about understanding the material characteristics as it is about ensuring compatibility with your components.”
In summary, the selection process of heat shrink wrap should emphasize the intricacies that differentiate types and sizes. A methodical approach ensures that users make thoughtful choices that align with their project requirements, enhancing the overall efficacy and reliability.
Cost Analysis
Understanding the cost implications of blue heat shrink wrap is essential for both individuals and businesses alike. The cost analysis helps in evaluating options available in the market. Several factors influence these costs, including material types, sizes, and suppliers. A thorough knowledge of these elements can greatly impact budgeting decisions and overall project viability.
Price Variations by Type
Different types of heat shrink wraps come with varying price points. Here are some examples:
- Polyolefin Heat Shrink: Generally priced on the lower end, polyolefin is popular for its balance between cost and functionality.
- PVC Heat Shrink: This is more affordable but may not always meet the specific needs of high-performance applications.
- Rubber Heat Shrink: Often found at the higher end of the price spectrum, rubber offers superior durability and flexibility.
The price can also vary depending on brand reputation, packaging size, and special features such as flame retardance or UV resistance.
Long-Term Value Assessment
While initial costs are important, the long-term benefits of using blue heat shrink wrap must not be overlooked. Investing in higher-quality materials may prove economically advantageous over time.
- Durability: More costly variants tend to have a longer lifespan, offering better protection. This can reduce replacement and maintenance costs.
- Performance: Higher-performing wraps can save time and effort in repairs and replacements, which can translate to cost savings in labor.
- Functionality: Depending on the application, choosing the right type of heat shrink can lead to enhanced safety and reliability, potentially lowering liability costs.
In summary, evaluating both the upfront costs and long-term benefits of blue heat shrink wrap is crucial. Making an informed decision could lead to better resource allocation and enhanced project outcomes.
"Quality often outweighs the immediate savings in cost."
By understanding the cost implications involved, professionals can make better choices that align with their specific needs and budgets.
The End and Future Considerations
In the realm of electronics and hardware, blue heat shrink wrap plays a vital role. Its significance cannot be overstated when discussing applications and benefits. This section aims to synthesize the ideas presented throughout the article, focusing on the enduring relevance of blue heat shrink wrap in multiple fields. The adaptability, protection, and identification it provides is essential for both consumers and industries alike.
Recap of Benefits
To summarize the key benefits of blue heat shrink wrap:
- Environmental Protection: The material offers resistance to moisture, dust, and other detrimental factors, which ensures that components remain functional over prolonged use.
- Durability: The enhanced material properties contribute to longer lifespan, helping users to reduce maintenance costs over time.
- Color-Coding: The blue hue not only facilitates easy identification but also assists in organizing components, making work more efficient.
Understanding these benefits is crucial for those who rely on this material for their projects and products. Integrating heat shrink wrap into design and repair processes can significantly elevate product integrity.
Looking Ahead
As technology progresses, the future of blue heat shrink wraps looks promising. Considerations for sustainability and eco-friendliness in material production will likely drive innovation. Manufacturers may invest in developing more advanced materials that contribute positively to the environment.
Furthermore, with the rise of smart devices and IoT applications, the demand for reliable insulative solutions like blue heat shrink wrap will increase. Innovations in shrink wrap technologies can open new doors for applications, from improving thermal efficiency to enhancing the safety of electronic components.
By keeping an eye on market trends and adapting to emerging technologies, businesses and consumers alike can better utilize this essential protective solution.