The Precision of Small Cutting Wheels for Drills
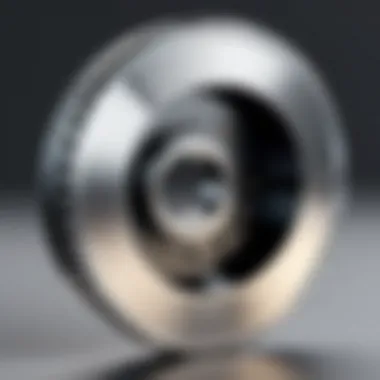
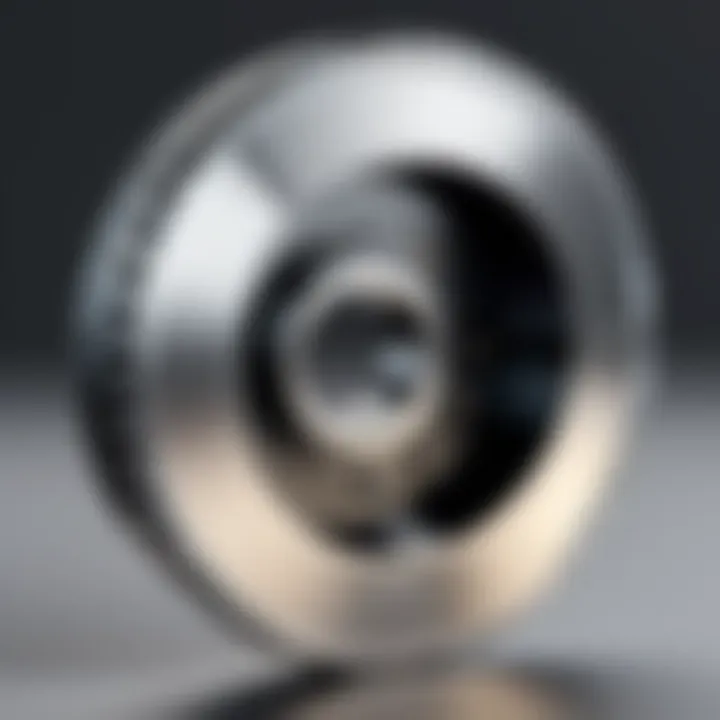
Intro
In the world of power tools, precision is king, especially when it comes to cutting tasks. Small cutting wheels for drills might not be the biggest component in your toolbox, but they sure pack a punch when it comes to efficiency and versatility. Rather than assuming that bigger is always better, this article casts a spotlight on these compact tools. Weâll cover their technical specifications, practical applications, and the latest trends to help you understand why these cutting wheels should be part of your toolkit.
Technical Specifications
When evaluating the capabilities of small cutting wheels for drills, it's essential to delve into their technical specifications. These specifications aren't just numbers; they provide insight into the performance and suitability of these tools for various materials.
Detailed Product Specs
Each cutting wheel comes with a unique set of specifications that can make or break your project. Look out for:
- Diameter: Common sizes range from 1.5 inches to 4 inches, affecting both the type of cuts and the precision.
- Thickness: Thinner wheels provide cleaner cuts but have a shorter lifespan, while thicker wheels offer durability at the cost of finesse.
- Material Composition: Wheels may be made from various elements such as diamond, aluminum oxide, or silicon carbide, each tailored for specific materials.
Performance Metrics
Assessing performance metrics like cutting speed and lifespan can guide your selection:
- Cutting Speed: Measured in RPM (Revolutions Per Minute), the ideal speed depends on the material being cut.
- Durability: The longevity of the wheel is directly tied to its material and thickness, so consider your usage frequency.
Compatibility Information
Compatibility is crucial. Not every wheel fits every drill. Check:
- Shank Size: Most cutting wheels come with a mandrel, and ensuring that it matches your drill bit holder is key.
- Drill Type: Whether youâre using a rotary drill, angle grinder, or dremel tool, make sure the wheel is designed for that specific application.
Practical Applications
Small cutting wheels shine in numerous applications ranging from professional tasks to DIY projects at home. Here are some insights:
Use Cases for Different Users
- DIY Enthusiasts: Perfect for small-scale projects, these wheels allow you to slice through wood or plastic effortlessly.
- Professional Contractors: Industrial-grade wheels can tackle tougher jobs, like cutting metal or thick tiles, often yielding a cleaner finish than larger saws.
Recommended Configurations
For optimal performance, consider these configurations:
- Low RPM for Metals: Use lower speeds with thicker wheels to reduce the risk of overheating.
- High RPM for Wood: When cutting wood, higher speeds with thinner wheels can accelerate your project without sacrificing cleanliness.
Multi-Platform Performances
Whatâs remarkable is their versatility across tools. You can switch between a drill, angle grinder, or even a dremel without hassle.
Latest Trends
The cutting wheel market is evolving rapidly, with emerging technologies and changes in industrial practices shaping its future.
Industry Developments
The industry is seeing significant advancements in material engineering, making cutting wheels stronger and more efficient. New compositions like advanced composites are gaining traction.
Emerging Technologies
Laser treatment and precision engineering are changing the game. This not only improves durability but also provides enhanced performance metrics that users can rely on.
Future Predictions
As more consumers embrace precision tools, the trend will likely lean towards eco-friendly and sustainable product lines, ensuring that cutting wheels are not just efficient but also environmentally responsible.
Buying Guides
Choosing the right cutting wheel can be daunting. Here are some tips to ease the process:
Recommended Products
Some of the top contenders in the market include brands like Dremel, DEWALT, and Makita, each with its own line of specialized cutting wheels.
Purchasing Tips
- Always check compatibility with your tools.
- Donât skimp on quality; sometimes paying a bit more upfront leads to significant savings in the long run.
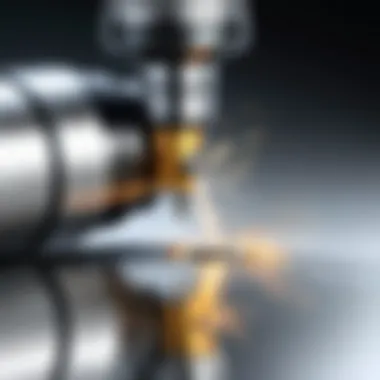
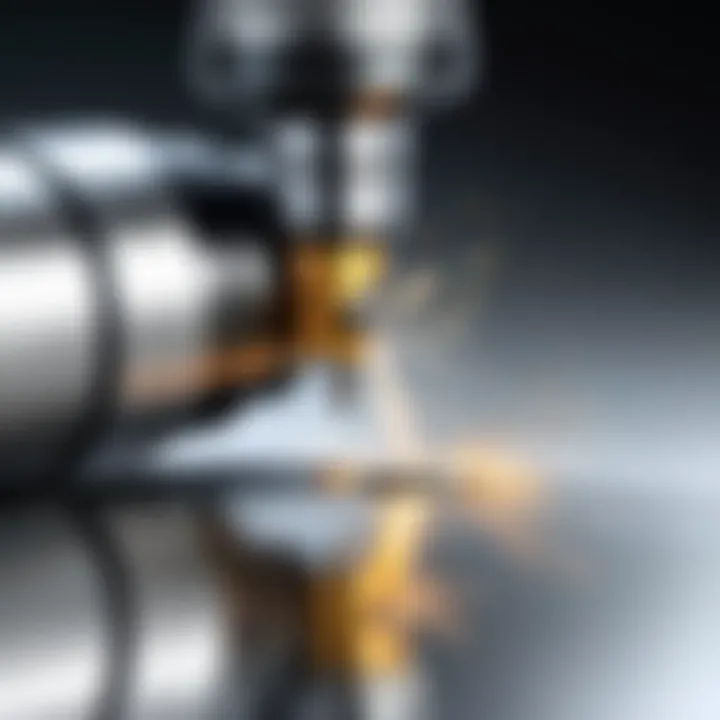
Warranty and Support Information
Look for products with solid warranty offerings and customer support, as this assures the longevity of your investment and provides peace of mind.
"Investing in high-quality cutting wheels can make the difference between a good project and a great one."
This guide aims to equip you with the necessary information to make informed decisions about small cutting wheels for drills. With the right tools in hand, thereâs no limit to what you can create!
Understanding Small Cutting Wheels
In the world of drilling, small cutting wheels are like the unsung heroes, quietly working their magic behind the scenes. These cutting tools are essential for achieving precision and efficiency in various applications. It's not just about making cuts; itâs about making the right cuts. Understanding small cutting wheels aids users in selecting the appropriate tools for specific tasks, optimizing performance, and enhancing the overall quality of work.
Definition and Purpose
Small cutting wheels, commonly mounted on drills, are circular blades designed to slice through materials with accuracy. They can be used for a range of tasks including carving, shaping, or trimming materials like metal, plastic, or wood. Their primary purpose is to deliver clean cuts while minimizing the risk of damage or excessive wear to both the wheel and the workpiece.
Material Construction
Types of abrasive materials
The abrasive materials used in small cutting wheels play a pivotal role in determining their effectiveness and durability. Materials such as aluminum oxide, silicon carbide, and diamond grit are popular selections. Aluminum oxide wheels, for instance, are favored for general purpose cutting due to their hardness and resistance to heat. Silicon carbide wheels, however, excel at slicing through non-metal materials because they provide a smoother finish. The key characteristic of these abrasive materials is their ability to wear down in a controlled manner, which is crucial for maintaining cutting efficiency.
A unique aspect of cutting wheels with diamond grit is their unparalleled hardness, allowing them to handle tough cutting jobs while retaining sharpness longer than their counterparts. However, diamond grit wheels can be pricier, which might deter some users who are budget-conscious. Itâs this blend of unique features that makes choosing the right type of abrasive material a critical task for anyone looking to accomplish intricate cutting jobs.
Metal and composite options
When it comes to the construction of small cutting wheels, metal and composite options have their own share of advantages. Metal cutting wheels tend to be more durable and provide a premium finish, especially when dealing with metals. Also, they are known for their strength and longevity, making them a favorite for industrial applications. On the flip side, metal wheels can be heavier, which can affect maneuverability.
Composite cutting wheels, on the other hand, strike a fine balance between weight and performance. These wheels typically combine various materials to offer a lightweight solution that doesn't compromise on capability. Their design allows for faster cuts without excessive force. The unique feature of composite materials is their flexibility, granting users a greater range of motion and adaptability during cutting tasks. Nevertheless, some composite options may wear out quicker under heavy use, which is a crucial trade-off to consider.
Selecting the right small cutting wheel significantly impacts performance and quality of the finished work.
Understanding these distinctions clarifies how the composition of a cutting wheel influences its performance across various applications. Whether approaching delicate electronic components or hefty construction materials, knowing the material composition helps users make informed choices that align best with their specific cutting needs.
Applications in Various Industries
The realm of small cutting wheels for drills extends far beyond mere utility; it embodies an essential tool that caters to diverse industry needs. With their precision engineering, these small wheels offer remarkable versatility. Whether you're outfitting your workshop or undertaking professional tasks, understanding the applications in various sectors is both enlightening and critical to achieving desired results.
Construction and Renovation
In the construction and renovation sectors, small cutting wheels prove indispensable. Workers often encounter a variety of materials, and the precision of these cutting wheels allows for efficient cutting without compromising structural integrity. For instance, when cutting tiles, a diamond-coated wheel can slice through with minimal chip-outs, preserving the visual appeal and functionality of the material. Additionally, these wheels can address tight spaces where larger equipment just cannot fit, making them a go-to choice for contractors and DIY enthusiasts alike. The ability to switch cutting wheels based on material type further enhances the efficiency of the job, ensuring adaptability across different project phases.
Metalworking
When it comes to metalworking, small cutting wheels play a pivotal role in various processes. They enable operators to craft intricate designs and maintain precision, essential factors in industries ranging from automotive to aerospace.
Types of cuts
The Types of cuts achievable with these wheels can significantly influence the outcome of a project. For example, straight cuts allow for clean, distinct separations along desired lines, helping to minimize material waste. Curved cuts, on the other hand, provide flexibility in design, ideal for artistic metal projects. With their keen edge, these small cutting wheels guarantee that every cut is precise, thus contributing substantially to overall production quality. Moreover, they are a favorite choice wherever tight tolerances are required, exemplifying why they remain popular in metal fabrication shops.
Finishing techniques
Moving to Finishing techniques, this aspect underscores the importance of achieving a refined surface after cutting. The right wheel can polish surfaces, removing burrs and providing a smooth touch. This is particularly valuable in metalworking, where aesthetics and functionality are paramount. Different materials may call for different finishing wheels; for instance, a flap disc might be chosen over a traditional cutting wheel for certain applications, enhancing versatility while ensuring that the end product meets quality expectations. In essence, fitting finishing techniques into workflows creates a synergy that not only augments performance but also safeguards the structural integrity of the materials treated.
Electronics and Precision Projects
In the ever-evolving electronics industry, small cutting wheels are instrumental in intricate applications. When crafting circuit boards or components that require exact dimensions, these tools deliver unmatched precision. The delicate nature of the materials involved forinstance, may range from fragile plastics to metal elements, requires a careful approach.
Utilizing small cutting wheels specifically designed for such projects can reduce the risk of damage, maximizing both yield and quality. The right selection here means selecting parameters like RPM ratings and arbor size alongside diameter and thicknessâall crucial for ensuring optimal functionality during assembly and production phases.
Specifications to Consider
When selecting small cutting wheels for drills, the specifications held by these tools play a crucial role. Each measurement can significantly alter performance, precision, and suitability for various tasks. Understanding specifications allows users to make informed choices, optimizing their projects' efficiency and quality.
Diameter and Thickness
Impact on cut depth
Diameter and thickness are pivotal when it comes to the depth of a cut. Generally speaking, a thicker wheel can execute deeper cuts, making it a popular choice for those working with denser materials. However, it comes with its own set of trade-offs. For instance, while thicker wheels may create deeper cuts, they also require more power from the drill, potentially leading to quicker wear.
The deeper cut capability allows for broader applications, such as cutting through layers of materials in construction. Yet, users need to be mindful of the balance between cut depth and the control needed during operations. A bigger diameter is beneficial for power tools, but might be cumbersome in tight spaces. Hence, the right measure can enhance overall performance while minimizing potential pitfalls.
Trade-offs between size and maneuverability
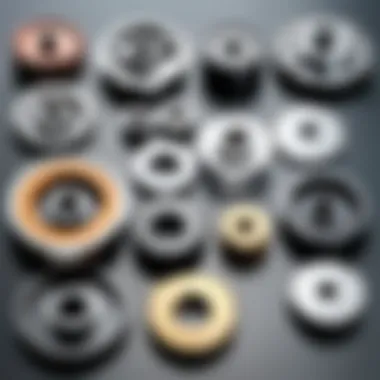
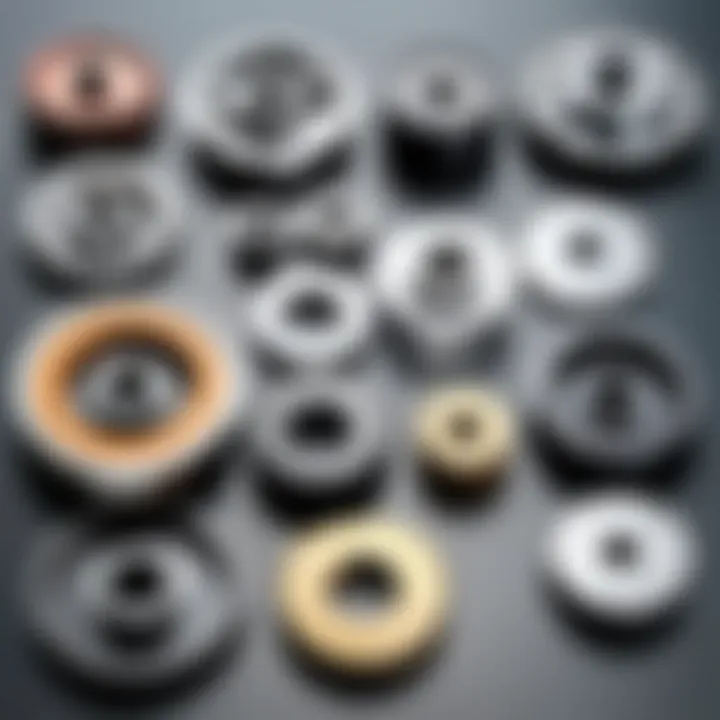
When opting for larger wheels, maneuverability often takes a hit. The flexibility to navigate tight corners or intricate designs typically diminishes as diameter increases. Conversely, smaller wheels allow for more precise work in confined spaces, a feature that's highly sought after in delicate projects like electronics assembly.
The key characteristic here is the adaptability based on the task. Opting for smaller wheels lets users get into more intricate areas but may compromise cutting depth. For a balanced approach, professionals frequently keep both sizes on hand, ensuring readiness for any challenge.
RPM Ratings
Matching drill capabilities
Understanding RPM (Revolutions Per Minute) is essential for getting the most out of small cutting wheels. Matching the RPM of the drill to that of the cutting wheel ensures effective operation without risking damage to either. A wheel with a higher RPM than the drill can lead to overheating, which is detrimental to material and performance.
It's beneficial because it enables users to maximize the efficiency of their tools. Ensuring that both the drill and cutting wheel are symbiotic in this regard can extend the life of both components.
Material compatibility
Different materials necessitate varied RPM ratings. Some materials, like softer metals, allow for higher speeds, while harder materials require slower, more controlled cuts. Knowing how to align material needs with the appropriate cutting wheel speed can make a world of difference in achieving clean cuts.
This consideration affects longevity and quality of work directly. Suitable RPM ensures that cuts are not only clean but that the cutting wheel lives a long life, minimizing costs over time.
Arbor Size
Importance for compatibility
The arbor size is another specification that cannot be ignored. Itâs essential that the wheel fits snugly on the drill for optimal performance. An incorrect size can lead to wobbling, which adversely affects precision and could lead to accidents. Wobbling can lead to incorrect cuts, waste of materials, and can even pose a safety hazard to the user.
This element emphasizes the need for careful assessment before purchase. A proper fit enhances efficiency and safety, ensuring that users can complete their projects with peace of mind.
Common sizes explained
Common arbor sizes usually range between 1/4 inch and 1/2 inch. Understanding the options and selecting a wheel that fits one's drill is part of the due diligence every user must undertake. If a user opts for a size that's too small or too big, they risk waste and potential mishaps.
Having detailed knowledge of which sizes match your equipment is vital. It allows users to maximize the use of their tools without compromising on safety or efficiency.
Choosing the Right Cutting Wheel
Selecting the right cutting wheel can make all the difference in achieving the desired outcome for your project. The perfect fit for your task hinges on a few critical factors, including the material youâll be working with and the finish youâre aiming for. This section will break down those elements to help you make an informed choice.
Assessing Project Needs
Material type
Understanding the type of material is paramount when choosing a cutting wheel. Different materials demand different approaches, from softer metals to hard composites. A cutting wheel designed for ceramic tiles may not fare well against steel, so it's essential to match the wheel to your specific workpiece.
For example, aluminum wheels are a favored choice for many due to their ability to cut efficiently while generating less heat, minimizing deterioration of the cutting edge. Using the wrong material can lead to friction, which not only affects the efficiency but could potentially damage the workpiece.
The key characteristic here is knowing that each material comes with its own unique challenges. Selecting a wheel that suits your material also ensures better control and less vibration, leading to cleaner cuts. The primary advantage of using a material-specific wheel is ultimately the performance and longevity it brings to your tasks.
Desired finish
The finish you desire on your project further narrows your options for cutting wheels. Are you looking for a rough cut that allows for further machining? Or perhaps a smoother finish that can be painted or polished right away? Different wheels provide varying levels of smoothness that can drastically change the final appearance of your project.
A wheel with finer grains, for instance, is typically more suited for finishing work. It creates less friction, allowing for delicate surfaces not to scratch or damage. Conversely, a coarser wheel facilitates quicker removal of material but may leave a rougher edge, necessitating additional finishing steps.
Ultimately, the relevant element in choosing the right cutting wheel lies in the balance between depth of cut and the quality of the finish that you want to achieve. Choosing the wrong finish type can result in time-consuming rework or surface issues down the line, costing you both effort and materials.
Evaluating Cost-Effectiveness
The cost of cutting wheels can vary widely. Itâs tempting to go for the cheapest option, but it often does not yield the best results.
Instead, consider the long-term implications. Investing in a high-quality cutting wheel may entail higher initial costs, but its durability usually equates to fewer replacements and better performance over time. Think of it as a penny wise, pound foolish situation; opting for a low-cost wheel may actually lead to higher expenses when factoring in replacement frequency and potential damage to your projects.
Several factors contribute to evaluating the cost-effectiveness of cutting wheels:
- Durability: A well-constructed wheel lasts longer.
- Versatility: Some wheels work with multiple materials, offering better value.
- Performance: Faster and more efficient cuts save time and labor costs.
User Recommendations
When working with small cutting wheels for drills, users must consider various important factors to ensure maximized performance and safety. Making informed choices can not only enhance the quality of your projects but also prolong the lifespan of your tools, turning any task from a chore into a straightforward process.
Safety Precautions
Proper gear
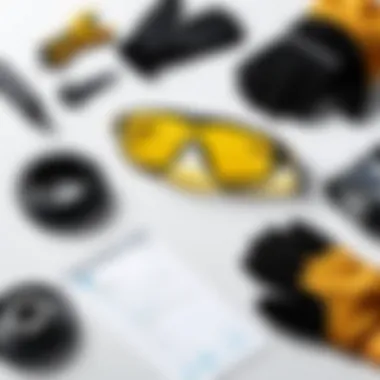
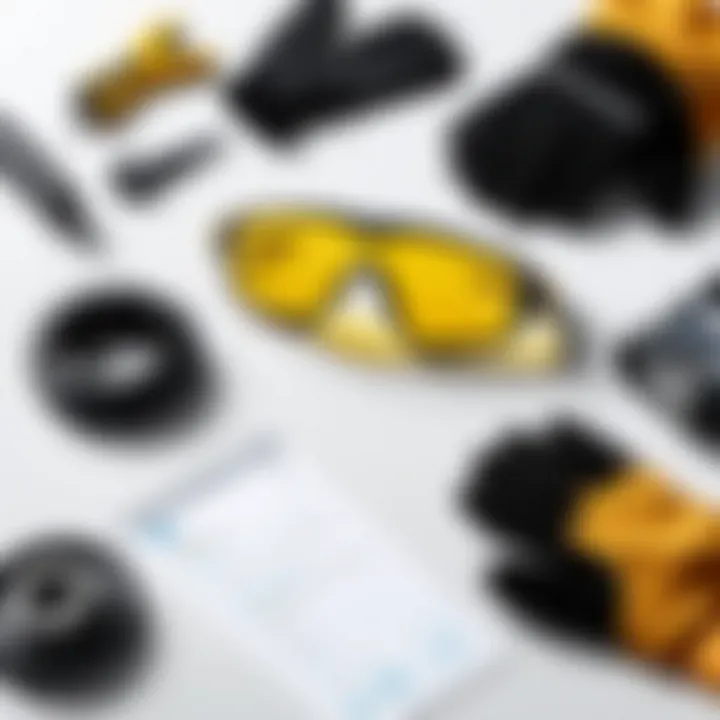
Using appropriate safety gear is non-negotiable when handling tools like cutting wheels. The significant aspect of proper gear revolves around injury prevention. Eye protection, for instance, is crucialâflying debris can unexpectedly strike the face if youâre not adequately protected.
One key characteristic of this gear is its ability to withstand impacts; you donât just want to wear glasses for the sake of it, but something that can genuinely guard against projectiles. Safety goggles that seal tightly around the eyes are thus seen as a beneficial choice. Their unique feature lies in their anti-fog lenses, which provide clear visibility during operations. While they may come with a price tag, their advantages far outweigh the costs; after all, a pair of well-made goggles can prevent serious eye injuries that could result in costly medical bills.
Workspace considerations
How your workspace is set up can make a world of difference in achieving effective results. Good workspace considerations help to create an environment where your focus is intact and distractions are minimal. One critical aspect is lighting; poor lighting can hinder precision and lead one to make careless errors.
The layout of tools and materials is another key characteristic worth noting. A well-organized work area allows for smooth transitions between tasks, reducing the time spent rummaging through clutter. Additionally, having a stable workbench decreases vibrations caused by the drill, which is conducive to accuracy. However, remember that clutter can sneak in silently. Keeping a tidy workspace is a habit worth cultivating to enhance both focus and expertise in drilling tasks.
Maintenance and Storage
Regular maintenance and proper storage significantly boost the longevity of cutting wheels and the drills they fit into. These considerations play a pivotal role, ensuring that users consistently achieve premium results without unexpected hiccups during projects.
Cleaning methods
Keeping your cutting wheels clean is not just about aesthetics; it is essential for optimal performance. Effective cleaning methods can prevent the build-up of debris that may hinder the wheel's functionality over time. An important aspect here is the use of a soft brush or compressed air to blow away dust and shavings gently.
This approach is beneficial because it does not wear down the wheel surface, unlike harsher methods that can lead to unnecessary damage. Regularly cleaning the wheels can thus enhance cutting efficiency and precision, allowing for better results on future tasks.
Optimal storage conditions
How and where you store your cutting wheels can greatly influence their effectiveness. Optimal storage conditions include keeping wheels in a dry environment, away from direct sunlight and moisture. Such factors can lead to deterioration of both the wheels and the materials they are made from.
One outstanding characteristic of proper storage rests in the ability to maintain the integrity of the wheelâs cutting surfaceâstoring them flat instead of stacked can mitigate warping. While setting up an organized storage space might seem labor-intensive, it ultimately pays offâproviding easy access to well-maintained cutting wheels allows for faster project completion and less frustration.
Proper recommendations not only enhance project effectiveness but also contribute to a safer and more productive workspace.
Common Mistakes to Avoid
In the realm of small cutting wheels for drills, avoiding common pitfalls can mean the difference between a successful project and a frustrating experience. Understanding what not to do is just as vital as knowing the right techniques. This section dives into those blunders that many may overlook. From miscalculating the speed settings to ignoring the condition of the cutting wheel, these mistakes can lead to poor performance and potential hazards.
Using Incorrect Speeds
One of the most frequent errors made by users is operating the cutting wheel at inappropriate speeds. Speed, as it relates to cutting wheels, isnât just a number; it plays a crucial role in ensuring smooth and precise cuts. When you use speeds that are either too high or too low, you risk damaging both the material being cut and the tool itself.
For instance, running the wheel too fast can cause excessive heat buildup, which in turn might lead to overheating and premature wear of the wheel. Conversely, too slow of a speed can result in a lack of efficiency in cutting, leading to frustration and wasted time. Therefore, matching the drill speed with the specifications recommended for the cutting wheel ensures longevity and performance optimally.
Neglecting Wheel Condition
Recognizing wear signs
The condition of the cutting wheel is paramount. Neglecting to inspect the wheel regularly can be like driving a car with bald tiresâdangerous and inefficient. Recognizing wear signs isnât just about visual inspections; it's about understanding the subtle cues that indicate a blade is nearing the end of its life. For example, if the wheel starts to show cracks or behaves unpredictably during use, those are signals that itâs time for a replacement. Regular checks not only ensure consistent cutting quality but also foster safety in your workspace, eliminating the risk of wheel failure during critical cutting tasks.
Impact on performance
Worn wheels can severely hinder performance. When a wheel has seen better days, it might not cut as effectively. A dull or damaged wheel requires more force to do its job, impacting the userâs experience significantly. This not only leads to inefficient work but can also result in inaccurate cuts and compromises on the finish of the material. Monitoring wheel condition ensures that the project progresses smoothly, allowing the user to focus on achieving their target results without unnecessary delays or complications.
The Future of Cutting Wheels
The future of cutting wheels looks promising, driven by innovation and evolving user demands. As industries continue to adapt to more complex materials and intricate designs, cutting wheels must keep pace. This section will explore advancements in material technology and how integrating smart technologies into these tools can transform drilling processes.
Advancements in Material Technology
In recent years, there's been a noticeable shift in the materials used to manufacture small cutting wheels. Traditional wheels, often made from less durable metals or simple composites, are now being complemented or entirely replaced by high-performance materials. These advancements aim to enhance durability and cutting efficiency.
New materials such as ceramic, diamond, and advanced resin composites offer several advantages. For example, ceramic wheels provide exceptionally high hardness and wear-resistance, resulting in longer lifespans without compromising performance. This means fewer replacements and, ultimately, cost savings for users.
Moreover, innovations in bonding agents and abrasives ensure that wheels can tackle various materials, from soft plastics to tough metals, with equal prowess. Aligning material technology with user needs shows a clear drive towards efficiency and precision in cutting tasks, key aspects highlighted throughout this article.
Integrating Smart Technologies
The integration of smart technologies into cutting wheels is a game changer. This move isn't just about sticking a computer chip on a wheel; it's about enhancing user experience and improving results through automation and data analytics.
Automation in tool usage
One of the faces of this integration is automation in tool usage. This functionality allows for real-time adjustments during the cutting process, helping maintain optimal cutting speeds and pressure. The key characteristic here is consistency; automated systems can prevent human error, which can lead to inconsistent cuts and compromised material integrity.
Automating the cutting process monitors conditions such as temperature and pressure, ensuring that the wheel operates within its ideal parameters. However, while this technology is promising, it does require a certain level of investment and familiarity, which could initially deter some users.ăsource: reddit.comă
"Automation transforms craftsmanship by ensuring uniformity and precision, but it may require users to adjust to new norms in their working methods."
Data-driven performance metrics
Another vital aspect is data-driven performance metrics. This can create a feedback loop where performance data from the cutting wheel is analyzed to suggest adjustments or improvements. The key characteristic of this approach is its ability to adaptâusers can learn how their wheels perform over time and tweak their practices accordingly.
Collecting performance data provides deep insights into wear patterns and operational efficiencies. Although it gives a big edge to savvy users, not everyone might be equipped to analyze such data or might find it overwhelming. The challenge lies in education and access; ensuring that all users can benefit from these advanced technologies.
As cutting wheels evolve, the need to embrace both material advancements and smart integrations becomes glaring. The careful balance between tradition and innovation is what positions the future of these tools on a robust path.