The Intricate Manufacturing Process of Door Closers
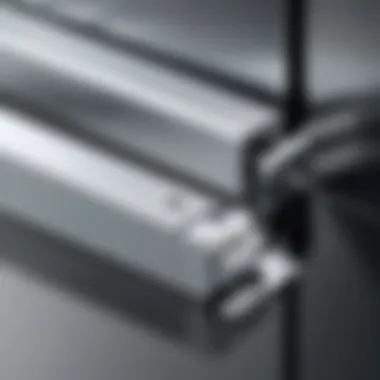
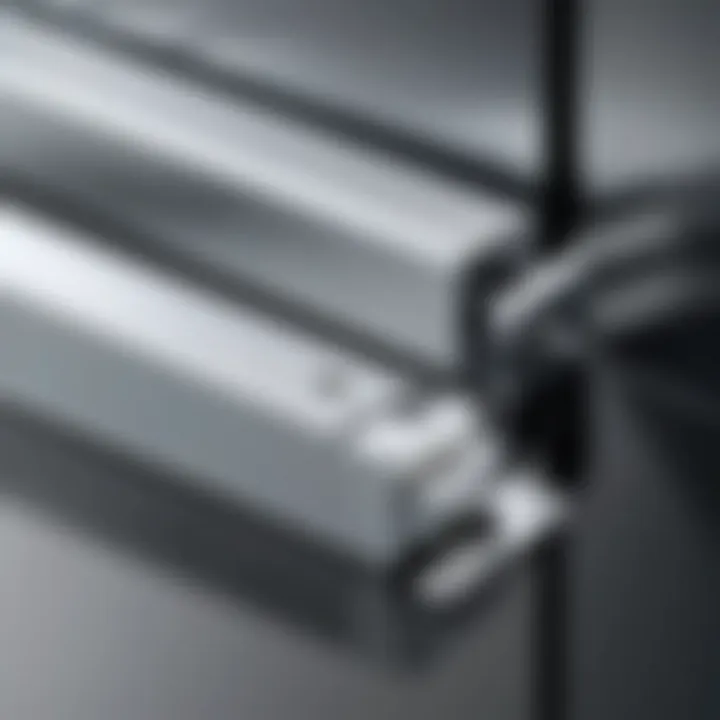
Intro
Understanding the intricacies of door closers is essential for manufacturers, engineers, and consumers alike. Door closers are pivotal components in maintaining safety and functionality in various environments. This article dives deep into their manufacturing process, elucidating every vital aspect, from materials to technological innovations.
Technical Specifications
Detailed Product Specs
Door closers come in various specifications tailored to meet different security and performance needs. Key specifications typically include weight capacity, which influences the size and strength of the spring mechanisms used. Common weight ratings can range from 150 pounds to over 300 pounds. Furthermore, models like the LCN 4041 offer adjustable closing speed and latching action, crucial for environments requiring controlled movement.
Performance Metrics
Performance metrics are critical for evaluating a door closer's effectiveness. Essential metrics include closing force, measured in pounds, and back-check strength, which prevents the door from being forced open too quickly. Measurements often follow the guidelines set by the American National Standards Institute (ANSI), ensuring compliance with safety and efficiency standards.
Compatibility Information
Compatibility ensures that a door closer functions properly within its designated frame. Most door closers are compatible with various door types, including wooden, metal, and fire-rated doors. It is essential to verify that the chosen model accommodates the weight and swing of the door to facilitate proper functionality.
Practical Applications
Use Cases for Different Users
Door closers serve diverse user needs across multiple sectors. In commercial settings, they maintain smooth operation for heavy traffic doors. In residential settings, closers provide convenience and security, especially for families with children. Specialized designs, like those found in healthcare facilities, enhance safety by ensuring that doors do not close too quickly.
Recommended Configurations
Configurations can differ based on usage requirements. For instance, a common configuration for high-traffic areas might include a delayed action feature, allowing users to pass through without obstruction. Alternatively, residential configurations may focus more on aesthetic integration, utilizing closer mechanisms that hide within the door structure.
Multi-Platform Performances
Multi-platform performance is increasingly becoming essential in design considerations. The integration of smart technologies allows for automatic adjustments based on traffic patterns and user engagement. Newer models can connect with home automation systems, enhancing user control.
Latest Trends
Industry Developments
The door closer manufacturing industry has seen advancements in technology, particularly with the rise of automated systems. Noteworthy developments include the introduction of sensors that modify closing speeds based on environmental conditions or user proximity.
Emerging Technologies
Emerging technologies focus on enhancing safety and functionality. New materials, such as advanced composites, are now employed to increase durability while minimizing weight. These innovations reduce wear and prolong the lifespan of the product.
Future Predictions
As technology advances, future predictions indicate an increase in the integration of IoT capabilities in door closers. Manufacturers may develop systems that offer real-time data on door usage and operational efficiency, thus streamlining maintenance schedules and interventions.
Buying Guides
Recommended Products
When selecting a door closer, models like the Norton 1601 and the Schlage BE365 are often highlighted for their reliability and performance in various settings. Each model caters to specific needs, ensuring diverse options for consumers.
Purchasing Tips
To optimize your purchasing decision, consider factors such as warranty duration, support options, and installation techniques. Ensuring compatibility with the door type is paramount for effective use.
Warranty and Support Information
Most reputable brands offer warranties ranging from one to five years. Good support and service can be critical when installing or troubleshooting door closers.
Prelims to Door Closers
Definition and Purpose
A door closer is a mechanical device that automatically closes a door after it has been opened. Its core purpose is to facilitate the seamless closing of doors, making it essential for various environments, from commercial buildings to residential areas. Beyond just closure, door closers also contribute to safety by reducing the risk of accidents related to door slamming. In environments where fire safety is a concern, these devices can help in adhering to safety regulations by ensuring fire doors close properly.
Historical Background
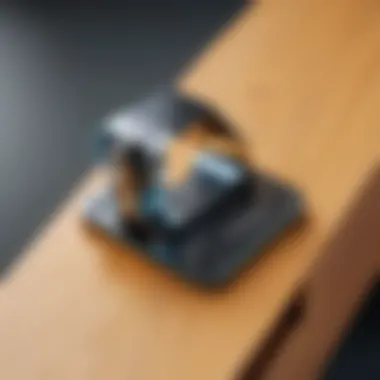
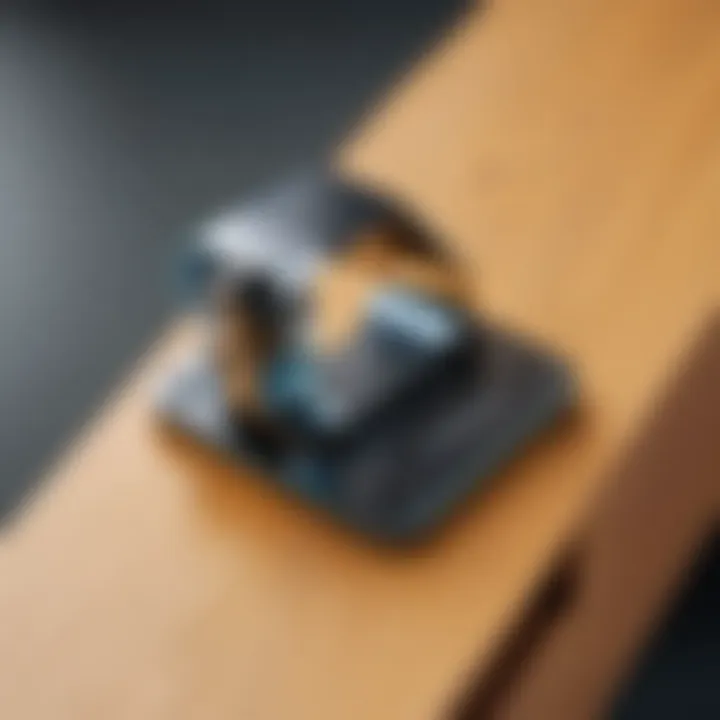
The concept of door closers has been around for centuries, evolving significantly over time. Historical records indicate that simple devices for closing doors were used in ancient civilizations. However, the modern door closer as we know it started to take shape in the 19th century with the advent of springs and hydraulic systems. This evolution was driven by a growing need for more effective solutions in both residential and commercial settings. Over time, advancements in materials and manufacturing technology have led to the development of more efficient and reliable door closers, each catering to different requirements of functionality and design.
"Understanding the historical context of door closers is crucial for recognizing the innovations that enhance their performance today."
The growing complexity in building designs and the need for energy efficiency have further propelled innovations in the door closer industry, shaping the devices to be not only functional but also aesthetically pleasing.
Overview of the Manufacturing Process
The manufacturing process comprises numerous interrelated stages, each essential in achieving the desired quality and performance. From selecting appropriate materials to implementing advanced technologies, every element plays a role in creating door closers that meet industry standards. A well-structured manufacturing process minimizes errors, optimizes resource usage, and enhances product durability.
Moreover, comprehending this process allows manufacturers and consumers to appreciate the complexity behind these essential tools. It underscores the importance of innovation and adaptability in meeting current market demands and future industry trends.
Key Stages of Production
The production of door closers involves multiple stages, including:
- Design: Engineers develop designs that balance aesthetics, functionality, and performance.
- Material Selection: Choosing the right materials is vital for durability and effectiveness.
- Manufacturing Techniques: Different methods are used to fabricate components, impacting the final product's quality.
- Assembly: Components are assembled to form a complete unit, ensuring all parts work harmoniously.
- Quality Control: This step includes testing and inspections to guarantee reliable performance.
Each of these stages requires careful planning and execution to ensure the end product meets customer expectations.
Materials Used
The choice of materials is fundamental in the manufacturing process, impacting both the function and longevity of door closers.
Metals
Metals, such as steel and aluminum, are commonly used for their strength and durability. These materials can withstand significant wear and stress, making them essential for high-traffic areas. For instance, the high tensile strength of steel makes it a popular choice because it offers robust support and resists deformities over time. However, metals can be susceptible to corrosion if not properly treated, necessitating protective coatings.
Plastics
Plastics, like polycarbonate and nylon, bring flexibility and lightweight advantages. These materials allow for innovative designs and cost-effective manufacturing processes. The key characteristic of plastics is their resistance to impact and varying weather conditions, making them suitable for external door applications. Nevertheless, plastics may not support heavy loads as effectively as metals do, which limits their usage in some environments.
Rubber
Rubber is an essential material often used in the seals and cushioning components of door closers. Its primary advantage lies in its ability to absorb shock and reduce noise during door operation. The elasticity of rubber ensures a tight seal, preventing air infiltration. Yet, rubber can degrade over time when exposed to certain environmental conditions, which may require periodic replacement to maintain performance standards.
Design Considerations
Design considerations play a pivotal role in the production of door closers. These elements are not merely aesthetic; they fundamentally influence the functionality and user experience of the product. Ensuring that a door closer operates effectively while maintaining an appealing look is critical for manufacturers and consumers.
Functionality
When it comes to door closers, functionality is paramount. The essential task of a door closer is to control the closing of the door smoothly and securely. There are several factors manufacturers take into account to ensure optimal performance:
- Durability: The materials used must withstand wear and tear. Components like springs and hydraulic fluids should be engineered for longevity to avoid frequent replacements. The integration of high-quality materials contributes to the lifecycle and reliability of the door closer.
- Testing and Compliance: Manufacturers must adhere to established industry standards to guarantee function. Rigorous testing protocols help identify potential issues during the design phase, thus enhancing the final product.
Understanding these aspects helps manufacturers focus on producing door closers that meet customer needs in everyday situations.
Aesthetics and Ergonomics
Aesthetics and ergonomics are critical when designing door closers. In contemporary architecture, a product's visual appeal can significantly influence its acceptance.
- Visual Integration: The design should complement the architecture of the building. A door closer must be visually subdued while still serving its purpose. Finish options, shapes, and sizes need to cater to diverse architectural styles.
- User Interaction: The design must facilitate effortless operation. Door closers that resist easy handling can frustrate users, causing inconvenience or even potential injuries. Manufacturers need to focus on how the user interacts with the door and its closer to create a seamless experience.
- Accessibility: Including features that enhance accessibility ensures that door closers meet a wider range of user needs. This consideration is especially important in public spaces where diverse populations use the facilities. Enhancing inclusivity aligns with modern design principles.
Types of Door Closers
Understanding the different types of door closers is crucial in the manufacturing process. Each type serves distinct functions and offers specific advantages tailored to varying environments and user needs. Proper selection can enhance building accessibility, ensure safety, and improve aesthetic appeal.
Surface-Mounted Closers
Surface-mounted closers are the most common type found in commercial and residential buildings. They are mounted on the door's surface and are generally easy to install. One of the primary benefits of surface-mounted closers is their visibility, which allows for straightforward maintenance and easy adjustments.
These closers can be used on standard doors as well as on higher traffic doors, making them versatile. They come in various styles, ranging from basic models to more sophisticated designs that integrate automatic hold-open features. The ability to adjust the closing speed and latching action is essential for controlling door behavior and ensuring safety.
Concealed Closers
Concealed closers, on the other hand, are embedded within the door or the frame, offering a clean and sleek look. Their hidden design makes them favorable for aesthetic purposes, especially in modern architecture. Despite being less visible, these closers provide similar functionality to surface-mounted options but with a more polished appearance.
However, installation can be more complex, which might increase overall costs. They are particularly beneficial in environments where door operation should not dominate the visual design, such as in luxury hotels or sophisticated offices. Their concealed nature also protects them from casual damage or tampering, providing added durability.
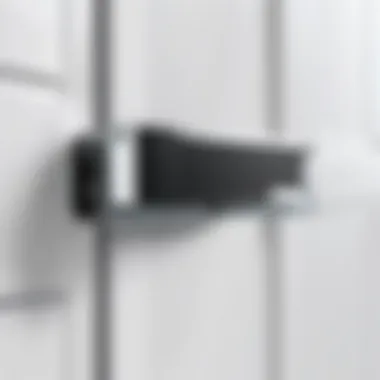
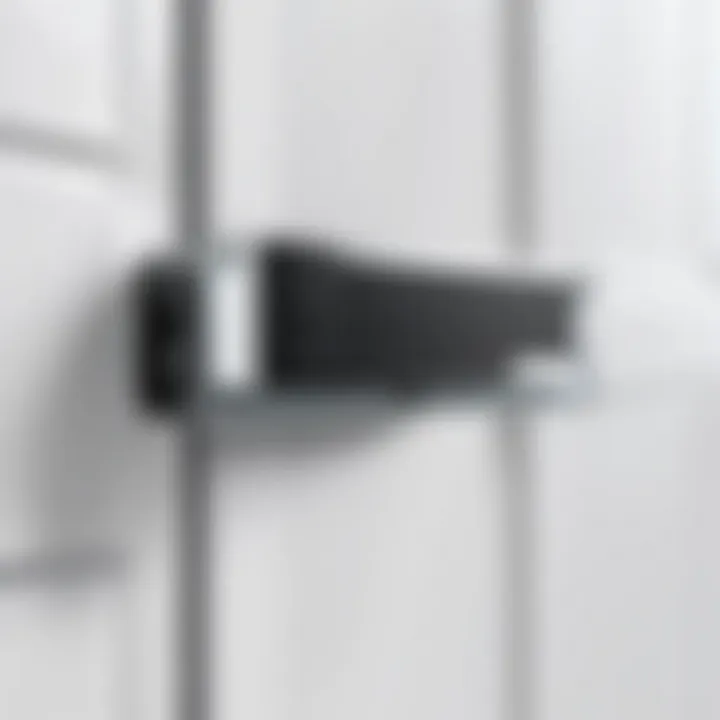
Rack and Pinion vs.
Hydraulic
When discussing the mechanisms of door closers, two prominent types emerge: rack and pinion and hydraulic. Rack and pinion closers utilize a gear system to control the door's movement. They are known for their speed and efficiency, making them suitable for high-use areas. Their design allows for precise control over closing speed, ensuring that the door operates smoothly without excessive force, reducing wear on hinges and frames.
Hydraulic door closers use fluid to control the motion of the door. This type provides a more cushioned closing action, ideal for environments that require quieter operation. They are particularly valued in settings such as hospitals or schools where noise reduction is a priority. Hydraulic systems often include adjustable settings to customize the closing speed and force based on the door's size and usage.
Both types have their unique advantages and are chosen based on specific operational requirements and performance criteria. The knowledge of these different types is vital for manufacturers, as it enables them to meet the diverse needs of consumers and ensure optimal functionality in various settings.
Industry Standards and Certifications
These standards help streamline the production process. They provide a framework that manufacturers can follow, ensuring consistency and adherence to best practices. This results in door closers that function efficiently and meet customer expectations.
Moreover, certifications from recognized organizations can enhance a manufacturer's reputation. When a product is certified, it indicates to consumers that the item has undergone rigorous testing and meets industry benchmarks. This assurance can influence purchasing decisions, particularly in competitive markets.
Quality Assurance Protocols
Quality assurance protocols are integral to maintaining high standards in the production of door closers. Manufacturers employ various methods to verify that each component meets specific requirements. This can include rigorous testing of materials, inspection of finished products, and continuous monitoring throughout the production process.
Key elements of quality assurance may include:
- Material Testing: Assessing raw materials for durability and strength.
- Dimensional Inspections: Confirming that parts conform to specified measurements.
- Functional Tests: Evaluating the operational performance of door closers under various scenarios.
Such protocols not only ensure that the product meets predefined standards, but they also pave the way for continual improvement. This continual cycle leads to higher quality products and increased consumer satisfaction.
Compliance with Regulations
Compliance with regulations is a vital aspect of the door closer manufacturing process. Manufacturers must navigate a myriad of national and international standards, like the American National Standards Institute (ANSI) and the International Organization for Standardization (ISO). These organizations set rules that cover various facets of manufacturing, from safety to environmental considerations.
Adhering to these regulations ensures that products are safe for consumer use and reduces the risk of liability. Additionally, compliance can facilitate market access. Many regions require products to meet specific regulatory standards before they can be sold. Without compliance, manufacturers would find it difficult to compete in global markets.
To achieve compliance, companies often need to invest in:
- Training: Educating employees about regulatory requirements and best practices.
- Documentation: Keeping clear records of processes and tests conducted.
- Periodic Reviews: Regularly evaluating and adjusting processes to align with changing regulations.
Ultimately, strict adherence to industry standards and certifications not only enhances product quality but also fosters trust between manufacturers and consumers.
Quality Control in Manufacturing
Quality control plays a critical role in the manufacturing of door closers. This process ensures that each unit meets specific standards regarding functionality, safety, and durability. Manufacturers implement quality control measures to maintain consistency and minimize defects. Without rigorous control, the end product can suffer in performance and reliability, leading to potential safety hazards.
The quality control approach often comprises several stages, including raw material inspection, in-process checks, and final product testing. Each of these stages serves to catch any issues early in the process, addressing them before they escalate into larger problems.
Testing Procedures
Testing procedures in door closer manufacturing are essential for confirming that products perform as expected. Manufacturers typically conduct a range of tests to evaluate different aspects of a door closer's performance. Some critical testing methods include:
- Functional Testing: This involves simulating the actual use of the door closer. It assesses how well the closer operates under various conditions, ensuring it meets required standards for speed and force.
- Durability Testing: This test checks how well the door closer withstands repeated use over time. Manufacturers often use machines to cycle the closer open and closed, replicating years of use in a short period.
- Environmental Testing: This evaluates how external factors, such as extreme temperatures, humidity, or exposure to corrosive environments, affect the performance of the door closer. Manufacturers must ensure that all units can maintain functionality under diverse conditions.
Utilizing these testing procedures provides manufacturers confidence in their products and reassurance to consumers regarding safety and reliability.
Continuous Improvement Methods
Continuous improvement methods are integral to maintaining high-quality standards in door closer manufacturing. These methods focus on regularly evaluating processes and products to identify areas for enhancement. Some common strategies include:
- Feedback Loops: Manufacturers actively use customer feedback and performance data to identify potential improvements in design or production processes.
- Lean Manufacturing: This approach emphasizes minimizing waste and enhancing efficiency in production, which often leads to improved quality. Focusing on value-added activities allows manufacturers to produce higher-quality products at reduced costs.
- Six Sigma Methodology: By employing statistical analysis, manufacturers can pinpoint defects and variability in their manufacturing processes. The goal is to achieve near-perfect quality and reduce the number of defective products reaching customers.
Implementing continuous improvement methods fosters a culture of excellence and innovation, which not only benefits the company but also enhances the overall quality of door closers available in the market.
โQuality is never an accident; it is always the result of intelligent effort.โ
The Role of Technology in Manufacturing
Automation and Robotics
Automation plays a pivotal role in modern manufacturing processes. It reduces human intervention in repetitive tasks, which not only increases production speed but also minimizes errors. Robotics is a key element of automation, providing support in various stages of door closer production. These robotic systems can handle delicate parts with precision, assemble components, and conduct quality checks.
- Consistency: Robots perform tasks with unwavering accuracy, which ensures that every door closer meets the required specifications.
- Efficiency: Automated systems can operate continuously, maximizing output while reducing labor costs.
- Safety: By taking over hazardous tasks, robots contribute to a safer work environment for human workers.
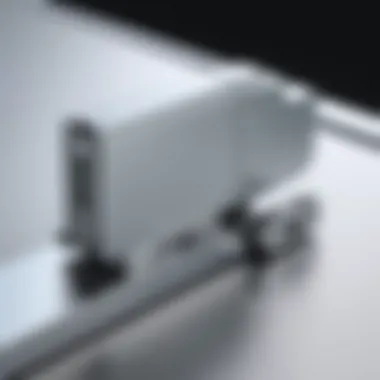
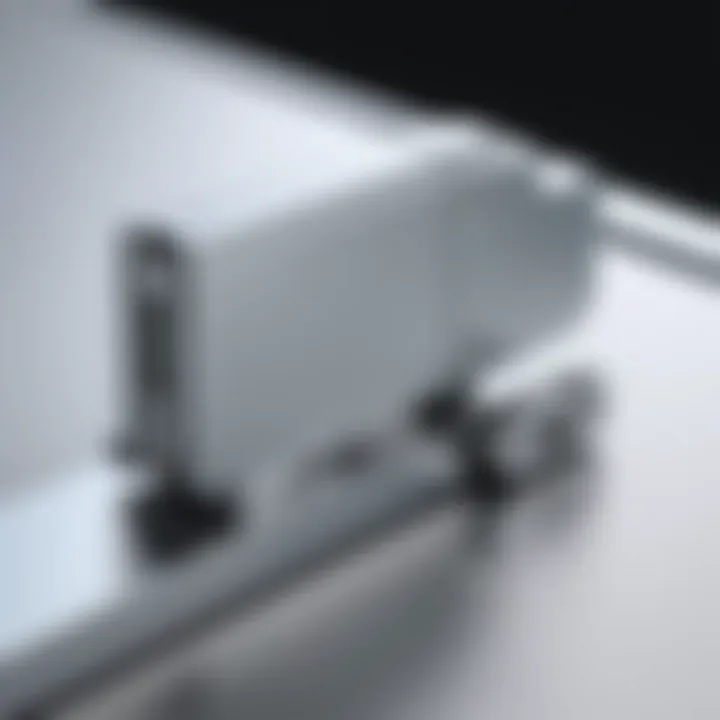
Furthermore, automation allows for real-time monitoring of the manufacturing process. This ensures timely adjustments can be made, leading to reduced waste and better resource management.
CAD/CAM Systems
Computer-Aided Design (CAD) and Computer-Aided Manufacturing (CAM) systems are integral to the design and production of door closers. CAD software enables engineers to create precise drawings and models of door closer components. This digital approach eliminates common errors associated with manual drafting.
CAM systems then take these designs and convert them into commands for manufacturing equipment. This means:
- Enhanced Design Flexibility: Designers can easily modify models to optimize functionality or adapt to new trends.
- Greater Precision: Automated machining processes facilitate the accurate cutting and shaping of materials.
- Streamlined Production: Integrating CAD and CAM reduces the lead time from design to production.
The collaborative use of CAD and CAM makes it possible to explore more complex designs while maintaining high standards of quality. The end result is a product that not only meets customer expectations but also incorporates the latest advancements in technology.
Technology's importance in the manufacturing of door closers cannot be understated. It shapes the industry through automation, precision, and efficiency.
Environmental Considerations
Environmental considerations play a crucial role in the manufacturing of door closers. This topic emphasizes the ecological impact of production processes, material choices, and overall sustainability. Manufacturers are increasingly aware of their responsibilities toward the environment, driving them to adopt more sustainable practices.
Sustainable Materials
The use of sustainable materials in door closer manufacturing is a significant element of reducing environmental harm. Manufacturers are opting for materials that not only meet functional requirements but also minimize negative impacts on the environment.
Some examples include:
- Recycled metals: Utilizing metals that have been recycled decreases the demand for new raw materials, thus reducing the energy consumption and emissions associated with extraction and processing.
- Bio-based plastics: These alternatives to traditional petroleum-based plastics are made from renewable resources. They help decrease dependency on fossil fuels and reduce overall carbon footprints.
- Natural rubber: Sourced from sustainable plantations, natural rubber can replace synthetic options while having a less detrimental effect on the environment.
Investing in such materials not only aligns with global sustainability goals but also appeals to consumers who prioritize eco-friendly options when selecting products.
Waste Management Practices
Effective waste management is vital in the production of door closers. Implementing proper practices ensures that waste is minimized and processed efficiently.
Important strategies include:
- Recycling: Manufacturers should have robust recycling programs that take back scrap metal, plastics, and other materials used during production.
- Reduction: Streamlining production processes to reduce excess waste is essential. This can involve optimizing material cutting methods to minimize leftover materials.
- Treatment of hazardous waste: Any hazardous materials used in the production process must be disposed of responsibly. Following local and international regulations helps prevent environmental contamination.
- Education and training: Staff should receive training on waste reduction techniques and the importance of compliance with environmental policies.
Adopting these waste management practices not only supports compliance with regulations but also enhances the overall productivity and efficiency of manufacturing. By focusing on both sustainable materials and effective waste management, manufacturers can significantly improve their environmental impact and contribute to a more sustainable future for their industry.
Future Directions in Door Closer Manufacturing
Understanding the future directions in door closer manufacturing is essential for stakeholders in the industry. This section emphasizes the transformative impact of advancing technology and evolving market needs. Manufacturers must adapt to changes to remain competitive and meet customer expectations. The incorporation of smart technology, sustainable practices, and innovative designs will shape this sectorโs landscape.
Emerging Technologies
- Smart Sensors: Enable automatic adjustment for varied traffic, optimizing the door's function.
- Connectivity: IoT-enabled door closers facilitate integration with security systems.
- Data Analytics: Provides insights into usage patterns, enabling manufacturers to improve design and performance.
The adaptation of these technologies not only enhances user experience but also supports manufacturers in creating more efficient production methods.
Market Trends
The trend in the door closer market shows a clear shift towards eco-friendliness and efficiency. Consumers increasingly prefer products that are sustainable and do not compromise performance. Several factors are driving these trends:
- Sustainable Materials: Increasing demand for products made from recycled and biodegradable materials.
- Energy Efficiency: Enhanced designs that reduce energy consumption in functionality.
- Customization: Greater emphasis on tailored designs to meet specific architectural needs.
This shift towards sustainability reflects broader societal values, requiring manufacturers to innovate continuously. As these trends evolve, companies must align their strategies with what consumers seek.
The combination of emerging technologies and market trends is reshaping the future of door closer manufacturing, pushing boundaries to meet evolving consumer expectations and environmental responsibilities.
Ending
For manufacturers, carrying the knowledge from this exploration helps them in refining their production techniques. Enhanced quality assurance protocols can lead to superior products, increasing consumer trust. Moreover, awareness of emerging technologies and market trends can direct businesses toward innovation, which is vital in todayโs competitive landscape.
Summary of Findings
- A range of materials used, mainly metals, plastics, and rubber.
- Various types of door closers, each with distinct functional features.
- Stringent quality control protocols that ensure compliance with industry standards.
- The role of technology, including automation and CAD systems, in improving production efficiency.
- Environmental considerations that affect the sourcing and disposal of manufacturing materials.
These findings emphasize the need for continuous improvement and adaptation in manufacturing practices, particularly regarding sustainability and technological advancements.
Recommendations for Manufacturers
To enhance the manufacturing of door closers, it is advisable for manufacturers to:
- Invest in automation and robotics to boost efficiency and precision in production.
- Prioritize research and development to stay ahead of market trends and consumer preferences.
- Implement sustainable practices by using eco-friendly materials and waste management methods.
- Regularly update quality control protocols to address new challenges as they arise.
- Foster industry collaborations to share insights and innovations that can lead to better products.
By adopting these recommendations, manufacturers can improve product reliability and meet the growing demands of tech-savvy consumers effectively.