Understanding Tool Replacement Cords: A Comprehensive Guide

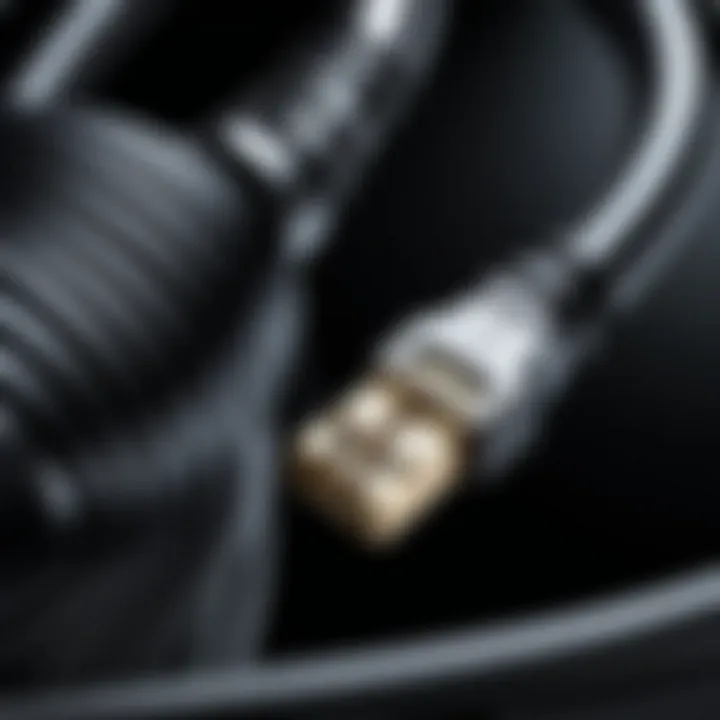
Intro
Tool replacement cords play a vital role in the performance and safety of electrical tools. As technology evolves, these cords become more significant in maintaining operational efficiency. Understanding the nuances of tool replacement cords helps users ensure longevity and reliability of their devices.
A tool replacement cord is not only a simple accessory but a critical component of any electrical tool. This guide delves into the technical specifications and practical applications of these cords. Each section examines different elements, such as compatibility with various tools, performance metrics, and emerging industry trends. By grasping these concepts, tech-savvy consumers, hardware enthusiasts, and everyday users can enhance their tool usage and maintenance practices.
In this comprehensive guide, we will explore the following topics:
- Technical Specifications
- Product Comparisons
- Practical Applications
- Latest Trends
- Buying Guides
Each section provides insightful information to empower readers with the knowledge to make informed decisions. This guide aims to serve as a reliable resource for ensuring optimal performance of tools using proper cord management and maintenance practices.
Intro to Tool Replacement Cords
Tool replacement cords play a crucial role in the functionality and reliability of electric tools. As essential components, they connect the tool to a power source, ensuring seamless operation. Their importance cannot be overstated. A well-functioning cord not only enhances efficiency but also promotes safety during tool use. Understanding various types of replacement cords, their specifications, and installation tips is vital for both seasoned professionals and everyday users.
Definition and Purpose
Tool replacement cords are specialized wires designed to connect power tools to a power outlet. They serve the primary purpose of supplying electrical power, allowing tools to operate effectively. Unlike standard cords, replacement cords are made to withstand the demands of specific tools, ensuring durability and longevity. When a tool’s original cord becomes damaged or worn out, a replacement cord is essential to restore functionality and maintain safety standards.
Choosing the right replacement cord is significant for several reasons. Firstly, compatibility with the tool’s specifications ensures that it operates at optimal performance. Secondly, proper installation mitigates risks associated with electrical hazards, reducing the likelihood of shocks or fires. Therefore, understanding the definition and purpose of tool replacement cords prepares users for selecting and maintaining these crucial components.
The Role of Cords in Power Tools
In power tools, cords serve as the lifeline that connects the tool’s motor to the electrical supply. They conduct voltage and current needed for operation. Without a suitable cord, tools may experience malfunctions, reduced performance, or complete inoperability. The relationship between cords and power tools is symbiotic; the cords rely on the integrity of electrical systems while simultaneously impacting the tools’ effectiveness.
Cord design varies significantly based on the type of tool and its power requirements. For instance, heavy-duty tools require cords that can handle greater voltage and current levels, while lighter tools may function with standard cords. Furthermore, the material and insulation of the cord play a vital role in safety and efficiency. A robust and resistant cord can prevent overheating and damage, ensuring that the tool remains functional over extended periods.
"Understanding the role of cord in power tools leads to informed replacement choices, enhancing both effectiveness and safety."
Types of Tool Replacement Cords
Understanding the different types of tool replacement cords is essential for maintaining power tools effectively. The right cord can enhance tool performance, ensure worker safety, and even prolong the lifespan of the device. Each type has its unique characteristics, and being aware of these can help consumers make informed choices.
Standard Electrical Cords
Standard electrical cords are the most common type of replacement cords used for everyday power tools. These cords are typically rated for a specific amperage and voltage. Essentially, they are designed to handle regular household tasks without straining the electrical supply. Standard cords come in various lengths, which allows users to select a suitable length based on their workspace requirements.
Features of standard cords include:
- Amperage Ratings: Usually rated for 15 amperes, which is standard for most home tools.
- Voltage Ratings: Typically rated at 120 volts, perfect for most appliances in regions using this standard.
- Cable Insulation Types: Commonly made from rubber or PVC, providing adequate insulation against electrical risks.
These cords are ideal for light to moderate tasks but might not suit heavy-duty applications. Always check the specifications to ensure compatibility with your tools.
Heavy-Duty Cords
Heavy-duty cords are a step up from standard cords. They are constructed to handle more significant electrical loads and withstand more demanding working conditions. Such cords are suitable for larger power tools that require higher amperage. Users should consider investing in heavy-duty cords when using professional-grade devices that place a high-demand on electrical systems.
Key attributes of heavy-duty cords are:
- Higher Amperage Ratings: Often rated for 20 to 30 amperes, accommodating robust machines.
- Durable Materials: Often made from advanced latex or thermoplastic rubber, providing resilience and weather resistance.
- Thicker Gauge Wire: Heavy-duty cords typically utilize lower gauge wire to support more load and reduce energy loss.
These are especially important for safety, as using inadequate cords can lead to overheating or electrical fires.
Extension Cords
Extension cords are crucial in scenarios where the original power tool cord does not reach an outlet. They come in various lengths, allowing users flexibility in placement and use. Extension cords are often rated for both amperage and voltage and can be used effectively with many tools, given that the continuous load does not exceed the cord’s rating.
Considerations when using extension cords include:
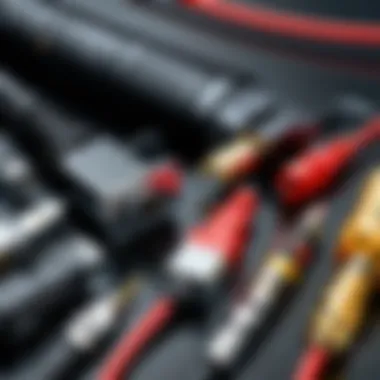
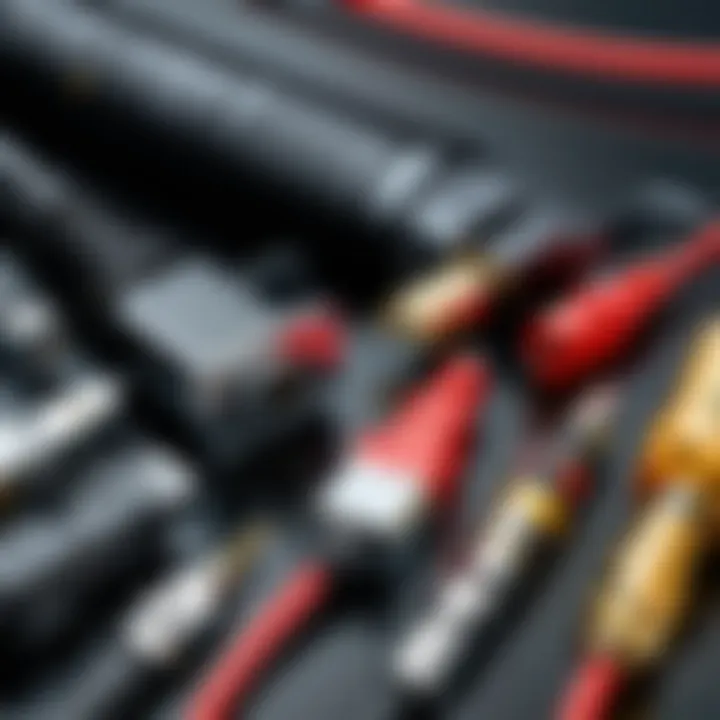
- Length and Gauge: Longer cords can result in voltage drops, so a thicker gauge (lower number) is recommended for longer lengths.
- Indoor vs. Outdoor Use: Make sure to choose an extension cord suited for the environment; outdoor cords have added insulation.
Extension cords provide convenience but also require proper usage to avoid hazards. Overloading can lead to electrical issues.
Specialty Cords
Specialty cords cater to particular needs and environments. These include cords with features like extra length, unique connectors, or special insulation properties. For instance, some cords are designed to withstand extreme temperatures or moisture, making them suitable for industrial applications.
Different varieties of specialty cords include:
- Cold Weather Cords: Designed to stay flexible at low temperatures, perfect for outdoor use.
- Retractable Cords: Built for ease of storage, retractable cords can help to reduce clutter and are often used in professional settings.
- Custom Length Cords: These cords can be manufactured to specific lengths for unique installations.
Understanding these different uses can help consumers select the right type for their specific applications.
Proper awareness of different cord types maintains tool efficiency and user safety.
In summary, the choice of tool replacement cords will significantly affect how power tools perform. Selecting the appropriate cord involves assessing the tool's needs, environmental conditions, and safety standards. This knowledge ensures optimal use and prevents unexpected interruptions during work.
Specifications of Tool Replacement Cords
The specifications of tool replacement cords are critical for ensuring safe and efficient operation of power tools. These specifications dictate the performance, longevity, and safety of the cords used with electrical devices. Understanding the specifications helps consumers and enthusiasts choose the right cord for their needs. The proper cord enhances tool functionality and reduces risks associated with electrical failures or accidents.
Gauge and Length Considerations
When selecting a replacement cord, gauge and length are paramount considerations. The gauge of a wire indicates its thickness, which affects the amount of current it can safely carry. Common gauges for tool replacement cords include 14, 12, and 10 AWG, where a lower gauge number signifies a thicker wire. Thicker wires can handle higher currents without overheating.
The length of the cord also matters. A longer cord may lead to voltage drop, reducing tool efficiency. Therefore, the gauge must be appropriate for the length chosen. For instance, if one is using a long cord, it may be necessary to opt for a thicker gauge to mitigate any potential drop in voltage. A short cord may use a higher gauge without risk, allowing flexibility based on the user's environment.
Voltage and Current Ratings
Every tool replacement cord comes with specific voltage and current ratings, which denote the maximum limits that the cord can handle safely. Knowing these ratings ensures that the cord will operate reliably without overheating or causing damage to the tool plugged into it. Most residential tools operate on standard voltages, typically around 120 volts. However, some industrial tools may operate at 240 volts.
Current ratings, expressed in amperes, are equally crucial. A cord rated for a tool with higher amperage will ensure safety and performance. When using a device that requires significant power, it is crucial to confirm that the cord can handle the expected load. Ignoring these ratings can lead to failure of the cord, damage to the tool, or even electrical hazards.
Wire Insulation Types
The insulation of a cord serves as the first level of protection against electrical hazards. Various materials are used for insulation, each suited for specific conditions. Common wire insulation types include thermoplastic elastomer (TPE), polyvinyl chloride (PVC), and rubber. Each type has unique properties regarding durability and flexibility.
- Thermoplastic Elastomer (TPE): Offers excellent flexibility and resistance to cracking, making it suitable for cold environments.
- Polyvinyl Chloride (PVC): Commonly used due to its cost-effectiveness and moderate resistance to damage.
- Rubber: Provides superior resilience and performance under extreme temperatures.
Selecting the appropriate insulation material impacts the longevity of the cord and its ability to perform in diverse environments. Using cords with proper insulation prevents deterioration and enhances safety during operations.
Selecting the Right Tool Replacement Cord
Selecting the appropriate tool replacement cord is a critical part of maintaining not only the functionality of tools but also the safety of the user. A wrong choice can lead to performance issues or even potential safety hazards. Several factors must be considered to ensure that the replacement cord meets the necessary requirements for the specific tool in use. Here, we will detail the primary elements that contribute to making an informed decision when choosing a replacement cord.
Assessing Tool Requirements
Before acquiring a replacement cord, it is essential to understand the power requirements of the tool for which it is being used. Each power tool has a defined voltage and current rating, which must be matched by the replacement cord. Check the specifications that are typically found on the tool itself or in its manual.
- Voltage: The replacement cord must support the voltage that your tool operates on. Using an under-rated cord can lead to overheating and potential failure.
- Current Rating: This reflects how much current the cord can safely carry. Confirm that the cord can handle the tool's maximum current draw without risk of damage.
Factors impacting these requirements include tool design and intended applications. Certain tools may require higher current capacities based on their size and operational demands.
Environmental Considerations
The environment in which the tool and cord will be used is another critical aspect to contemplate. Cords are often subjected to harsh conditions, which can affect their longevity and performance. Here are key considerations regarding the environment:
- Temperature Extremes: If the cord will be used in high or low-temperature environments, it is necessary to select cords rated for those conditions. Some cords can withstand extreme temperatures while others cannot.
- Moisture and Wet Areas: If the tool operates in damp or wet conditions, consider using cords with moisture-proof insulation. This increases safety and performance.
- Physical Wear and Tear: In work environments where cords might experience cuts or abrasions, protective coatings or reinforced cords are advisable to avoid damage.
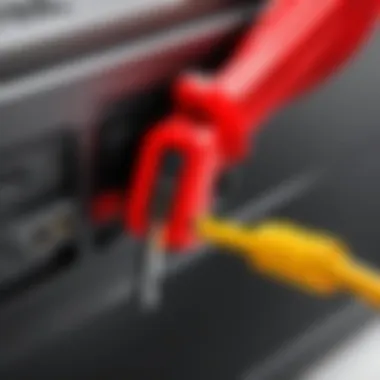
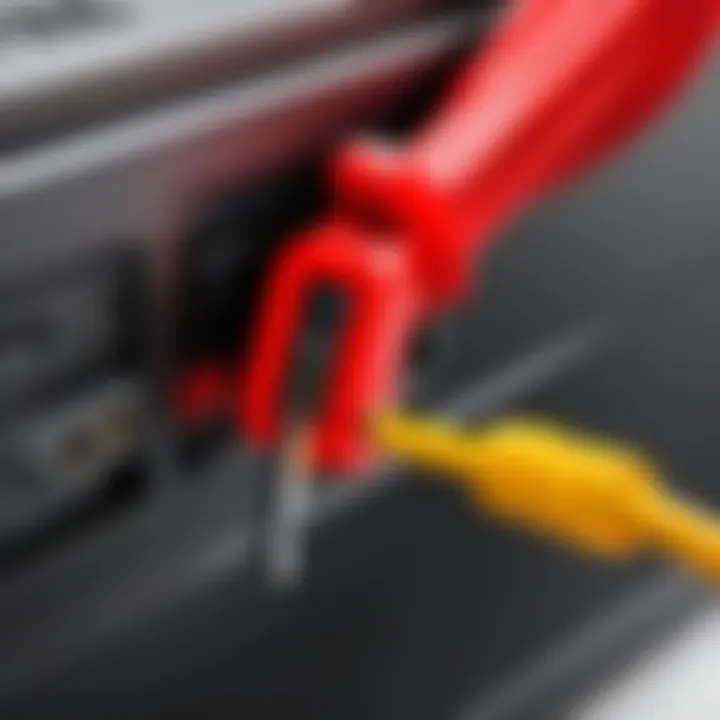
Compatibility with Tools
Ensuring that a replacement cord is compatible with the particular tool is crucial. Compatibility includes several aspects:
- Connector Type: The ends of the cord must match the connections on the tool. Many power tools use specific types of plugs and sockets that have distinct configurations.
- Cord Length: Consider how far the tool will be from an outlet. Too short of a cord can create hazards or limit utility. On the other hand, excessively long cords may lead to unwieldy setups.
- Application-Specific Needs: Certain tools have unique requirements based on their intended use, such as those needing flexibility or high mobility. It is wise to refer to the manufacturer’s guidelines for recommendations on replacement cords.
Installation and Replacement of Tool Cords
The process of installing and replacing tool cords is crucial to ensure that power tools work safely and efficiently. This practice contributes not only to the longevity of the tool but also to maintaining the safety of the user. A damaged or improperly installed cord can lead to electrical shorts, tool malfunctions, or even personal injuries. Understanding how to properly replace tools' cords is essential for tech-savvy consumers and users who prioritize safety and performance in their equipment.
Tools Required for Replacement
To successfully replace tool cords, specific tools are necessary. Having these tools ready before starting ensures that the process goes smoothly and safely. A basic toolkit should include:
- Wire cutters: for cutting the old cord to remove it with ease.
- Wire strippers: These help in stripping the insulation from the wires in the new cord for connection.
- Screwdrivers: A set of flathead and Phillips screwdrivers are needed to open up the tool casing.
- Soldering iron: This may be needed if soldered connections are present in the tool.
- Heat shrink tubing: Used to insulate newly connected wires for safety and durability.
- Multimeter: Optional, but useful for ensuring connections are correct before fully assembling the tool back.
Preparation with these tools will facilitate an efficient and safe cord replacement process.
Step-by-Step Replacement Process
The replacement process should be methodical to guarantee safety and functionality. Here is a step-by-step guide to replacing power tool cords:
- Unplug the tool from any power source to avoid electrical shock.
- Remove any screws holding the tool casing together.
- Open the casing carefully, taking note of how the original cord is connected.
- Cut the old cord close to where it connects to the tool.
- Strip the ends of the new replacement cord using wire strippers.
- Connect the new cord to the tool by either twisting the wires together or soldering them, depending on the tool’s design.
- Insulate the connections with heat shrink tubing or electrical tape to prevent short circuits.
- Reassemble the tool casing and securely tighten all screws.
- Test the tool with a multimeter to ensure proper connectivity before use.
- Plug in the tool and test it to confirm it operates correctly.
Following these steps can help prevent mistakes that might compromise tool performance.
Safety Precautions During Installation
Safety cannot be overstated when working on electrical items. Here are some key precautions:
- Always disconnect the power source before beginning work on any tool.
- Use insulated tools whenever possible to avoid electrical shock.
- Wear safety goggles to protect eyes from debris while working.
- Avoid working in wet conditions to minimize the risk of short circuits or electrocution.
- Ensure a clear workspace to prevent accidental cuts or trips that could lead to injuries.
- Consult the tool manual for specific information on handling and replacing cords specific to your model.
By maintaining awareness of these safety protocols, users can perform maintenance and replacements with greater confidence and security.
Remember: Proper installation and replacement of tool cords is not just a maintenance task; it is a commitment to safety and efficiency in your workspace.
Maintenance of Tool Replacement Cords
Maintaining tool replacement cords is crucial for ensuring both safety and functionality. A well-maintained cord can enhance the performance of power tools while minimizing the risk of accidents. Regular upkeep not only prolongs the lifespan of the cords but also guarantees that they operate at optimal efficiency. By being proactive with inspections and maintenance, users can avoid potential malfunctions that may compromise their work.
Regular Inspection Procedures
Regular inspections of tool replacement cords should not be overlooked. A visual check can reveal significant issues that could lead to failures. Here are some key steps to follow during the inspection process:
- Check for Visible Damage: Look for frays, cuts, or abrasions along the length of the cord. Any visible damage can be a sign that the cord needs repair or replacement.
- Examine Connectors and Plugs: Ensure that both the plug and connectors are intact. Loose connections can lead to overheating or intermittent power supply.
- Test for Functionality: Plug the tool into a power source and monitor its operation. If there are issues, such as flickering power, the cord may need to be inspected further or replaced.
- Look for Overheating Signs: If the cord feels excessively hot while in use, this could indicate a problem. It’s essential to address overheating immediately, as it can lead to more severe damages.
Perform these inspections regularly, ideally before each use, to maintain safe operation of your tools.
Cleaning and Storage Tips
Keeping tool replacement cords clean and stored properly can significantly impact their performance. Here are some practical tips:
- Use a Damp Cloth: For regular cleaning, a damp cloth can remove dust and debris from the surface of the cords. Avoid soaking the cords, as excess moisture can lead to electrical issues.
- Avoid Chemical Cleaners: Harsh chemicals can degrade the insulation on your cords. Stick to mild cleaning agents and water.
- Properly Coil Cords: When storing cords, they should be coiled neatly. Improper coiling can lead to kinks or damage that may not be immediately visible.
- Keep Away from High Temperatures: Store cords in a cool, dry place. Excessive heat can weaken insulation and contribute to failure over time.
- Label Each Cord: If you have multiple cords for different tools, labeling can save you time and ensure you are using the correct cord for each tool.
Regular maintenance actions, like inspections and careful storage, are vital to prolong the lifespan of your cords and ensure safe operation.
Common Issues with Tool Replacement Cords
Understanding common issues with tool replacement cords is essential for ensuring the longevity and effectiveness of your electrical tools. A faulty cord can lead to not only ineffective tool performance but also serious safety hazards. Addressing these issues proactively can save time and money, as well as ensure a safer work environment. This section will outline typical damage indicators, troubleshoot these issues effectively, and advise when it may be necessary to seek professional assistance.
Damage Indicators and Troubleshooting
Damage to a tool replacement cord often manifests in clear, observable signs. Recognizing these symptoms early can prevent further damage to the tool itself or potential hazards. Here are some common damage indicators:
- Fraying or Cracking: Inspect the insulation for signs of wear, fraying, or cracks. These are clear indicators that the cord may not be safe to use.
- Burn Marks: Any discoloration or burn marks on the cord’s surface suggest overheating, which could lead to a short circuit.
- Loose Connections: Check the plug and socket. If the connection feels loose or the cord frequently disconnects during use, it might indicate internal damage.
- Unusual Noise: If you hear buzzing or crackling sounds from the cord while in operation, this could signal electrical issues.
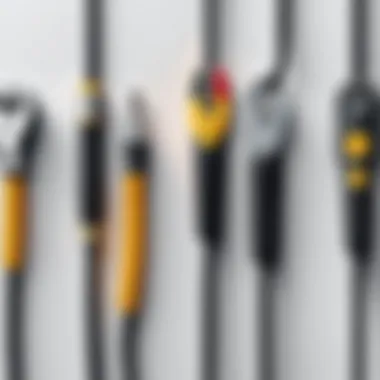
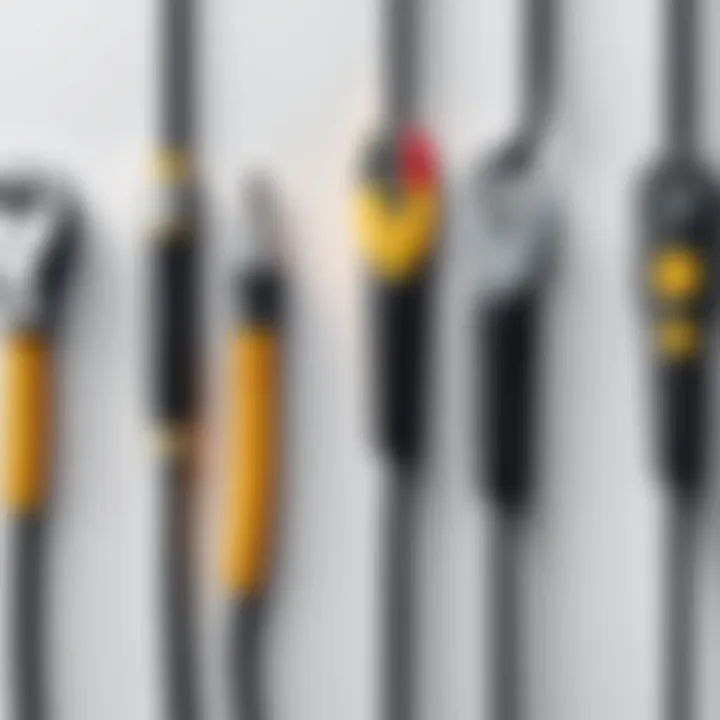
When troubleshooting these issues, here are few steps you can take:
- Visual Inspection: Regularly inspect the cord for any visible signs of damage or wear.
- Functional Test: If safe, test the tool with another compatible cord to rule out other potential issues.
- Check Plug Integrity: Ensure that the prongs are intact and not bent or broken.
- Examine the Outlet: Sometimes the issue may stem from the electrical outlet. Test the outlet with another tool or device.
In many cases, addressing these minor issues can restore functionality. However, if the cord is severely damaged, replacing it might be the only option.
When to Seek Professional Help
While many minor issues can be resolved independently, there are specific instances where consulting a professional is the safest course of action. Here are some guidelines on when to seek expert assistance:
- Severe Damage: If the cord is extensively frayed or has visible sparks, it is best to stop using it immediately and consult a professional.
- Complex Tool Systems: For sophisticated tools or systems, it is crucial to ensure that any cord replacement is compatible with the tool's electrical requirements. An expert can assist in this evaluation.
- Electrical Hazards: If you suspect that the cord might be linked to wider electrical problems in your home or workspace, professional intervention is advisable.
- Uncertainties About Safety: If there is any uncertainty about how to safely replace a cord or whether a tool is safe to use, a professional’s insight can be invaluable.
Safety Standards and Regulations
Understanding Electrical Safety Standards
Electrical safety standards are pivotal in maintaining safe practices when using tool replacement cords. These standards, set by various organizations, dictate how products are designed, tested, and implemented in the market. Compliance with these standards ensures that cords will function safely under their specified electric loads. They also help mitigate risks such as short circuits, overheating, and electrical shocks.
Adhering to established safety standards provides a framework that manufacturers must follow. For instance, the Underwriters Laboratories (UL) sets stringent criteria for safety testing. Cords that carry the UL mark have been tested and certified, assuring buyers of their safety. Moreover, the Institute of Electrical and Electronics Engineers (IEEE) also offers guidelines that assist in the design and application of tool replacement cords.
In practice, understanding these standards aids users in selecting the right cords for their specific tools. It allows for better decision-making steps regarding cord assessments. In many cases, knowledge of electrical safety standards may prevent accidents and equipment failures.
Industry Regulations for Cords
Regulation of tool replacement cords is not just about safety, it encompasses performance aspects as well. Each type of cord has its own set of regulations that manufacturers must abide by. These regulations ensure cords not only meet safety requirements but also perform effectively under various conditions.
In the U.S., the National Electrical Code (NEC) provides guidance on the proper installation and use of electrical cords. This includes guidelines that delineate ratings for voltage and current, as well as specifications for wire insulation. Moreover, there are regulations to ensure environmental adaptability, ensuring cords can withstand different weather conditions without risk of damage.
Sometimes, industry organizations may also update regulations based on emerging technologies or new safety concerns. Therefore, staying informed about these changes is crucial for both manufacturers and consumers. Doing so ensures that cords utilized in homes and workplaces meet the latest safety and performance standards.
Understanding and adhering to these safety standards is essential for avoiding hazards and ensuring optimal performance of tools.
The Future of Tool Replacement Cords
As technology advances, the design and functionality of tool replacement cords are evolving. Understanding these developments is crucial for consumers who rely on effective and safe tools. The changes in this sector will impact how users maintain their tools and ensure optimal performance over time.
Technological Developments in Cord Design
The future of tool replacement cords will be shaped by significant technological advancements. Manufacturers are increasingly focusing on making cords that are not only more durable but also safer. One trend is the integration of smart technologies into cord designs. These smart cords can monitor power consumption and detect faults in real time, providing immediate feedback to users. This feature is particularly beneficial in preventing hazards that may arise from overheating or overload.
Another area of improvement is in the flexibility and weight of cords. New materials are allowing for thinner and lighter cords without sacrificing strength. This makes them easier to handle and reduces the fatigue that users may experience during prolonged use. Cords are also being designed with enhanced resistance to wear, and environmental factors such as water and chemicals, which is critical for outdoor or heavy usage.
Sustainable Materials and Replacement Cords
Sustainability is becoming increasingly important in many industries, and the production of tool replacement cords is no exception. Consumers are showing a preference for products made from eco-friendly materials. This includes cords made from recycled plastics and other sustainable materials, which helps reduce environmental impact.
Using sustainable materials comes with benefits. For one, it can lead to lower production costs as raw materials become more abundant. Moreover, manufacturers who adopt these practices position themselves favorably in the market, appealing to environmentally conscious consumers. Products crafted from sustainable materials can also enhance durability, offering better performance over time.
Further, there is a movement towards creating biodegradable options. While still in development, this innovation could revolutionize how cords are disposed of, significantly lowering their ecological footprint.
The shift towards sustainable materials is not just a trend; it reflects broader consumer values and aligns with global initiatives to reduce waste and enhance environmental stewardship.
Closure
The conclusion of this article encapsulates the essence of tool replacement cords, outlining their critical role in ensuring functionality, safety, and efficiency of power tools. It emphasizes the need for users to understand the specifications and types of cords available, which are fundamental in selecting the right replacements for specific tools. Recognizing how these cords operate can lead to better maintenance practices, thereby enhancing the longevity of both the cords and the tools they serve.
Summary of Key Points
In summary, the importance of tool replacement cords can be summarized into several key points:
- Functionality: Cords are integral for the operation of power tools; choosing the correct cord maximizes performance.
- Safety: Proper usage and maintenance minimize risks of electrical hazards, ensuring safe operation.
- Specifications: Understanding gauge, voltage, and insulation types directly impacts the selection process.
- Maintenance: Regular inspections and cleaning can prevent damage and extend the lifecycle of the cords.
- Trends: Emerging technological advances are leading to more efficient and sustainable cord options suitable for diverse requirements.
"Proper management of tool replacement cords extends beyond usability; it lays the groundwork for an entire tool ecosystem that operates safely and effectively."
Final Thoughts on Cord Maintenance
Maintaining tool replacement cords should never be an afterthought. Regular inspection is essential to catch signs of wear before they escalate to more significant issues. Users should ensure cords are kept away from extreme temperatures, sharp edges, and heavy machinery where abrasion can occur. Cleaning the cords after use, along with proper coiling and storage, greatly contributes to their longevity.