Cut Pile Machines: Revolutionizing Textile Production
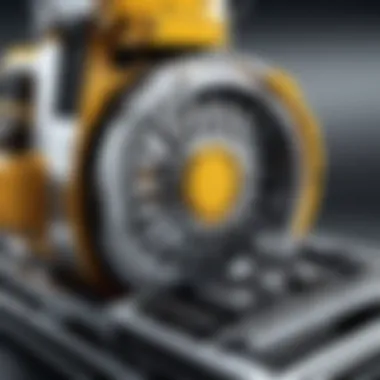
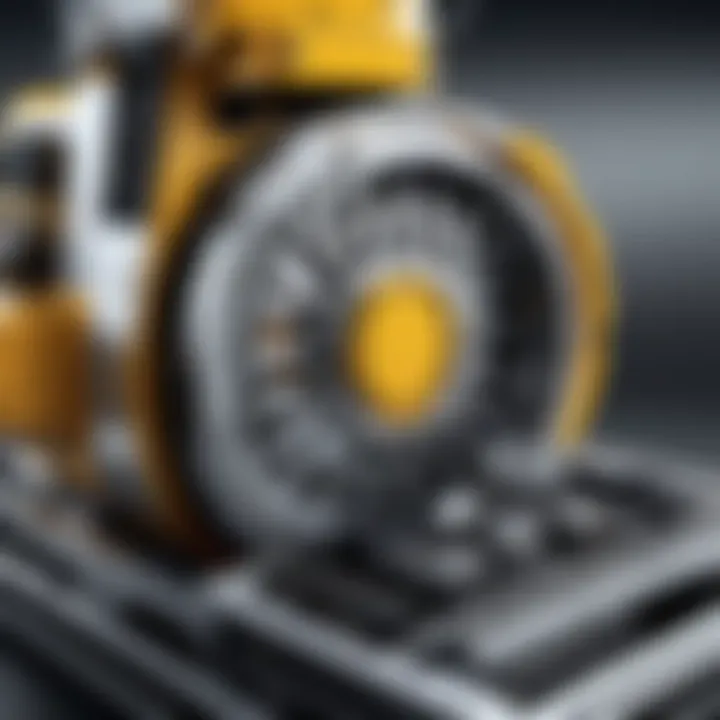
Intro
Cut pile machines have an important role in the textile industry, facilitating the production of various fabric types. Understanding their evolution and functionality gives insight into their significance for modern manufacturing processes.
These machines have undergone significant changes over time, adapting to technological advancements and market demands. Today, they are critical for creating high-quality textiles with unique textures and designs. This article aims to explore the complexities behind cut pile machines, their operational principles, and their contributions to the efficiency and quality of textile production.
Technical Specifications
Understanding the technical specifications of cut pile machines is essential for anyone involved in textile production. These details provide insights into their capabilities and help in selecting the right machine for specific tasks.
Detailed Product Specs
Cut pile machines vary widely in specifications. Common attributes include:
- Model Type: Electronic or mechanical
- Cut Pile Height: Typically adjustable, ranging from 4mm to 20mm
- Working Width: Commonly between 1.5 meters to 4 meters
- Production Speed: Often exceeds 1000 meters per hour
Performance Metrics
Performance metrics are crucial to measuring how effectively a cut pile machine operates. Metrics include:
- Efficiency Rate: Percentage of fabric produced without defects
- Uptime: Total operational time as opposed to downtime
- Energy Consumption: Both power and cost related to usage
Compatibility Information
Machines must be compatible with various materials and processes. For instances:
- Material Types: Cotton, polyester, and blends
- Software Compatibility: Integration with design programming for custom patterns
- Maintenance Tools: Specific tools required for repair or upkeep
Practical Applications
Cut pile machines are utilized in various settings within the textile industry. Their applications range from small workshops to large-scale production facilities.
Use Cases for Different Users
Different users benefit from cut pile machines in diverse ways. For garment manufacturers, these machines aid in creating luxurious textiles for high-end markets. Carpet producers leverage them for durability and texture.
Recommended Configurations
Configuration options focus on user needs. For instance:
- Basic Setup: Suitable for small-scale operations with limited production demands.
- Advanced Configuration: Ideal for large manufacturers requiring higher speeds and efficiency.
Multi-Platform Performances
Cut pile machines often need to work alongside other equipment. For better production capability, integrating with knitting machines, dyeing machines, and finishing units can enhance overall output quality.
Latest Trends
The landscape of cut pile machines is continually changing. Keeping abreast of the latest trends can inform decisions in investment and operation.
Industry Developments
Recent developments include:
- Focus on automation for better efficiency
- Enhanced cutting technology for precise control
- Sustainable materials being used in machine components
Emerging Technologies
Technological advancements are seen with:
- Smart machines that incorporate IoT for monitoring
- AI-driven design processes that optimize fabric creation
Future Predictions
Looking ahead, the industry is likely to witness:
- Increased investment in energy-efficient machines
- A shift toward customization and niche markets
Buying Guides
When considering the purchase of a cut pile machine, informed choices are important. Understanding what to look for can streamline this process.
Recommended Products
Some well-known cut pile machines include brands like MΓΌller and Baldwin, known for their efficiency and durability.
Purchasing Tips
- Assess production needs carefully
- Compare specifications meaningfully
- Inquire about warranty terms and after-sale support
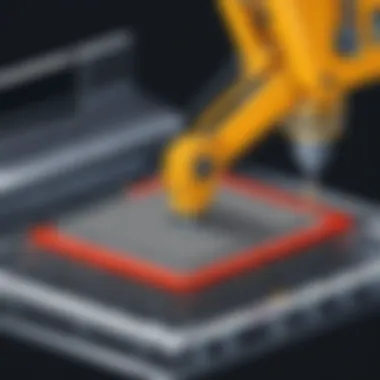
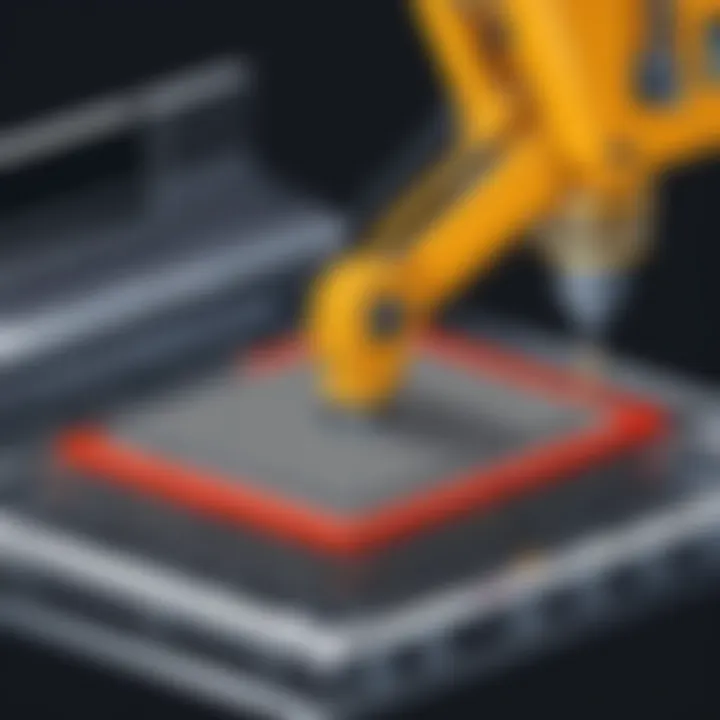
Warranty and Support Information
Ensure that warranty terms are clear. Look for manufacturers providing solid support options. It minimizes risks and aids in timely maintenance.
Preamble to Cut Pile Machines
Cut pile machines play a vital role in the textile manufacturing industry. Their significance lies not only in the fabric's appearance but also in the efficiency and quality of production. These machines create a unique texture by cutting loops of yarn, producing a range of products from carpets to plush textiles.
Understanding cut pile technology involves recognizing the benefits it offers. Firstly, it provides versatility in design and texture. Manufacturers can create varied pile heights and densities, influencing the final product's look and feel. Secondly, efficiency is enhanced as these machines automate a complex process that was once labor-intensive.
Moreover, there are several considerations when operating cut pile machines. It is crucial to know the specific material requirements and maintenance practices. Failure to adhere to these can lead to production delays or quality issues. Thus, an in-depth exploration of cut pile machines contributes significantly to optimal textile production.
Understanding Cut Pile Technology
Understanding cut pile technology involves delving into the mechanisms that allow for the cutting of yarn. Machines typically employ blades or knives that slice through yarn loops, creating a uniform pile. The depth and angle of the knife play significant roles in determining the final texture.
This technology integrates various features. For instance, some machines include programmable settings, allowing manufacturers to adjust pile height or pattern based on production needs. While traditional methods focus on manual labor, modern cut pile technology emphasizes automation and precision. This reduces human error and boosts production speed.
Key Features:
- Automated cutting mechanisms
- Adjustable pile height settings
- User-friendly interfaces for operation
Historical Development of Cut Pile Machines
The historical evolution of cut pile machines dates back to the late 19th century. Early models were simple devices that required significant manual intervention. However, as textile technology progressed, machines became more sophisticated.
The introduction of electricity in textile manufacturing revolutionized these machines. Electric cutting mechanisms replaced hand-operated blades, increasing speed and efficiency. Over time, innovations such as programmable logic controllers were integrated, allowing for greater customization in textile production.
The trajectory of cut pile machine development highlights the shift from manual to automated processes, emphasizing the importance of technological advancements in boosting production capabilities.
This growth is vital as it reflects broader trends within the textile industry. Competitiveness hinges on the ability to produce high-quality products swiftly and cost-effectively. With each advancement, cut pile machines have continued to shape production practices, enabling manufacturers to meet evolving consumer demands.
Types of Cut Pile Machines
The landscape of textile production is significantly shaped by the various types of cut pile machines. Each machine type serves distinct functions and caters to specific production needs. Understanding these differences is crucial for manufacturers aiming to optimize their operations. This section will explore the three main categories of cut pile machines: single-cut, double-cut, and electronic machines. Each has unique advantages and considerations that affect the overall efficiency, cost, and quality of textile products.
Single-Cut Pile Machines
Single-cut pile machines are fundamental to the cut pile process. They operate by introducing a single blade that cuts into the pile yarn at a consistent height. This method results in a single lush layer of cut pile, making it a popular choice for manufacturers who prioritize simplicity and reliability in their production lines. The design and mechanism of single-cut pile machines are typically straightforward, which aids in lower operational and maintenance costs.
One significant advantage of single-cut systems lies in their ability to produce fabrics that have a soft, plush texture. This feature is particularly desirable in textile markets focused on comfort and luxury. Additionally, these machines generally have a higher throughput compared to more complex systems, which allows for quicker production cycles.
However, single-cut machines may face limitations in producing intricate patterns or textures. Their relatively straightforward functionality may not meet the demands of textile designers looking for unique fabric structures.
Double-Cut Pile Machines
Double-cut pile machines take the evolution of cut pile technology a step further. By employing two cutting mechanisms, these machines can achieve greater versatility in yarn lengths and textures. The dual-blade system allows for a more refined cut and creates a denser pile, adding depth and structure to the fabric.
The benefits of these machines are particularly notable in applications such as carpet manufacturing or high-end upholstery. Double-cut machines allow for the creation of various patterns and textures, meeting consumer demands for customization and uniqueness in textile products.
However, the complexity of the machinery means higher initial investment costs and often more extensive maintenance. Manufacturers must weigh the benefits of production flexibility against the demands of operating and maintaining more advanced technology.
Electronic Cut Pile Machines
Electronic cut pile machines represent the pinnacle of technology in this category. Incorporating digital controls and automated systems, these machines offer superior precision in cutting and pile construction. Operators can adjust settings through a user-friendly interface, allowing for seamless production changes.
The primary benefit of electronic systems is their enhanced ability to produce intricate designs and varying pile heights with minimal manual intervention. This can lead to greater efficiencies in production, as well as improved consistency and quality across batches. Moreover, electronic machines often feature integrated quality control systems that monitor output in real time, ensuring high standards are met continuously.
Yet, the sophistication of electronic cut pile machines come with drawbacks. Such technology incurs significant upfront costs, and manufacturers need ongoing technical support and training for their personnel. Despite these challenges, the potential for larger profit margins through high-quality output makes electronic solutions attractive for many textile producers.
In summary, the variety in cut pile machines allows manufacturers to select equipment that aligns with their specific production goals, from straightforward single-cut systems to advanced electronic models.
Components of a Cut Pile Machine
Understanding the components of a cut pile machine is essential for grasping their functionality and efficiency in textile production. Each part plays a vital role in the overall operation, making it critical to familiarize oneself with these elements for both practical application and theoretical exploration.
Cutting Mechanism
The cutting mechanism is at the heart of a cut pile machine. It is responsible for creating the desired pile height, which directly impacts the texture and appearance of the fabric. This mechanism often utilizes sharp blades or knives to cut the fibers at precise angles and lengths.
The precision of the cutting mechanism determines the quality of the end product. A well-functioning mechanism can yield a uniform pile, enhancing the aesthetic appeal of the textile. Moreover, advanced cutting systems can adapt to different materials, allowing for greater versatility in production. This adaptability is crucial in a market that demands varied textures and finishes.
Regular maintenance of the cutting mechanism is necessary to avoid wear and tear, ensuring consistent performance over time. Minor adjustments, such as blade sharpening, significantly affect the overall efficiency and quality of production.
Feeding System
Next is the feeding system, which is responsible for guiding the fabric into the cutting area. An efficient feeding system allows for uninterrupted operation and smooth material flow. It can define the speed and consistency of production, making it a crucial component.
Different types of feeding mechanisms, such as roller systems or conveyor belts, can be used depending on the machine's design. These systems need to be calibrated accurately to accommodate various fabric types. Misalignment or inconsistent feeding can result in defects, such as uneven piles or damaged fibers.
Moreover, a well-designed feeding system arranges fibers in a specific orientation, which enhances the performance of the cutting mechanism. This synergy between the feeding system and the cutting mechanism is essential for achieving high-quality outputs.
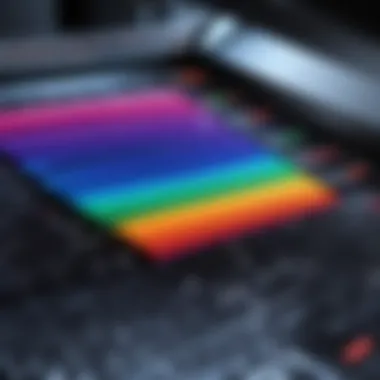
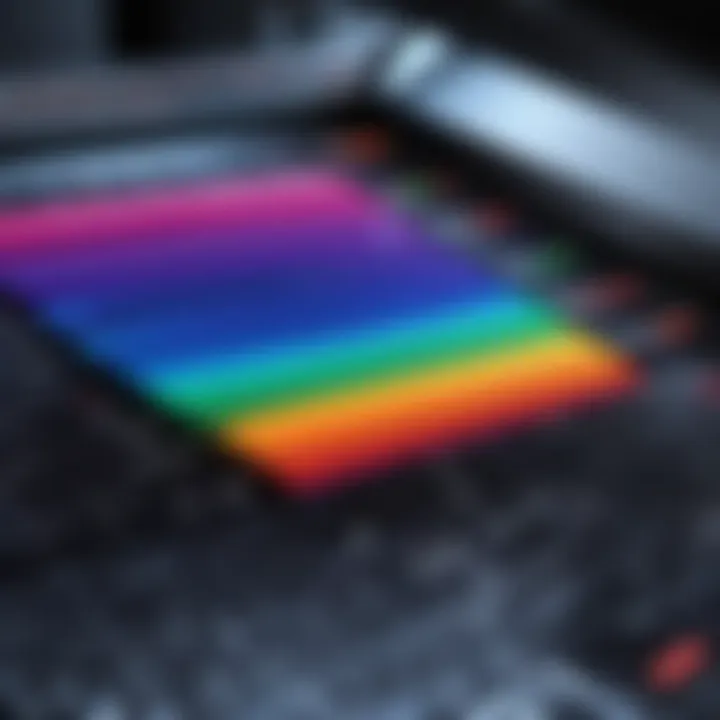
Control Panel and User Interface
The control panel and user interface serve as the operator's primary point of interaction with the cut pile machine. A straightforward and intuitive design can significantly enhance user experience. Operators can monitor settings, adjust parameters, and troubleshoot issues with ease.
Modern machines often feature digital interfaces that allow for real-time monitoring. These interfaces can display crucial information such as cutting speed, feed rate, and machine status, enabling operators to make quick decisions. The ability to program specific settings for different types of fabrics further enhances efficiency.
Additionally, training operators to effectively use these controls is vital. Poor handling can lead to mistakes, resulting in subpar products. A user-friendly interface minimizes the likelihood of errors, making it an important design consideration.
Operational Principles
Understanding the operational principles of cut pile machines is essential for grasping their role within the textile industry. These principles dictate how machines function and the efficiency with which they produce materials. By recognizing how these machines manipulate fibers, one can appreciate both the technological advancements in this field and the quality of the final product.
Mechanics of Cut Pile Production
Cut pile production involves several key mechanical processes. The primary mechanism is the cutting tool that dissects the pile yarn loops to create a uniform surface. Typically, the mechanism can be categorized into blade and knife systems, each with their own strengths.
- Feeding Mechanism: This part ensures that the textile material is fed into the machine correctly. An efficient feeding system minimizes tension and prevents errors in the cutting process, directly affecting the outcome.
- Cutting System: The cutting tools operate at variable speeds depending on the type of material. Speed plays a crucial role in ensuring clean cuts, reducing fraying, and maintaining the integrity of each pile. Some modern machines use advanced technologies, such as ultrasonic cutting, which enhances precision.
- Adjustable Height Settings: Different pile heights can be achieved by altering the machine settings. This flexibility allows manufacturers to cater to various textile designs and requirements efficiently. Improved adaptability is crucial for meeting customer demands in diverse textile markets.
These interlinked mechanisms contribute to the efficacy of cut pile production, making it essential to implement regular maintenance to avoid downtime and ensure optimum function.
Quality Control Measures
Quality control is a critical element in the operational principles of cut pile machines. Implementing strict quality measures guarantees that the final product meets industry standards.
Effective quality control ensures product reliability and customer satisfaction.
- Material Inspection: Before production, raw materials are examined for defects. Any flaws present in the initial stages can affect the integrity of the final product.
- Monitoring Production Processes: Real-time monitoring helps in identifying issues promptly. Operators can adjust settings or halt production if subpar conditions arise.
- Final Product Evaluation: After the cut pile is produced, thorough inspections are conducted. Assessing pile height, density, and overall appearance ensures that the product adheres to quality standards.
- Statistical Process Control (SPC): Utilizing SPC tools helps in statistical analysis of the production process. This method evaluates variations and enhances the predictability of the manufacturing outcomes.
Incorporating these quality control measures maximizes production efficiency and minimizes waste, offering a competitive edge in the textile market. By focusing on both the mechanics of production and quality assessment, manufacturers can optimize their cut pile operations effectively.
Applications of Cut Pile Machines
The applications of cut pile machines in textile production are vast and significant. This technology plays a crucial role in creating a range of products that require cut pile fabrics. The efficiency and precision of these machines enhance productivity while ensuring high-quality output. Understanding where and how these machines are employed gives valuable insight into their impact on the industry.
Textile Fabrication
Cut pile machines are integral to textile fabrication, where they transform raw materials into finished fabrics. These machines allow for the production of a variety of textile goods, ranging from apparel to industrial fabrics. The mechanism of cutting the pile yarn results in a soft, plush texture that is highly sought in the textile market.
- Versatility: The ability to process different fiber types, including natural and synthetic fibers, makes cut pile machines versatile. This adaptability allows manufacturers to cater to diverse consumer demands.
- Texture and Quality: The cut pile technique is favored for its ability to create distinct textures. The cut ends of the yarn produce a uniform surface, enhancing the fabric's aesthetic appeal.
- Speed and Efficiency: These machines operate at high speeds, significantly increasing production rates compared to manual methods. This efficiency reduces turnaround times for textile orders.
Carpets and Rugs Production
In the carpet and rugs sector, cut pile machines hold substantial importance. They enable the mass production of floor coverings with varying designs and textures. The following points highlight how they contribute to this particular application:
- Design Flexibility: Manufacturers can create intricate patterns and styles, appealing to numerous market segments. This adaptability helps in meeting consumer preferences.
- Durability: Cut pile carpets are generally more durable than loop pile alternatives. By cutting the yarn, manufacturers achieve a softer finish that withstands foot traffic better over time.
- Easy Maintenance: The cut pile style is easier to clean and maintain. The texture prevents dirt from getting trapped, making it a practical choice for households and businesses alike.
"Cut pile carpets provide a unique blending of comfort and durability, making them a preferred choice for many consumers."
Upholstery and Home Textiles
Cut pile machines are also crucial in the upholstery and home textiles sector. Their functionality provides a means to produce a variety of textures and finishes suitable for furniture and decorative items.
- Aesthetic Value: Upholstered items with cut pile fabrics are often more visually appealing. Consumers are drawn to the rich textures and softness.
- Fabric Variety: From velvets to plush materials, cut pile machines can produce a wide range of upholstery fabrics that enhance the design of home interiors.
- Comfort and Functionality: The soft pile enhances comfort for furniture use while maintaining the structural integrity needed for upholstery applications.
In summary, the versatility and functionality of cut pile machines in various textile applications underline their importance in modern textile production. As the demands for high-quality fabrics grow, these machines will continue to evolve, ensuring they meet new challenges in the textile industry.
Economic Impact of Cut Pile Machines
Cut pile machines hold significant economic value in the textile industry. Their efficiency and productivity influence a company's profitability directly. Understanding the economic impact of these machines helps stakeholders make informed investment decisions. Factors such as initial costs, operating expenses, and maintenance issues play essential roles in evaluating their overall worth.
Initial Investment Considerations
When contemplating the purchase of cut pile machines, the initial capital investment is a key factor. The price of these machines can vary widely based on several elements:
- Type of Machine: Single-cut, double-cut, and electronic machines can differ greatly in cost.
- Brand and Features: Renowned brands with advanced features typically command higher prices, but might offer better reliability and efficiency in production.
- Customization: Custom-built machines can have steep initial costs, yet they can also be tailored to solve specific production challenges.
Investors must also consider the potential return on investment. An advanced cut pile machine may have a high upfront cost but can lead to lower labor costs and higher throughput. This potential for increased profit margins can justify a larger initial expense.
Operating Costs and Maintenance
Ongoing operating costs and maintenance are critical in evaluating the economic impact of cut pile machines. These aspects can significantly affect profitability over time.
- Energy Consumption: The efficiency of the machine affects utility costs. Machines that consume less power will lower ongoing expenses.
- Material Use: Efficient machines reduce waste in fabric, lowering material costs.
- Labor Costs: Although machines automate many processes, skilled operators are still needed. Understanding the balance of machine efficiency and labor requirements is vital for maintaining low operating costs.
- Repair and Maintenance: Regular maintenance can prevent costly breakdowns. Companies must allocate resources for routine inspections and potential repairs. Building a strong relationship with suppliers of parts is also beneficial, ensuring faster service when issues arise.
Properly maintained cut pile machines not only enhance production efficiency but also significantly impact the bottom line of textile manufacturers.
Advancements in Cut Pile Production
Advancements in cut pile production play a significant role in the textile manufacturing landscape. These innovations not only improve efficiency but also enhance the quality of the finished products. In recent years, the focus has shifted towards incorporating technology and eco-friendly practices into traditional methods. This chapter examines the critical elements of such advancements, detailing the benefits and considerations they bring to the production process.
Technological Innovations
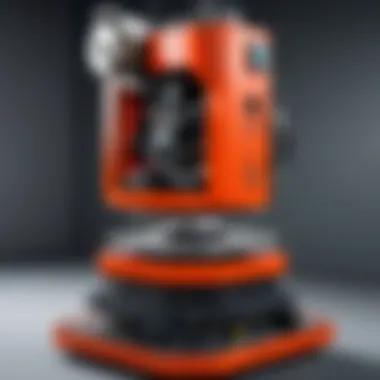
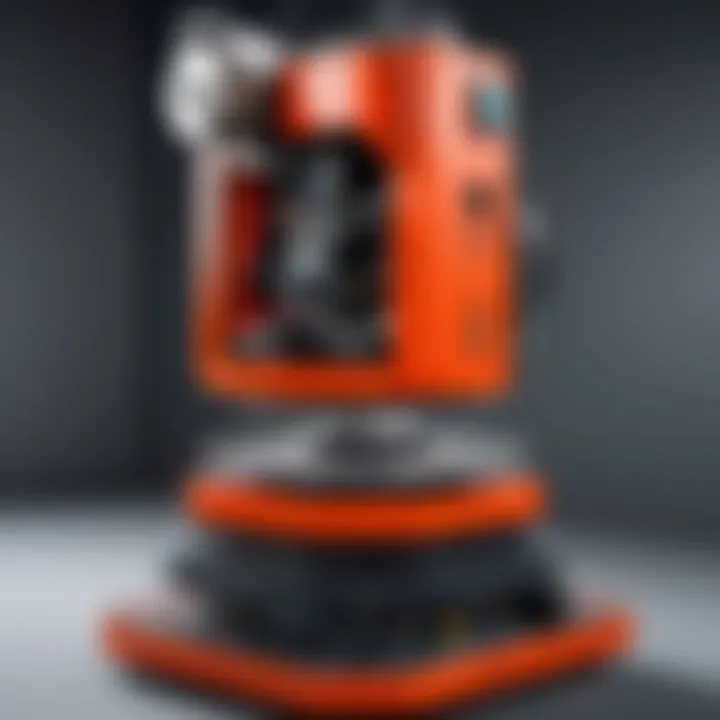
Technological innovations in cut pile machines represent a leap forward for the textile industry. Modern machines have integrated sophisticated electronics for precision and control. For example, new electronic cut pile machines can adjust cutting height automatically. This feature allows for consistent pile lengths, improving the overall quality of products.
Additionally, automation is becoming more prominent. Machines equipped with automation features reduce human error and increase speed. They enable manufacturers to produce large volumes without sacrificing quality.
Some key innovations include:
- Computerized control systems: These systems allow for precise settings and adjustments, improving production rates.
- Advanced sensors: Real-time feedback on the cutting process can help optimize performance.
- Data analytics: By tracking machine performance, manufacturers can implement timely maintenance, reducing downtime.
These innovations ensure that textile production meets the rising demands for quality and efficiency in todayβs market.
Sustainability Initiatives
Sustainability initiatives within cut pile production focus on minimizing environmental impacts and optimizing resource usage. As consumers become more aware of environmental issues, the textile industry must adapt to changing demands. This involves utilizing sustainable materials and energy-saving practices in production processes.
Some important sustainability practices include:
- Use of recycled fibers: Incorporating recycled materials not only reduces waste but also promotes a circular economy.
- Energy-efficient machines: Newer models are designed to consume less power, significantly lowering the carbon footprint of production facilities.
- Reduced waste protocols: Optimizing cutting techniques can decrease fabric waste during production.
Promoting sustainability in cut pile manufacturing not only meets regulatory requirements but also enhances brand reputation, attracting a more eco-conscious consumer base.
In essence, stand-alone technological advancements coupled with sustainability initiatives are reshaping how cut pile production operates, fostering a more efficient and responsible textile industry.
Maintenance of Cut Pile Machines
Maintaining cut pile machines is essential for ensuring their efficiency and longevity in textile production. Proper maintenance reduces downtime, enhances performance, and ultimately contributes to the quality of the finished products. Understanding the specific elements involved in maintenance can provide significant benefits for manufacturers, keeping the machines in optimal condition while minimizing repair costs. Routine care and attention can extend equipment lifespan, which is crucial in an industry where reliability is paramount.
Routine Inspections
Routine inspections form the backbone of an effective maintenance program for cut pile machines. These inspections should be conducted regularly, following a pre-defined schedule that aligns with the machineβs operational hours. During an inspection, operators should check various components, including the cutting blades, feeding systems, and electrical connections.
Key aspects to assess during routine inspections:
- Blade Condition: Check for dullness or damage that may affect cutting efficiency.
- Feeding Mechanism: Ensure smooth operation and alignment to prevent fabric jams.
- Electrical Connections: Inspect for loose or worn wires that could lead to system failures.
Timely detection of any issues can prevent larger problems down the road. Implementing a checklist could help streamline this process and ensure nothing is overlooked.
Troubleshooting Common Issues
Even with routine maintenance, cut pile machines can encounter issues that may disrupt production. Troubleshooting these common problems requires a systematic approach, starting with identifying symptoms.
Common issues that may occur include:
- Inconsistent Pile Height: Often caused by improper feeding or dull blades.
- Fabric Jamming: Usually a result of misalignment in the feeding system.
- Electrical Failures: May involve blown fuses or malfunctioning controls.
To effectively troubleshoot, consider the following steps:
- Identify the Symptom: Understand what is happening with the machine.
- Review the Manual: Each machine model comes with specific guidelines for troubleshooting.
- Check for Common Issues: Look for the problems mentioned above.
- Replace Components if Necessary: Dull blades or faulty parts should be replaced promptly.
Regular maintenance and prompt troubleshooting not only promote efficiency but also enhance the overall productivity of textile production.
Future Trends in Cut Pile Technology
The evolution of cut pile machines continues to shape the textile industry. Understanding future trends in this technology is vital for manufacturers seeking to optimize operations and adapt to market demands. These developments can lead to improved efficiency, enhanced product quality, and sustainability in textile production.
Emerging Designs and Features
The future of cut pile technology is marked by innovative designs that prioritize efficiency and adaptability. Some notable emerging features include:
- Integrated Smart Technology: Machines are incorporating sensors and automated controls for real-time monitoring and adjustments. This technology enhances precision in cutting and reduces waste.
- Modular Design: Future cut pile machines may feature modular components that allow for easy upgrades. This flexibility ensures manufacturers can stay current with technological advancements without replacing entire systems.
- Energy-efficient Systems: As environmental concerns grow, energy consumption is coming to the forefront. Future designs may focus on lower energy needs while maintaining output quality.
Such changes not only streamline production but also address sustainability, a growing directive in the industry.
Market Implications and Growth Projections
The market for cut pile machines is expected to undergo significant growth in the coming years, driven by various factors. Key implications include:
- Increase in Demand for High-Quality Textiles: As consumers seek better quality products, manufacturers must invest in advanced cut pile technology. This demand trends towards higher standards in textile production.
- Global Expansion of Textile Markets: Emerging markets in Asia and Africa present opportunities for cut pile machine manufacturers. Increased production in these regions will likely stimulate demand for more efficient machines.
- Investment in Research and Development: Companies are prioritizing R&D to innovate and keep pace with competitors. This focus is critical as new features and technologies are rolled out.
Overall, the future of cut pile technology is promising, with advancements likely to play a significant role in the evolution of the textile industry. As firms align with these trends, they can better meet consumer demands and enhance their production capabilities.
End
In reviewing the evolution and functionality of cut pile machines, it is essential to understand their significance in modern textile production. These machines have advanced from rudimentary designs to sophisticated systems, enhancing productivity and quality in the industry.
Summary of Key Points
The examination of cut pile machines reveals several critical aspects:
- Technological Advancements: Continuous innovations have led to improvements in efficiency, resulting in faster production times and enhanced fabric quality.
- Diverse Applications: Cut pile machines serve a wide variety of textile applications, from carpet manufacturing to upholstery, showcasing their versatility.
- Economic Impact: Investing in cut pile technology can be financially beneficial in the long run. The operational efficiency and reduction in waste contribute to lower long-term costs.
- Maintenance Requirements: Regular upkeep ensures optimal performance, highlighting the importance of knowledgeable staff in the maintenance process.
The Role of Cut Pile Machines in the Textile Industry
Cut pile machines are not merely tools; they are pivotal elements that shape the textile landscape. They enhance the ability of manufacturers to create high-quality products while minimizing production times. Moreover, the flexibility in designs achieved through modern cut pile technology allows firms to cater to evolving consumer demands.
The relevance of these machines in the textile industry cannot be overstated. They facilitate the production of diverse types of fabrics, thus meeting the growing consumer market. As sustainability becomes a central theme, cut pile machines also contribute to eco-friendlier practices by reducing fabric waste.
In summary, cut pile machines have transformed the textile manufacturing process, adding significant value and efficiency. Their continued evolution reflects changing market needs and demonstrates the industry's adaptability to new technologies. Embracing these advancements is crucial for any business aspiring to thrive in the competitive textile sector.