Exploring Taulman Nylon 645: Properties and Applications

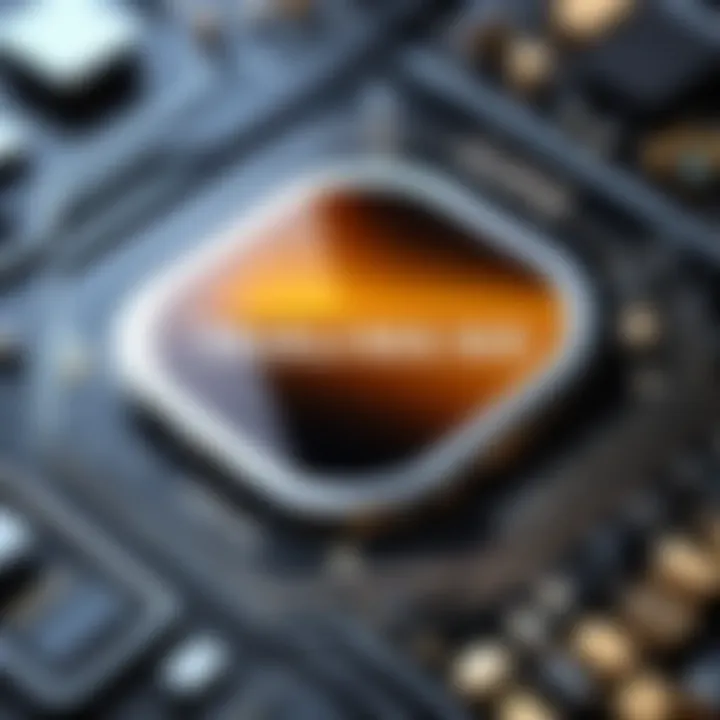
Intro
In the world of 3D printing, materials drive innovation, allowing creators to realize intricate designs with just a few clicks. Among these materials, Taulman Nylon 645 stands out. This type of nylon has been gaining traction due to its unique properties, which make it particularly suited for a variety of applications. With a balance of strength, flexibility, and lightweight nature, Taulman Nylon 645 is evolving into a top choice for enthusiasts and professionals alike.
The purpose of this exploration is to furnish readers with a comprehensive understanding of Taulman Nylon 645. As we embark on this journey, we will dissect its technical specifications, practical applications, latest trends, purchasing tips, and maybe even uncover some common pitfalls that users might face. The myriad advantages this material offers may very well change how you approach your next 3D printing project. So, fasten your seatbelts, and let's dive into the nuts and bolts of this fascinating filament.
Preamble to Taulman Nylon
In the ever-evolving world of 3D printing, material selection is pivotal in determining both the functionality and quality of the final product. One of the standout options is Taulman Nylon 645, a material that has gained traction among enthusiasts and professionals alike. This section will illuminate the essence of Taulman Nylon 645, highlighting its unique characteristics and the myriad benefits it brings to the table.
Understanding Nylon in 3D Printing
Nylon is a type of polyamide that has carved out a niche for itself in the 3D printing landscape. It's well-regarded for its strength, flexibility, and resilience, making it ideal for applications that require durability. The significance of nylon in 3D printing boils down to its impressive mechanical properties that rival those of traditional materials like metals and composites.
When it comes to Taulman Nylon 645, it's a formulated blend that takes these fundamental properties up a notch. This specific variation is designed to retain the favorable traits of nylon while addressing common concerns such as ease of printing and material integrity. Users can expect robust results, with a level of accuracy that is crucial for both prototyping and functional pieces.
The adaptability of nylon to various printing methods—including FDM (Fused Deposition Modeling)—combined with its ability to bond well with itself, showcases its versatility. Thus, understanding the role of nylon in this manufacturing process helps in appreciating why Taulman Nylon 645 is frequently chosen for complex projects.
Consider the following points:
- Versatile Applications: Due to its excellent mechanical strength, it's suitable for everything from intricate prototypes to mechanical parts.
- User-Friendly: The formulation of Taulman Nylon 645 makes it approachable for seasoned makers and novices alike, offering a manageable printing experience.
- Environmentally Conscious: As more users become aware of sustainable practices, nylon presents a viable option due to its potential for recycling.
Overview of Taulman Materials
Taulman 3D has established itself as a noteworthy player in the field of 3D printing materials. Known for pushing the envelope, they offer a range of specialty filaments that appeal to a diverse audience. Each filament variant is crafted with specific properties that cater to various needs, often leading to a higher quality of printed objects.
Taulman Nylon 645 stands out, notably for its tailored qualities intended to enhance the printing process. This particular filament offers:
- Higher clarity: Enhances the overall aesthetic of the print.
- Low warpage: Reduces the risk of print failures, granting peace of mind.
- Significant strength: Ensures that finished products withstand the test of time and usage.
Together with proper settings and techniques, utilizing Taulman Nylon 645 can transform the way users approach their 3D printing projects. With offerings like this, Taulman enables makers to explore the boundaries of creativity, ensuring each creation is not just functional but also an expression of craftsmanship.
Taulman Nylon 645 provides a robust solution for both hobbyists and professionals, uniting quality and ease of use in one remarkable filament.
Chemical Composition of Taulman Nylon
Understanding the chemical composition of Taulman Nylon 645 is fundamental for users ranging from enthusiastic hobbyists to seasoned professionals. The material's distinct properties stem from its unique blend of polymer structure and the careful choice of modifiers and additives. This section explores not just the ingredients of this material, but also why these characteristics matter in practical applications. Knowing what makes up Taulman Nylon 645 helps in understanding its behavior during printing and its performance in end-use products.
Polymer Structure
At the heart of Taulman Nylon 645 lies its polymer structure, a complex interplay of interconnected molecular chains. Specifically, Taulman Nylon 645 is a type of nylon known as polyamide 645. This polymer is recognized for its high tensile strength, but what truly sets it apart is its high crystallinity. This translates into superb mechanical properties that can endure considerable stress before yielding.
The polymer chains in Taulman Nylon 645 are longer compared to some other nylons, contributing to its greater flexibility and durability. When these long chains interlink effectively, they create a material that resists deformation, meaning it can spring back from minor bends or impacts.
Moreover, its chemical composition allows for good resistance to various chemicals, which is important in functional applications where parts may come in contact with oils, fuels, or even solvents while in use.
Additives and Modifiers
While the polymer structure is crucial, the additives and modifiers used in Taulman Nylon 645 enhance its characteristics even further. These substances can include impact modifiers, plasticizers, and even colorants, each contributing to a more tailored performance of the filament.
- Impact modifiers improve resistance to shock, ensuring the parts created can withstand sudden forces without breaking.
- Plasticizers lower the material’s viscosity and improve flow during the printing process, making it easier to work with for both beginner and expert printers.
- Colorants are often included not just for aesthetic purposes but also to influence the overall thermal stability and processing characteristics of the nylon.
A notable additive in Taulman Nylon 645 is its special formulation that minimizes moisture absorbance, addressing a common issue in other nylon variants. This particular aspect is essential because high moisture levels can severely affect both the physical properties and the printability of nylon filaments.
In summary, the careful selection of both the polymer structure and the additives/modifiers allows Taulman Nylon 645 to achieve a balance of strength, flexibility, and ease of use that appeals to a wide array of users. Understanding these elements is key when considering this material for different 3D printing projects, supporting informed choices that lead to successful outcomes.
Mechanical Properties of Taulman Nylon
This section digs into the mechanical properties of Taulman Nylon 645, a critical factor that influences its performance in various applications. Understanding these properties not only aids in material selection but also provides insights into the usage contexts that play well with this specific nylon variant. Key elements like strength, durability, flexibility, and impact resistance will be dissected here, each contributing in their own way to the material's overall utility.
Strength and Durability
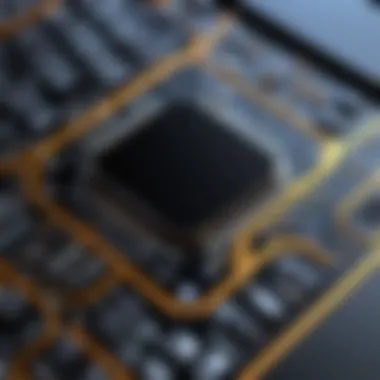
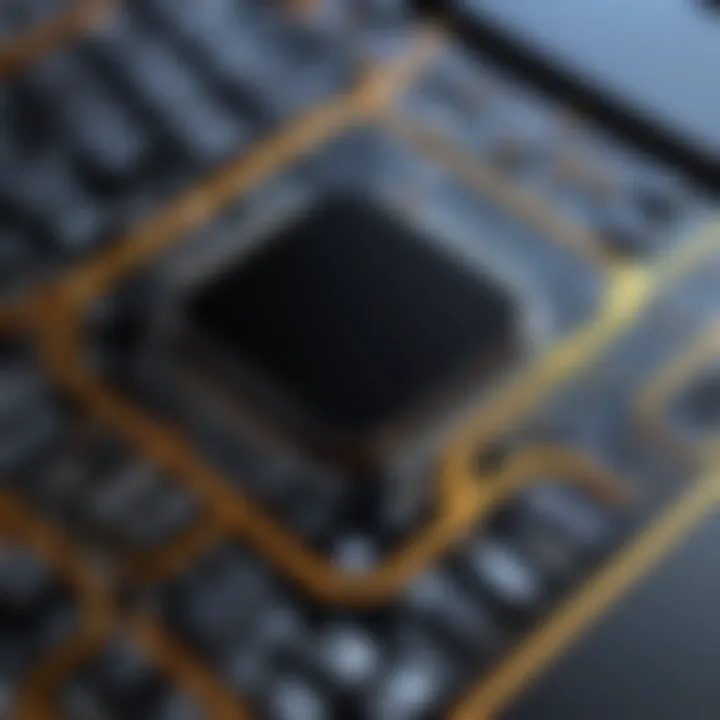
When discussing Taulman Nylon 645, one cannot overlook its impressive strength and durability. This nylon offers a tensile strength of about 5,000 psi, making it a solid choice for parts that require a robust structure. It shines in functional prototypes and end-use applications where reliability is non-negotiable. For example, consider a drone frame or specialized gears; using Taulman Nylon 645 ensures they withstand real-world stresses without cracking or deforming.
A crucial aspect of durability also involves resistance to wear and tear. The material's ability to endure repetitive stress means that components made from it have a longer lifespan. In this sense, Taulman Nylon 645 can often emerge as a cost-effective solution, where less frequent replacements lead to savings over time, especially in production lines where downtime can be detrimental.
"Using Taulman Nylon 645 allows engineers to create components that can handle significant loads with minimal risk of failure, an aspect vital in high-stakes applications."
Additionally, the material's thermal properties play a role in its durability. It performs adequately under varying temperatures, with specific attention to how it retains its structural integrity even under heat. Thus, those employed in industries that encounter thermal variations may find Taulman Nylon 645 particularly appealing.
Flexibility and Resilience
Flexibility is another remarkable attribute of Taulman Nylon 645. Despite its strength, it boasts a degree of bendability that allows for application in dynamic environments. If you’re crafting parts that interact with moving components, this flexibility can be a game-changer. A classic example might be hinges or connectors where rigid materials could lead to fracture or failure.
The resilience of Taulman Nylon 645 means that it can be subjected to various forces without permanent deformation. Whether it's compressive or tensile forces, this nylon variant absorbs shocks well, making it a candidate for items subjected to vibrations or impacts, like automotive parts or even gadgets that see a bit of rough handling.
Moreover, its flexibility also allows it to accommodate design iterations. If you're in prototyping, adjustments can be made with relative ease, avoiding the headaches of brittle materials that snap under pressure. This balance of strength and give creates an overall ergonomic solution in design.
Impact Resistance
When it comes to impact resistance, Taulman Nylon 645 shines with its ability to absorb shocks effectively. Unlike many other materials, it doesn't shatter upon impact, making it suitable for applications prone to blows or jolts. For instance, consider its potential use in protective gear or casings that protect sensitive electronics. Its pliability absorbs energy from impacts, which can save inner components from damage.
To put it simply, if a product is likely to see heavy usage, impact resistance can’t be an afterthought, and that’s where Taulman Nylon 645 excels. Whether in consumer goods or industrial machines, this property contributes significantly to safeguarding both integrity and functionality over the product's lifespan.
In summary, the mechanical properties of Taulman Nylon 645—its strength, flexibility, and impact resistance—position it as a valuable choice in 3D printing. Understanding these traits helps designers and engineers make informed decisions, ensuring that the chosen materials can meet their end-use requirements effectively.
Thermal Characteristics of Taulman Nylon
Understanding the thermal characteristics of Taulman Nylon 645 is essential for anyone considering its application in 3D printing. The material's performance is significantly influenced by its thermal properties—these not only determine how it behaves during the printing process but also influence the durability and functionality of the final products. Knowing the melting point and other thermal behaviors can make or break your project, especially when dealing with components intended for specific environments.
Melting and Glass Transition Temperatures
The melting point of Taulman Nylon 645 hovers around 220 degrees Celsius. This is an important temperature to keep in mind, as it indicates the point at which the material transitions from a solid to a liquid state, thus allowing for successful 3D printing.
Glass transition temperature (Tg), on the other hand, typically falls between 50-60 degrees Celsius. This is the temperature range at which the material begins to lose its rigid structure and becomes more rubbery and flexible. It’s crucial for designers to consider the operating environment’s temperature, as parts made from Nylon 645 will start to lose their structural integrity if exposed to temps nearing its Tg.
Key considerations regarding these temperatures include:
- Print Settings: Knowing these temperatures can assist with setting your printer’s nozzle temperature accurately for optimal results.
- Usability in Applications: Parts operating in higher temperature environments might need additional coatings or treatments to maintain their integrity.
- Thermal Stability: Understanding these characteristics helps in predicting the lifespan of parts under stress from heat.
"Choosing the right material means knowing how it behaves under temperature changes and stresses. Taulman Nylon 645 holds up well, but it’s vital to understand its limits."
Thermal Deformation
Thermal deformation refers to the physical changes a material undergoes when exposed to temperature changes. With Taulman Nylon 645, both mechanical and thermal stresses can lead to deformation. Here’s how it typically manifests:
- Creep: Over time, and under constant load, the material may slowly deform. This can spell trouble when using parts in critical load-bearing applications.
- Warping: This is a common challenge with many plastics during the cooling process, leading to variations in dimensions.
- Dimensional Stability: The heat history during printing impacts a part's final dimensions. Poor control can lead to unexpectedly oversized or undersized components.
By staying aware of thermal deformation, users can plan for proper cooling methods and post-processing plans to ensure parts maintain their designed specifications. Therefore, it’s suggested to allow printed parts to cool gradually rather than introducing them to abrupt temperature changes, which could exacerbate warping or bending.
In summary, the thermal properties of Taulman Nylon 645 are pivotal for both the printing process and the final application. Adequate knowledge and proper handling will yield better results and more satisfying project outcomes.
Applications of Taulman Nylon
The growing interest in Taulman Nylon 645 can be largely attributed to its versatility and how well-suited it is for various applications in the 3D printing Industry. Notably, this material is not just a niche product; it's carving a substantial place in both professional and hobbyist circles. Understanding its applications provides insight into why this nylon variant stands out in the crowded field of filament choices.
Functional Prototyping
When it comes to functional prototyping, Taulman Nylon 645 shines brightly. Its outstanding mechanical properties, like the ability to endure stress, make it perfect for creating prototypes that need more than just aesthetic appeal. For instance, engineers and designers routinely push the envelope with concept creations using this filament. Plus, the ease of printing combined with the nylon's durability means that prototypes can be tested in real-world conditions rather than just under sterile lab environments.
From automotive parts to intricate machinery components, this material serves as an excellent base for designs that have to operate under actual working conditions. The freedom to iterate and create without the fear of breaking can boost creativity and acceleration in product development. Whether it's a simple gear or a complicated housing unit, the endurance of Taulman Nylon 645 adds substantial value to the prototyping process.
End-Use Parts
In terms of end-user applications, Taulman Nylon 645 is often employed for parts that demand resilience and longevity. Take, for example, the realm of aerospace or automotive—components built with this nylon variant can withstand higher loads and environmental conditions than those created with standard PLA or even ABS.
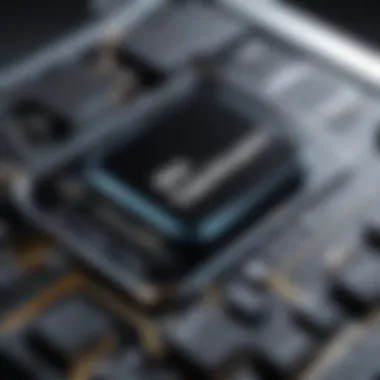
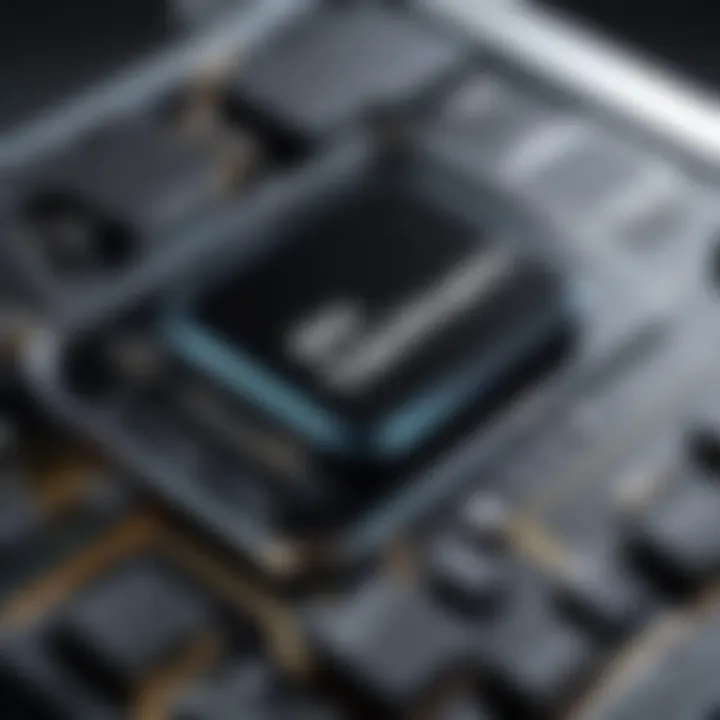
As industries continually seek materials that offer not just strength but also flexibility, Taulman Nylon 645 fits the bill through its balance of durability and workability. End-use applications often vary significantly across sectors; for instance, it could lead to functional parts for machinery, housing for delicate electronics, or specialized grips and fixtures, showing its adaptability. The takeaway here is that the efficacy and reliability of products crafted with this filament can be pivotal to project success.
Consumer Goods
Shifting to consumer goods, Taulman Nylon 645 finds its stride in a multitude of products that everyday users come into contact with. From durable phone cases to intricate home decor items, the potential applications are virtually limitless. Users appreciate the appeal of custom-made items that stand up to daily wear and tear.
Moreover, the aesthetic quality of prints made with this nylon is intriguing, allowing for a range of finishes that can elevate a design from ordinary to exceptional. Take the case of custom toy parts or unique household solutions; the strength and finish possible with Taulman Nylon 645 could lead to the creation of products that not only function but also delight the consumer sensibly.
"The intersection of utility and design makes Taulman Nylon 645 a prime choice for anyone eager to create lasting, functional consumer products."
In summary, the applications of Taulman Nylon 645 are as diverse as they are vital. Its role in functional prototyping helps bring ideas to life, while its strength as an end-use material offers simplicity and reliability in demanding environments. Finally, in the consumer goods sector, the combination of durability and aesthetic appeal is redefining possibilities for creativity and innovation. The filament is not just another option; it’s a powerful partner in achieving product success.
Best Practices for Printing with Taulman Nylon
When diving into the world of 3D printing with Taulman Nylon 645, having a solid grasp of the best practices is crucial. This material, known for its strength and durability, requires specific settings and techniques to maximize its advantages while minimizing potential printing failures. Understanding these best practices ensures not only a better printing experience but also higher quality end products. By adhering to certain guidelines, both newcomers and seasoned printers can capitalize on the unique properties of Taulman Nylon 645.
Printer Settings and Recommendations
Getting your printer dialed in for Taulman Nylon 645 is no small feat. Each machine varies, and what works for one may not translate well to another. Here are some best settings to seriously consider:
- Temperature Settings: It's essential to print at a nozzle temperature between 240°C and 260°C. Staying within this range helps in achieving optimum layer adhesion while reducing the risk of stringing.
- Bed Temperature: A heated print bed is non-negotiable. Set your bed temperature between 65°C and 75°C. This helps reduce warping and fosters better adhesion of the first layer.
- Speed Settings: Slower speeds often yield better results. Consider lowering the print speed to around 30-50 mm/s. This will contribute to more precise layer placement and reduce the chances of common issues like under-extrusion.
To put it plainly, proper adjustment of your 3D printer’s settings is a make-or-break factor when working with nylon, given its unique handling properties.
Adhesion Techniques
Getting that first layer right can often spell the difference between a successful print and a frustrating reprint. Taulman Nylon 645 can be finicky with surface bonding, so using effective adhesion techniques is paramount.
- Surface Material: A glass bed or a PEI surface can work wonders for adherence. Flat, smooth surfaces minimize lift during printing, especially for your initial layers.
- Adhesives: Utilizing adhesives like a glue stick or a specialized 3D printing glue can make a significant difference. It’s often wise to apply a thin layer on the bed to foster a strong grip and prevent warping as the print cools.
- Rafts or Brims: Consider adding a raft or brim to your print settings. Both options can help with achieving better adhesion. For larger prints, using a brim provides extra stability and prevents corners from lifting.
"Adherence to best practices can elevate your printing from good enough to exceptional. Do not underestimate the basics—it’s often where the magic happens."
Reinforcing these foundational practices and settings will ensure you're on the right track to maximizing the potential of Taulman Nylon 645. Being diligent from start to finish can yield functional prototypes and finished products that meet rigorous standards and expectations.
By investing time and effort into understanding and implementing these best practices, you can help position your projects for success!
Challenges with Taulman Nylon
Understanding the challenges associated with Taulman Nylon 645 is vital for anyone looking to utilize this material effectively in 3D printing. While its unique properties make it an appealing choice for many applications, being aware of its limitations can save time and reduce frustration.
Two primary issues often arise when working with Taulman Nylon 645: warping and shrinkage, as well as moisture sensitivity. Both of these factors can significantly influence print quality and performance, making it crucial to navigate them skillfully.
Warping and Shrinkage Issues
Warping and shrinkage during the printing process can cause a multitude of headaches for users of Taulman Nylon 645. These problems often manifest when the material cools unevenly after the extrusion. This differential cooling can lead to distortion, which may affect the dimensional accuracy of the printed part.
Common symptoms of warping include:
- Lifted Edges: Parts may curl up from the print bed, leading to poor adhesion.
- Inconsistent Layer Height: Variations as the print progresses can lead to a product that deviates from the intended design.
To combat these issues, here are some best practices:
- Use a Heated Bed: Keeping the print bed heated helps maintain consistent temperatures throughout the printing process.
- Print with a Brim or Raft: Adding these features can improve adhesion and minimize warping.
- Optimize Layer Cooling: Strategically managing fan speeds can prevent uneven cooling that leads to warping.
"With proper adjustments and foresight, users can mitigate the detrimental effects of warping and shrinkage in Taulman Nylon 645, leading to cleaner and more reliable prints."
Moisture Sensitivity
Moisture sensitivity is another critical challenge when dealing with Taulman Nylon 645. Nylon materials in general tend to absorb moisture from the air, which can lead to a myriad of printing dilemmas. The presence of moisture can result in bubbling, stringing, or poor layer adhesion.
Some key aspects to consider regarding moisture sensitivity include:
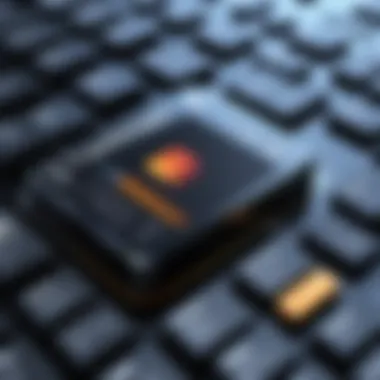
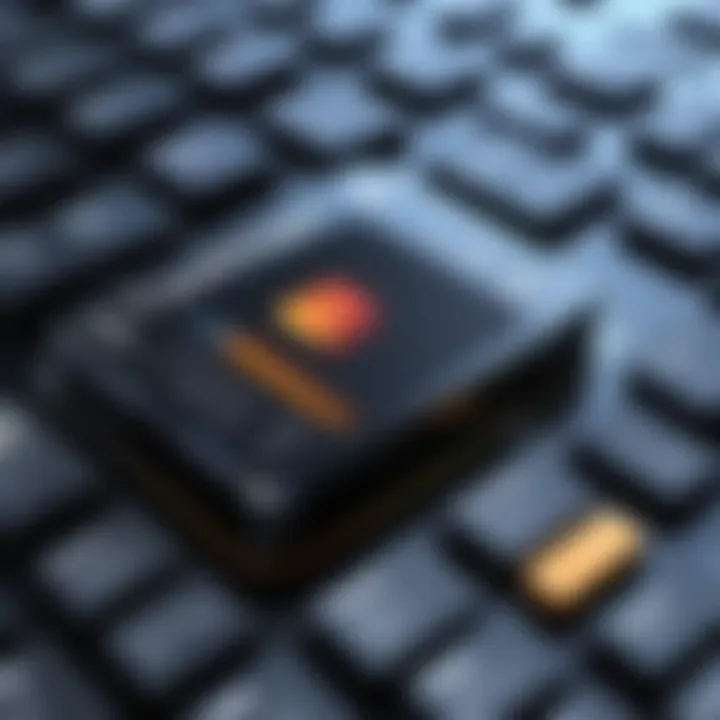
- Storage Conditions: Store Taulman Nylon 645 in a dry environment, ideally in a sealed container with desiccants to keep moisture at bay.
- Drying the Filament: If exposure has occurred, drying the filament in an oven at low temperatures can restore its properties.
- Monitor Humidity Levels: Keeping an eye on environmental humidity can help prevent issues before they arise.
Addressing moisture sensitivity not only boosts the quality of prints but also extends the life of the filament, ensuring that each project can be handled with precision and care.
Comparative Analysis with Other Nylon Variants
In the evolving landscape of 3D printing, understanding the nuances between different nylon variants can significantly impact the choice of material for specific applications. Here, we dive into the comparative analysis of Taulman Nylon 645 with other popular variations like Nylon 618 and Nylon X. This examination is pivotal for both hobbyists and professionals alike, as it lays the groundwork for informed decision-making when selecting materials that align with their project requirements. By exploring each variant's strengths and weaknesses, users can better appreciate the unique advantages that Taulman Nylon 645 offers.
Nylon vs Taulman Nylon
When considering Nylon 618 as an alternative, one should note several key differences that could inform material selection. Nylon 618 is generally recognized for its excellent flexibility and impact resistance, making it a favorite among many in the prototyping arena. However, Nylon 645 often stands out for its superior strength and thermal stability.
- Strength and Durability: Taulman Nylon 645 showcases enhanced tensile strength than Nylon 618. This durability makes it ideal for applications requiring robust performance, like mechanical parts or functional components subjected to stress.
- Ease of Printing: When it comes to printing, users often find Taulman Nylon 645 a bit more manageable than Nylon 618, which can sometimes be prone to significant warping and curling. A stable print is paramount, particularly for intricate designs.
- Applications: If we look deeper, Nylon 618 is commonly used for softer, more flexible end-use products. In contrast, Nylon 645 is perfect for parts that demand not just flexibility but structural integrity over time.
In summary, while Nylon 618 has its merits, 3D printing enthusiasts may lean towards Nylon 645 when the need arises for enhanced performance under duress.
Comparison with Nylon and Others
Moving on to Nylon X, we unearth yet another layer of complexity. Nylon X is a composite material that typically blends nylon with carbon fiber.
- Material Composition: The addition of carbon fiber offers exceptional stiffness and reduces the weight of parts created. However, these benefits often come at a premium price and can complicate the printing process due to the aggressive nature of the carbon fibers which require specialized nozzles. Taulman Nylon 645, on the other hand, remains a pure nylon option that delivers reliable performance without the additional expense or complexity.
- Printability: Experiences reported by users indicate that while Nylon X is favored for advanced engineering applications, Taulman Nylon 645 provides better print consistency, particularly for detailed intricate designs. Each filament has its quirks, but Taulman’s formulation often shows less tendency to clog print heads, allowing for smoother operation in standard FDM printers.
- Cost Considerations: There’s also the factor of cost. In many cases, Nylon X will set you back considerably more than Taulman Nylon 645. Given that many DIY projects or even smaller-scale production runs may not justify the expense, sticking with the Taulman brand often allows for more cost-effective solutions.
In closing, the choice between Taulman Nylon 645 and other nylon variants ultimately comes down to specific project needs. Whether it be functionality, cost-effectiveness, or printability, understanding these comparisons can guide users to make more informed decisions, ensuring they select the right material for the job.
"In the realm of 3D printing, the right material can make all the difference, impacting performance, cost, and overall success of a project. "
Cost Effectiveness of Taulman Nylon
Understanding the cost-effectiveness of Taulman Nylon 645 is crucial for makers, hobbyists, and professionals looking to make informed decisions in their 3D printing projects. The choice of material often hinges not just on performance characteristics, but also on how economic it is in relation to both project requirements and budget constraints. This section seeks to illuminate the key elements influencing the overall costs as well as the long-term value brought by this specific nylon variant in various applications.
Material Costs
When discussing material costs, it’s important to consider both the initial purchase price and the overall expenditure involved in the utilization of Taulman Nylon 645. On average, the cost per kilogram for Taulman Nylon 645 falls within a competitive range compared to other nylon filaments. However, like many specialized materials, prices can fluctuate based on market demand and supplier options.
- Comparison with Other Filaments: While basic PLA or ABS options may come at a lower price point, the unique properties of Taulman Nylon 645—such as its strength and flexibility—can justify the investment. This filament stands out in applications where durability is paramount.
- Bulk Purchase Benefits: For larger projects or frequent usage, buying in bulk could yield significant savings. Many suppliers offer discounts on larger quantities, effectively reducing the cost per kilogram.
- Production Wastage: Unlike some standard filaments that may need extensive post-processing, Taulman Nylon 645 allows for more detailed precision, potentially lowering waste and costs in the long run.
It's essential to weigh these factors against the specific requirements of each project to ensure the selected filament aligns with both budgetary constraints and desired outcomes.
Value in Prototyping
Beyond pure material costs, the value of Taulman Nylon 645 shines brightly in the world of prototyping. It’s not merely about the sticker price but also how well the material performs in various applications, which counts towards its overall value proposition.
The key aspects to consider include:
- Durability and Performance: Projects requiring strong working prototypes can depend on Taulman Nylon 645’s robust mechanical properties. This means less need for over-engineering designs, thus saving both time and material.
- Iterative Design Process: Prototyping is often about multiple iterations. Using Taulman Nylon 645 balances the fine line between producing quick mock-ups and reliable prototypes that can withstand functional testing.
- Cost Savings Over Time: While the initial material cost might be on the higher side, fewer failures during printing or testing can drastically cut down on the total cost over multiple iterations of a design, ultimately offering greater value when viewed holistically.
"In the end, the real cost of a material isn't its price tag; it's the value it delivers through the life of the project."
By understanding how material costs and value intersect, one can more effectively harness the strengths of Taulman Nylon 645 for a variety of applications.
Future Trends in Nylon 3D Printing
The evolution of 3D printing using nylon materials, especially Taulman Nylon 645, has propelled various sectors into a future filled with possibilities. As technological advancements continue to reshape manufacturing and design paradigms, staying abreast of the future trends in nylon 3D printing is crucial for professionals and enthusiasts alike. Knowing these trends not only helps in selecting the best materials for specific applications but also opens doors for innovative approaches to design and production.
With its unique properties, Taulman Nylon 645 has already shown its potential in several avenues, but understanding what lies ahead can provide even greater potential benefits for users. The advancements in material science and the integration of nylon with composite materials are particularly noteworthy.
Advancements in Material Science
In recent years, the field of material science has made remarkable strides, which directly influence how nylon is used in 3D printing. New formulations are being developed that enhance the characteristics of nylon filaments. For instance, researchers are experimenting with blending nylon with various polymers to improve thermal stability, flexibility, and impact resistance.
- Enhanced Thermal Properties: New nylon composites can endure higher temperatures without compromising their structural integrity. This opens new doors for applications requiring heat resistance.
- Improved Mechanical Strength: Upcoming blends appear to be enhancing mechanical properties for greater durability in demanding environments.
- Sustainability Efforts: A focus on biodegradable materials is taking root. Some new nylon formulations are being developed to reduce environmental impact.
These advancements are shaping the future of nylon in additive manufacturing, allowing designers to create stronger, more reliable, and environmentally friendly parts.
Integration with Composite Materials
The integration of nylon with composite materials presents new opportunities in 3D printing, virtually redefining what’s possible in manufacturing. By combining Taulman Nylon 645 with materials such as carbon fiber or glass fiber, manufacturers are able to produce parts that harness the best attributes of both.
- Increased Strength-to-Weight Ratio: Composite nylon materials can dramatically increase strength while remaining lightweight—ideal for aerospace or automotive applications.
- Tailored Properties: Mixing nylon with different composite materials allows for customization in terms of rigidity, flexibility, and weight, leading to more tailored designs suited to specific project needs.
- Broadening Application Spectrum: The diverse properties of composite materials mean that Taulman Nylon 645 can be used more effectively across a broader range of industries, from medical devices to consumer electronics.